Pioneering Environmental Sustainability
Today’s reduced carbon footprint can’t be measured only at the stack. Below the waterline, Thordon Bearings guides marine innovation to new depths.
By Rhonda Moniz
Maritime companies face significant operational changes due to new sustainability standards and stricter environmental regulations. Answering the call, Thordon Bearings develops pollution-free marine bearing systems through advanced bearing technology. In fact, they’ve been doing it for a long time. Today, their self-lubricating polymer materials and water-based lubrication systems now lead marine and clean power generation sectors without risking environmental pollution to oceans, lakes, and rivers.
Craig Carter, VP of business Development at Thordon Bearings, perhaps puts it best when he says, "Regulations are only going to get tougher, and the elimination of oil and grease can help ship owners reduce their environmental footprint which can only be good for the environment. Seawater is free! And does not pollute."
Thordon Bearings: Redefining Marine Standards
Thordon Bearings leads the market with advanced solutions through its COMPAC shaft and rudder bearing systems. With COMPAC systems, you can use seawater instead of traditional oil or bio-lubricants. This revolutionary approach eliminates the need for oil and complex sealing systems, addressing two critical concerns. Unlike traditional oil-lubricated or bio-lubricant alternatives, COMPAC systems utilize seawater as a lubricant. This revolutionary approach eliminates the need for oil and complex sealing systems, thereby addressing two critical concerns: pollution risk and operational complexity.
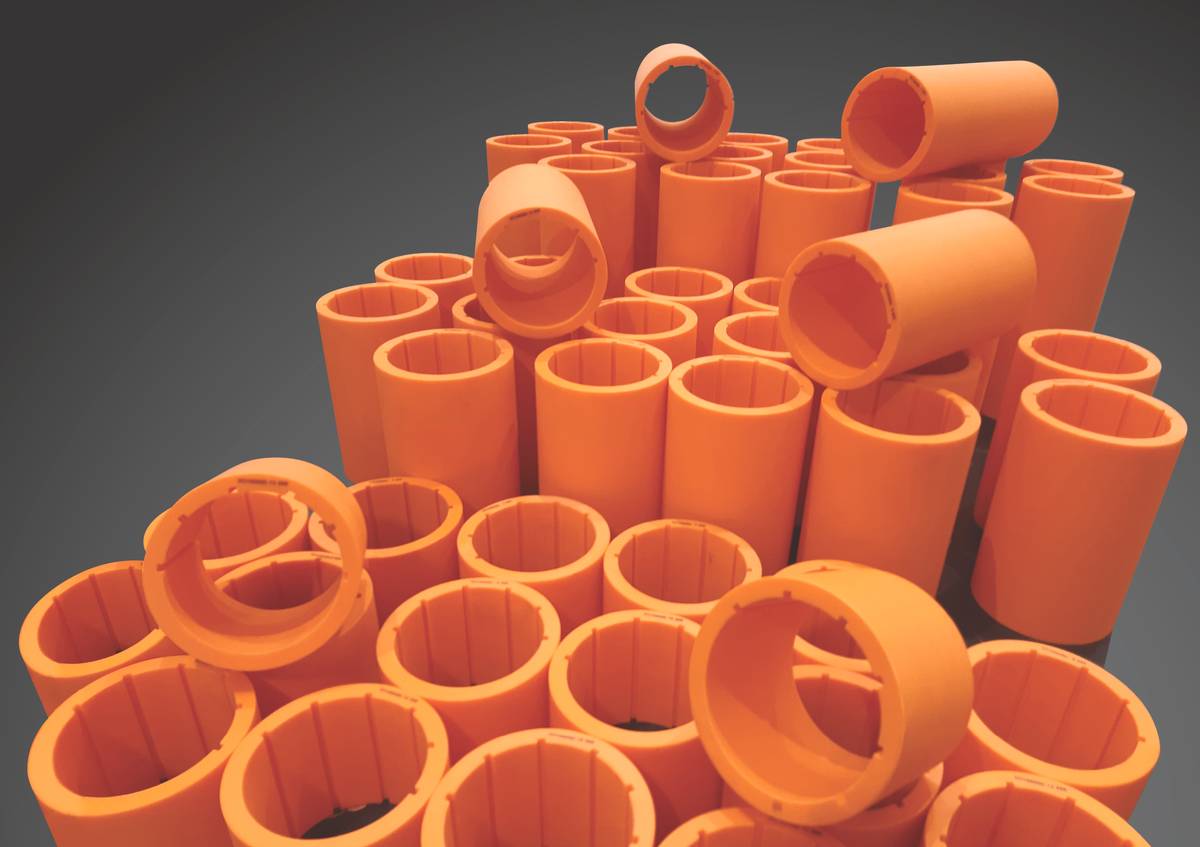
Actually, says Thordon’s Carter, “The use of seawater for propeller shaft lubrication dates back to 1843 with the original bearing in use being Lignum Vitae - a very dense oily wood. Modern materials such as polymer bearings offer long wear life with less complicated installation and operation. Seawater-lubricated propeller shaft bearings equal zero pollution and no criminal penalties or fines from illegal oil leaks.”
Thordon’s COMPAC systems reduce pollution hazards and simplify ship operations. A vessel that uses seawater for lubrication needs less maintenance and produces long-term financial benefits. COMPAC systems offer advantages beyond environmental protection. The bearings' design elements protect against wear and decrease friction. Forming a hydrodynamic film at low speeds helps the system run more efficiently, decreasing fuel use and reducing greenhouse gas emissions. This assists operators in reaching global sustainability targets.
Case Study: Liberty Lines & Thordon Bearings combine to achieve sustainability
Recently, San Sebastian-based Echetalde, Thordon’s authorized distributor in Spain, delivered 18 seawater-lubricated COMPAC propeller shaft bearings and nine grease-free SXL rudder bearings to Spain’s Astilleros Armon for installation on nine hybrid ferries scheduled for delivery over the next two years. Thordon’s technology and equipment aligns perfectly with the company's plan to lower environmental effects while meeting all performance targets.
credit: Thordon BearingsRegulations are only going to get tougher, and the elimination of oil and grease can help ship owners reduce their environmental footprint which can only be good for the environment. Seawater is free! And does not pollute. – Craig Carter, VP business Development, Thordon Bearings
The first vessels in the series, the 39.7 meter LOA 251-passenger capacity Vittorio Morace and Cristina M, were launched in June and have since completed sea trials. Delivered earlier this year, they are now the world's first IMO HSC (High-Speed Craft) hybrid fast ferries of this size.
“Liberty Lines wanted a vessel that matched their current fleet operating performance, but also capable of operating with reduced environmental impact,” explained Carter, adding quickly, “Using seawater lubricated propeller shaft and rudder bearings eliminates the risk of any oil or grease discharge to the fragile ecosystems at the various island destinations served by the company.”
In this case, COMPAC bearings stood out because of their creative design solutions. The lower half of the bearing without grooves reduces friction to improve efficiency and makes hybrid propulsion systems work better at low speeds. Despite the effort needed during system startup, oil-based systems perform better at first, but operational speed shows significantly reduced friction, which leads to better fuel use and cleaner emissions. Hence, Astilleros Armon actually made changes to their shipbuilding plans because they needed to add the COMPAC system.
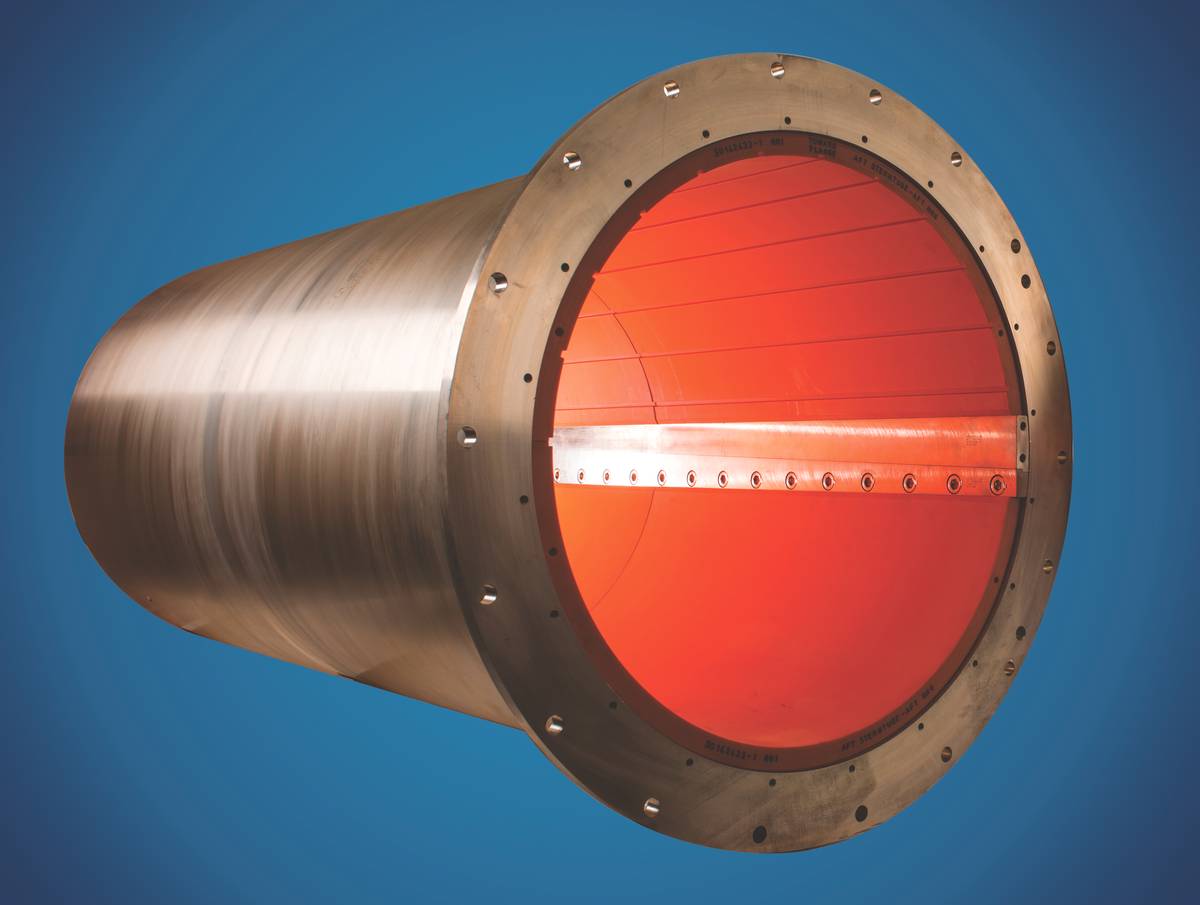
Malcolm Barratt, Thordon Bearings’ Regional Manager explains, “… the shipyard decided to slightly alter the original Incat-Crowther design to accommodate COMPAC. The original design included three competitor seawater-lubricated bearings on each shaft, but with COMPAC only two propeller shaft bearings – aft and forward – were required. The yard found this the optimum solution, not only because it fits better with the environmental ethos of the design, but it was the more cost-effective solution.”
The integration subsequently aptly demonstrated how using Thordon’s system with two bearings per shaft brings better results than traditional three-bearing setups. The change also showed the versatility of Thordon technology to fit the myriad design needs and varied ship operation profiles.
Expanding Horizons: New Markets and Applications
Thordon Bearings is widely recognized as the firm that became well known first in the large cruise vessel market, and indeed all but owned that niche because of the obvious merits of a ‘green’ solution for fleet operators acutely aware of their forward-looking, public profile and therefore yearning for a cleaner environmental signature. Today, Thordon has turned its focus also to smaller ferry boats and inland waterway workboats.
In the case of smaller, coastwise ferries – under intense pressure from local, state, municipal and indeed federal authorities to approach and achieve that elusive “zero carbon” Promised Land – they will look to any incremental solutions that bring them closer. Thordon Bearings therefore fits the bill.
Many of these vessels navigate protected waterways and ports on a daily basis. Thordon bearings stand apart because they do not release oil or grease into the environment, which creates zero pollution risks. And, with these bearings, the need to continually purchase consumables in the form of grease and lubricating oils goes away, along with the pricey cost of those items. To that end, Thordon has deployed sustainable solutions in various nations worldwide; especially Canada, Brazil, Sweden, and Italy.
Closer to home, the U.S. inland river industry – and its nearly 9,000 self-propelled domestic vessels – indeed has strong growth potential ahead. That’s because workboat owners are increasingly investing in environmentally friendly upgrades, with the Environmental Protection Agency (EPA) phasing out older, less efficient vessels. In response, the domestic workboat market increasingly accepts Thordon's RiverTough tailshaft bearings, ThorPlas-Blue rudder bearings, and TG100 tailshaft seals as standard components. These systems have become popular because they last longer, need less care, and work better than standard equipment used by pushboats and other inland craft navigating challenging environments. Hence, the acceptance of seawater-lubricated systems, once thought to be primarily a blue water solution, now extends across many different types and sizes of vessels.
Innovation: The T-BOSS System
In 2022, Thordon introduced the T-BOSS system, which advanced the bearing technology even further. Through joint efforts with the American Bureau of Shipping and the National Technical University of Athens, T-BOSS became a new system that no longer needs stern tubes in ship design. By replacing the sterntube system with a T-BOSS design, Thordon helps ships save money while operating with lower maintenance needs. Shipbuilders and operators typically select T-BOSS technology because it improves vessel performance, emits less carbon, and meets new environmental rules.
Importantly, Thordon stands out because it entirely replaces traditional lubricants. Bio-lubricants, though advertised as eco-friendly, can actually harm marine life in certain circumstances. The seawater-lubricated bearings from Thordon create no environmental pollution. The difference between Thordon's solutions and oil-based lubricants becomes crucial in protecting water bodies like Great Lakes and rivers because even minor oil spills here can ruin entire ecosystems.
Moreover, Thordon’s solutions address long-standing operational challenges. Aft seals on regular systems can be compromised when they touch fish lines, ice, or floating objects, triggering oil leaks. Thordon designs remove the weak points, using a simpler solution, and leading to more dependable and eco-friendly ship operations.
Real-Time Monitoring and Future Innovations
The company has also demonstrated its dedication to innovation by releasing BCM-W, which monitors bearing wear wirelessly and data streams bearing condition data in real-time to help operators prevent problems before they happen. BCM-W lets Thordon assist customers to run their ships faster without stopping for inspections.
The use of seawater for propeller shaft lubrication dates back to 1843 with the original bearing in use being Lignum Vitae - a very dense oily wood. Modern materials such as polymer bearings offer long wear life with less complicated installation and operation. Seawater-lubricated propeller shaft bearings equal zero pollution and no criminal penalties or fines from illegal oil leaks – Craig Carter, VP business Development, Thordon Bearings
Over time, Thordon continues to find new ways to use its technology and collaborate with other companies. Through its global partnerships, Thordon aligns with organizations prioritizing sustainable practices and operational advancement. The company that revolutionized bearings solutions for blue water, deep draft shipping, has now quietly made significant inroads into the smaller, brown water workboat and ferry markets.
Reliability, long wear life and superior customer service have made Thordon the first choice in pollution-free rudder bearing applications for over 25 years with an impressive reference list of over 4,000 vessels. That’s because Thordon, and its myriad customers alike, both understand that a cleaner environmental signature isn’t just measured by what comes out of the stack. What’s lurking just below the waterline is equally important.