Tech Talk
Inertial Sensors
Motion Compensation and Position: Role and Important Features to Check when Selecting an Inertial Sensor
Oceanography is crucial nowadays with the growing environmental challenges that the world faces, such as climate change, pollution, or ecology in general. A better understanding is a key factor to finding solutions, and oceanographers can count on fast-evolutive technologies making higher performance available to the largest professional communities. As a manufacturer of inertial navigation systems for more than 15 years in the marine industry, we will focus on what inertial navigation systems are, how they are used in the industry, and what parameters are important to acknowledge when selecting an MRU or an INS/GNSS for the motion compensation of all oceanographic instruments as well as position tracking.
Your Ally for Accurate Motion, and Navigation Measurements
An Inertial Navigation System, also called INS, is a navigation device that provides roll, pitch, heading, position, velocity, and heave. It is composed of various elements: An Inertial Measurement Unit (IMU), which is the core of the INS, a microprocessor, and a GPS/GNSS receiver. The IMU embeds 3 accelerometers, 3 gyroscopes, and depending on the heading requirement 3 magnetometers. It measures Euler angles in 3 axis thanks to their rotation along with the IMU to obtain pitch, roll, and yaw.
The microprocessor runs an enhanced onboard Extended Kalman Filter (EKF) to fuse in real-time inertial data with GNSS if position, velocity or GNSS-based heading are required. In addition, some INS also provide heave and wave measurement data for all oceanographic tasks and missions.
Oceanographers use many different instruments to measure various elements such as environmental parameters (salinity for example), sedimentology, or current. This includes Inertial Navigation Systems, which compensate the instruments or the platform’s movement.
They can be installed on different types of platforms such as buoys, vessels, surface or subsea systems ( USV, ROV, or AUVs) making size, power consumption, and enclosure determinant factors when choosing the solution, but not only. Below are some useful tips to check when choosing an inertial sensor.
1 – How to Check Robustness and Data Repeatability?
As inertial sensors are embedded in platforms which can stay at sea for months, sensor robustness is crucial. That’s why all SBG Systems’ MRU and INS benefit from an individual high-end calibration procedure using multi-axis rotary tables and temperature chambers. They are extensively calibrated in temperature from -40 to 85°C and each sensor is delivered with its calibration report. It is a major step in production as it ensures that the system will maintain an optimal constant behavior and deliver accurate data continuously in all environmental conditions, even the harshest ones.
At SBG, the specific in-house qualification process guarantees the same level of performance over lifetime with no significant drift. When calibrated, the inertial sensors go through a strict screening process, removing all sensors that don’t meet the specifications so professionals can count on consistent measurements during their missions.
2 - Heave Measurement – Choose the Sensor Depending on the Sea State
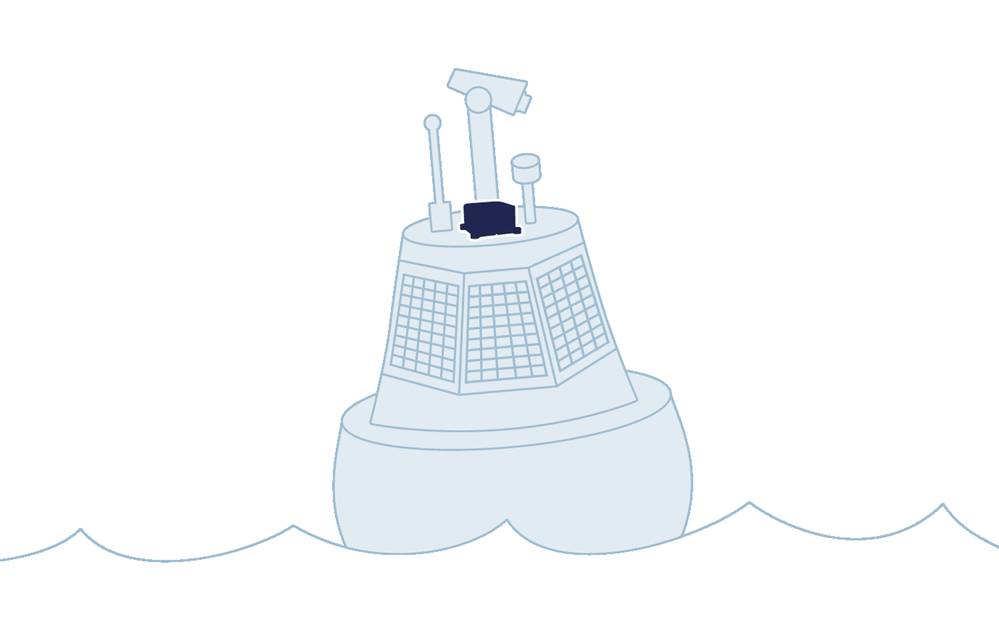
If SBG’s miniature inertial sensor called Ellipse delivers a 5-cm accurate real-time heave that automatically adjusts to the wave period, it does so on a limited wave period. To allow missions where wave frequencies are larger or more complex, higher grade SBG products come with a delayed heave feature resulting in a heave accurate to 2 cm computed in real-time, with a little delay.
3 - Multi-Constellation GNSS Receiver and Corrections
The new generation of entry-level GNSS receivers is now able to utilize GPS, Glonass, Beidou, and Galileo and so, increase satellite availability in difficult areas where the satellite coverage is limited. If metric position is not sufficient for the study, high-end systems reach 5 cm real-time position thanks to PPP corrections. This technology is constantly evolving to offer more affordable and simple solutions. RTK, providing centimeter position, is still the most accurate positioning solution when close to the coast. If data is not required in real-time, even higher precision is possible using a post-processing software.
4 - What Heading Solution When Low Dynamics or Mission Conducted Close to A Pole?
From our experience, most oceanographic applications highlight the importance of having a dual-antenna INS (i.e., that uses two antennas on the same GPS/GNSS receiver). Indeed, this kind of inertial sensor uses two GPS/GNSS antennas to provide position, velocity, and a true heading angle that is valid, even when stationary or at very low dynamics contrary to single-antenna GPS. It also delivers true heading in any situation without being impacted by magnetic disturbances or the Earth rotation, when a magnetometer and gyrocompass would be. It is a critical feature, particularly for current studies and missions in the poles. At SBG, we just launched the Ellipse-D 3rd generation , a 17-gram dual-frequency and dual-antenna GNSS/INS with high-end functionalities, making it an ideal solution for oceanography.
5- Easy Integration and Technical Support
Inertial sensors can be easily integrated into any marine project thanks to their compatibility with numerous industry software and protocols (more than 90 different messages at SBG). ROS drivers are also provided for an easy integration on autonomous platforms. We often forget that when selecting a sensor, not only should we focus on the datasheet but also on how the company is ready to help during the integration and after. Support responsiveness and pertinence are key to the project’s success. Inertial sensing and navigation is a discipline that takes into account a lot of parameters; learning some fundamentals through training could also be a game-changer in project development quickness.
We have seen how new miniature sensors like the Ellipse fit most oceanographic application. However, Inertial Navigation Systems can also serve for fully instrumented vessels integrating different grades of instruments, which require high-end INS/GNSS to compensate them. For example, SBG Systems’ Navsight Marine Solution consists in an Inertial Measurement Unit available at different grades of performance (from 0.02° to 0.007° roll/pitch) that connects to Navsight, a rugged processing unit embedding the fusion intelligence, a survey-grade GNSS receiver, a data logger, and offering multiple connections. This advanced solution is well suited for entire fleets of vessels dedicated to oceanography that need to compensate instruments such as multibeam echosounders, for instance.
For any type of application, choosing an inertial sensor is like choosing a partner for developing your project. We hope that these pieces of advice will help bring your future integrations to success.