Insights
Insights: Timo Vesala, Account Manager, ABB Marine & Ports
Timo Vesala, Account Manager, Americas, at ABB Marine & Ports, is responsible for newbuild sales in the Americas market. Since joining ABB in 2018, he has gathered extensive experience in the marine industry with a focus on electrification and propulsion systems. He holds a Master’s Degree in Mechanical Engineering from Aalto University, Finland, and has a passion for clean technology and maritime decarbonization. This month, in our annual Power & Propulsion edition, he weighs in on the way forward to a greener global waterfront.
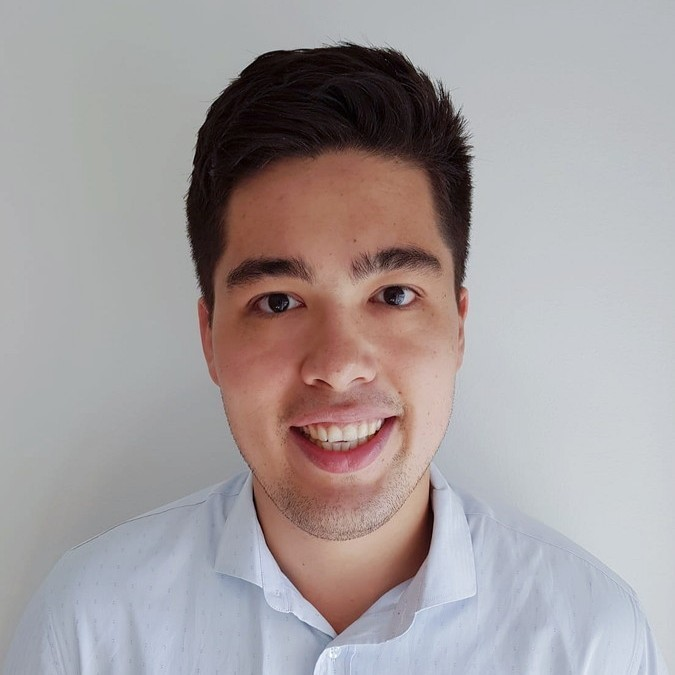
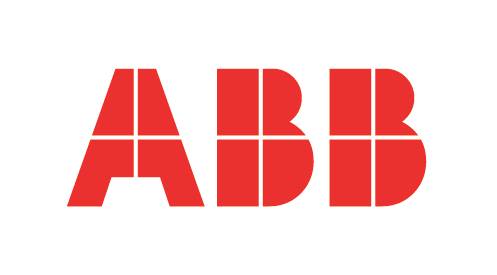
All American Marine and ABB recently collaborated on new hybrid-electric ocean sampling vessel in California. Tell us about that project and how it came about.
We are excited to collaborate with All American Marine on this innovative project for Orange County Sanitation for their new ocean sampling vessels. This 19.8-meter vessel has been designed by Auckland based naval architect Teknicraft to support Orange County Sanitation District’s ocean monitoring program that has run for over 40 years in support of wastewater collection, treatment, disposal, and recycling services for 2.6 million residents of Orange County, CA. The program operates around 90 days each year, verifies that the Pacific Ocean remains safe for swimming, marine life and fisheries.
- https://new.abb.com/news/detail/68546/new-all-electric-niagara-falls-tour-ferries-powered-by-abb-enter-service
- https://www.maidofthemist.com/3830-2/
The project was heavily driven to meet the California Air Resources Board’s requirement for 30% of propulsion to be provided by zero-emission sources. In the last couple of years, ABB has been developing solutions for smaller vessel applications, bringing solutions to the market that were originally developed for heavy duty landside application such as mining and off-highway e-mobility. The first example of such solutions was for two vessels for Maid of the Mist, which were some of the first all-electric passenger vessels in the US.
Our collaboration with All American Marine has been extremely fruitful so far and we have been learning a lot ourselves, especially when it comes to the weight and space sensitivity on smaller catamaran vessels.
ABB’s hybrid-electric propulsion system will enable the ocean sampling vessel to meet the California Air Resources Board’s annual equivalence requirements for Zero-Emission Capable Hybrid Vessels. Would a Tier 4 EGR or SCR solution be as clean? Why or why not?
There is no straightforward answer to this question, as it really depends on the operational profile of the vessel and what you mean by hybrid-electric propulsion system. Both EGR and SCR are technologies designed to reduce emissions from engines, but they still rely on the combustion of fossil fuels. Although they significantly can reduce harmful pollutants, including NOx and other matters, they do not eliminate the emissions entirely. In the hybrid-electric propulsion system we are delivering for Orange County Sanitation District together with All American Marine, we are allowing the vessel to run on electricity for certain operations, especially around port and during sampling operations. This reduces the need for fuel combustion, leading to zero or near-zero emissions when operating on electricity. Depending on the source of the electricity, the system can have a far smaller carbon footprint, especially if paired with renewable energy sources. The vessel is also designed to be future proofed for new technologies; operating more on electricity by increasing the battery capacity and reducing the operations on engines.
The new ocean sampling catamaran for the Orange County Sanitation District is about 19 meters long. That said; what is the sweet spot for your technology, in terms of vessel size, tonnage and service?
ABB is uniquely positioned in the market with solutions that range from a 65 -foot aluminum catamaran to larger ferries and cruise ships. Traditionally, ABB’s solutions have been focused on large medium voltage AC or DC applications, such of ice-going vessels, mid/large size ferries and the cruise market. However, the solution we have developed for the Orange County Sanitation District vessel can range from just 200 kW up to 2 MW.
The vessel will be built to meet California Air Resources Board’s annual equivalence requirements for Zero-Emission Capable Hybrid Vessels, which mandate that at least 30 percent of total annual power must come from zero-emission power sources. That’s a high bar to clear. Are you seeing these kinds of regulations in any other markets?
I would expect that other states will look to follow California’s lead in the future. Many in the industry have their eyes on the CARB regulations to see how commercial operators will comply and what technologies will arise to help ease the transition. As technology continues to improve and adoption of low and zero emitting solutions increases, it will enable other areas to enact similar requirements to improve overall air quality.
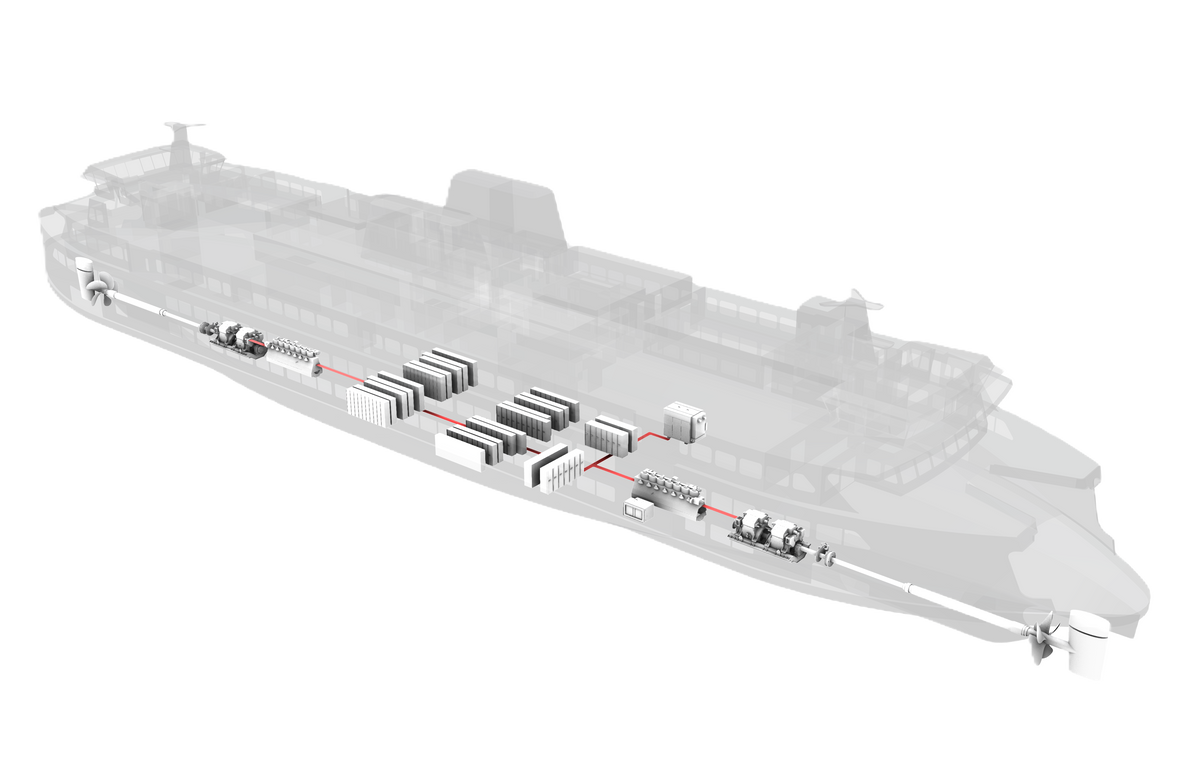
The new catchphrase for clean and green propulsion is hybrid electric. Five years ago, it was diesel electric. Is there a difference, and if so, explain how and why.
In a diesel-electric propulsion system, the vessel uses a diesel engine to generate electricity, which is then used to power motors that drive the vessel’s propellers. This means that the engines are the primary source of power for generating electricity, and the electric motors allow for more efficient operation and smoother control than a mechanical drive system. A hybrid-electric propulsion system adds a new layer of flexibility, combining both diesel engines and another energy source (batteries, fuel cells, etc.). Typically, in a hybrid-electric propulsion system, engines are the primary source of power for high power and long-range operations. Energy sources such as batteries are used for low-speed, short-range operations or when the vessel is operating around ports or for example environmentally sensitive areas.
The advent of the ‘diesel electric’ offshore service vessels (OSV) became commonplace during the offshore boom era. Those offshore systems were, by and large, too big to fit into a conventional inland pushboat. Talk about the effort to scale these technologies down for the inland, coastal, and harbor operators.
Working with All American Marine on the Orange County Sanitation District vessel has pushed us to find a solution on a vessel that is extremely weight and space-sensitive. A lot of the technology used was originally developed for heavy duty landside application such as mining. As the technology further develops, we can hopefully push even more performance from this equipment to manage high power operations workboats commonly face.
Has the progress with the battery market – smaller, lighter packages fitting more storage capabilities, for example – made it easier to fit these hybrid systems on board smaller platforms? What’s anticipated in the near future in this challenging arena?
Battery systems are per definition modular structures, built up from cells forming series strings to full energy storage systems. As such, batteries have been installed in small vessels such as river boats and sightseeing vessels already in the early days of marine electrification. The recent developments in the battery technology have however allowed for higher energy density and more compact designs. Another important aspect is the reducing cost levels for batteries in general. This helps to make hybrid and full electric propulsion commercially viable for an increasing number of vessel segments and use cases.
The ‘conventional’ propulsion option involves installing two large EPA Tier 4 main engines supplemented by an aftertreatment system – either the Exhaust Gas Recirculation (EGR) or Selective Catalyst Reduction (SCR) option. The latter choice can add additional piping, a refill and urea storage tank and demand separate maintenance all within the confines of an already cramped machinery space. Is the ABB engine hybrid electric solution conducive to a more roomier engine space – and, for that matter, freeing up space for other vessels’ needs?
In a conventional propulsion system, meeting stringent emission standards often requires to be supplemented with additional components such as EGR or SCR. ABB’s hybrid-electric propulsion system typically allows the vessel to operate with smaller engines, due to the ability to run on electric propulsion in certain conditions. This reduces the size of the engine required and may even allow for downsizing the engine room overall. Additionally, having an electric propulsion system gives you significant flexibility, as a lot of equipment can be freely positioned in unused or space elsewhere on the vessel, further freeing up space in the engine room. The ocean sampling vessel for Orange County Sanitation District is extremely weight and space sensitive, therefore being the main design driver in our solution and equipment selected.
Talk about the prospect for future towboats, inland pushboats and myriad workboats being routinely all-electric. Will that be possible, when will it happen, and what will it take to get there?
The industry is laying the groundwork for electrification, and as battery technology advances and demand for sustainable operations grows, the widespread us of all-electric workboats become increasingly feasible. We already see vessels operating in harbors or port facilities being the first adopters of all-electric systems. However, there is still work that needs to be done on the technological advancement, regulatory frameworks, infrastructure, and the economics. The next decade will likely see hybrid systems as the most common solution, with all-electric vessels becoming more routine as battery technologies improve and infrastructure for charging expands. Government regulations and incentives, such as grant funds and emission regulations, will play a critical role in accelerating the adoption of fully electric vessels.
It isn’t easy to make apples-to-apples comparisons for fuel consumption, economy, NOx, SOx and particulate matter numbers between conventional engine arrangements and a hybrid electric solution. Nevertheless, give us a general idea of what the typical workboat operator MIGHT expect.
It is indeed quite challenging to make a direct apples-to-apples comparison due to the variability in operational conditions and profile. Workboats are an attractive vessel type from a hybridization point-of-view for the following reasons:
-
Mix of high and lower demand operations
-
Short operational cycles, frequent port calls.
In a hybrid system, fuel efficiency can improve significantly, as the hybrid system allows the engine to operate at its optimal load (higher efficiency), reducing fuel consumption compared to conventional systems that often run at suboptimal levels. A hybrid system also offers lower wear and tear, as the engine is not constantly running at full load, leading to less frequent maintenance and potentially longer intervals between overhauls. In general, a hybrid solution for workboats offers benefits in terms of fuel consumption, emission reductions, and overall operational efficiency. Operators can expect significant savings over time, both in terms of fuel costs and maintenance.
Is the ABB hybrid electric solution, for the most part, OEM agnostic?
Yes, as an electric system integrator, ABB’s hybrid-electric solution is for the most part OEM agnostic. We always try to promote our own equipment where it makes sense, but in many cases, we select OEM’s based on the customer’s operational needs and preferences. Our solution is modular and flexible, which allows us to choose the best solution and equipment for different vessel types and operations, regardless of the manufacturer. In addition, we have developed strong partnerships with a wide range of partners and OEM’s (engines, energy storage solutions, power distribution, etc.), which allows us to be compatible with various types of equipment and provide customers with options based on their operational needs. Leveraging our inhouse expertise with system integration, ABB has extensive experience in the market, meaning we can work with various OEM components and ensure the solution can work seamlessly with different manufacturers’ equipment.
Give us an idea of cost differentials between the hybrid electric solution and conventional engine arrangements.
We can say that usually hybrid solutions are more expensive up front, but pay for themselves over time in that they have lower OPEX and improved efficiency
By the year 2020, ABB had already supplied over 1,300 vessels featuring diesel electric propulsion. Share, if you can, the latest numbers for ABB’s penetration into the workboat markets.
To date, ABB has electrified over 1500 vessels and digitally connected over 2000 vessels and ports worldwide.
On an ABB engineered hybrid solution, do you act as the integrator, effectively providing a single point of contact for maintenance and service issues?
Yes, as an electrical system integrator, ABB takes the responsibility of integrating all the various components of the hybrid propulsion system and warrants all equipment within our scope, therefore acting as a single point of contact when it comes to maintaining and servicing the equipment. This approach streamlines operations for vessel operators and ensures that all equipment in our system work seamlessly together.
For the typical harbor tugboat, these vessels all have what industry stakeholders have dubbed, “the hour of power.” In other words, that period of time when maximum power must be available for such heavy-duty tasks such as pushing alongside a VLCC or towing a string of barges. In a hybrid electric configuration, or a pure electric mode, will that “hour of power” ever be able to depend on the hybrid solution?
The “hour of power” can indeed be handled in hybrid electric or fully electric system; how it is achieved depends on the design and capacity of the system. Typically, with a hybrid system, this is achieved with a combination of engines and batteries; think of the battery usage as an immediate power boost. The batteries are designed to supplement the engines during this high-power scenario. In a well-designed system, the engine always operates at its optimal efficiency, even during these high-power operations. For a fully electric system, it is all about how you size your batteries to meet the power needs of your operations. A fully electric workboat typically requires large battery capacity to deliver high power for extended periods. Having good data of the current operations is vital to understand the range and operating time of the vessel. As battery technology advances, more workboat operators who previously couldn’t consider fully electric systems due to concerns about range or power output will find themselves with viable options.
Inland towboats and barges represent 85 percent of U.S. vessels and towboats are the oldest with as many as two-thirds of that type of vessel older than 25 years. The strategy of growing a fleet by acquisition of existing assets will not be viable into the foreseeable future. Or, will it? Can existing assets be retrofit for hybrid solutions?
We strongly believe growth needs to be achieved by a mix of new builds and retrofitting existing assets. Hybrid systems are modular, meaning existing towboats can benefit from the technology currently available to improve fuel efficiency, reduce emissions and comply with regulatory standards. Retrofitting existing towboats is a viable and sustainable solution, although it can present challenges. Older vessels might have limited space and structural capacity for integrating modern hybrid technologies and might require significant modifications to the hull or machinery spaces. In addition, adding electric motors, batteries, and other hybrid equipment can significantly impact the weight distribution and stability of older vessels. Careful planning and a strong partnership with stakeholders are both essential to ensure that the vessel remains seaworthy.