Pro-active In-water Cleaning - Decarbonizing and Beyond
Biofouling is a problem. Even at its earliest stages (microfouling), it is a problem. It doesn't need to be barnacles and seagrasses to be an issue. Management and control of microfouling can pay significant dividends to vessel efficiency and environmental safety, and adoption of a proactive in-water cleaning plan is the biggest step that a vessel owner or operator can take in that direction.
Aiding Decarbonization Efforts
The International Maritime Organization (IMO) has set a goal of a 40% reduction in greenhouse gas emissions for the international shipping industry by 2030, with that goal increasing in the coming decades. These are laudable, necessary goals, but also extremely challenging to achieve. The shipping industry is working hard to develop new technologies to meet these goals, including alternative fuels, emissions cleaning and capture solutions, and improved hydrodynamic features for hulls, propellers and rudders. Great progress is being made on these approaches, but many of them are only applicable to newly built ships, or are extremely difficult (and expensive) to implement on existing vessels. Fortunately, there is one approach that can be adopted by all vessels, existing and new - proactive in-water cleaning.
The most straightforward way to reduce emissions is to reduce fuel consumption. Fuel consumption can be reduced through efficient operations, including ensuring the hull is as hydrodynamically efficient as possible. Once built and painted, the hull needs to be kept as clean as possible. Any growth on the hull will have a negative impact on performance. A recent report published by the IMO’s Glofouling Partnership has indicated that a very thin layer of slime (approx 0.5mm thick) covering 50% of the hull can increase emissions as much as 20-25%. That level of growth can occur rapidly in warm waters and is not easily detected. Very little of a ship’s submerged hull is visible, therefore without a diver or ROV inspection, the actual condition of the hull is unknown.
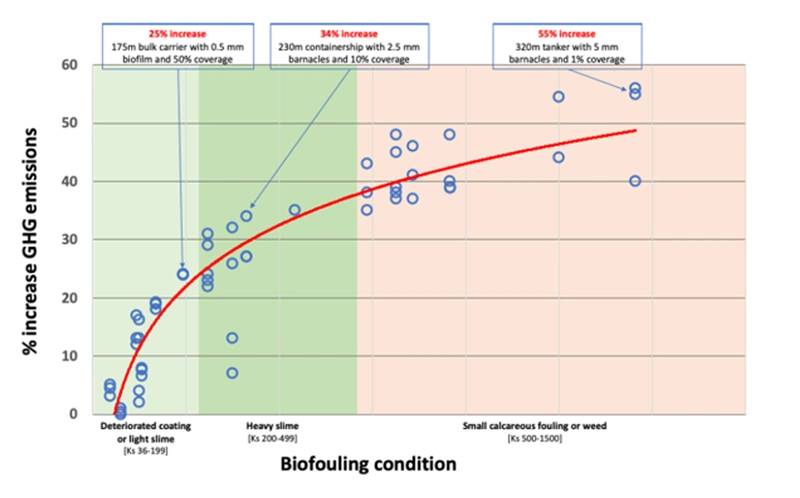
Modern coating systems work extremely well when the vessels operate within the specifications of the coating, but extended idling or pier side time will challenge the capabilities of even the best coatings. These coatings work one of two ways, either through the biocidal removal of growth, or by limiting the adhesion of growth to the hull and using the vessel’s own movement through the water to remove the now loosely attached growth. In either case, they are more effective at dealing with macrofouling; whereas microfouling is either too new to the hull to have absorbed the biocide, or is light enough to still remain attached to the fouling release coatings. When measured in weeks and months, the coatings can be effective, however when measured in months and years, the performance of all coatings degrades over time. Regardless of coating, microfouling can start impacting performance in days.
Current practices for in-water cleaning are either reactive in nature - clean once the hull condition gets “bad enough,” or scheduled at extended periodicity. These cleaning evolutions also tend to be fairly intensive events, requiring multiple days and the use of large, manually-operated equipment. Further, if removing macrofouling, the cleaning techniques can be aggressive and may risk damaging the coating system.
Proactively cleaning the hull at a much greater frequency, using gentler tools designed to remove the slime-like microfouling, can greatly improve vessel efficiency at little risk to the coating system. A proactive approach resets the vessel to a clean condition every month or so, netting a savings in fuel every day, when compared to allowing the fouling and fuel penalty to grow until the annual cleaning occurs. This fuel savings directly translates to reduced emissions and a cost savings for fuel. Further, this increased efficiency translates to other fuel sources, which may prove to be more expensive than current heavy oil and diesel fuels
Under Invasive Species Control
A second, equally significant, impact of biofouling is the potential transport of invasive species from port to port. IMO regulations have already addressed how to control the spread of invasive species through proper management of ballast water, but hull fouling has been identified as an extremely high risk factor requiring additional management practices. Australia is already implementing regulations to address the threat. The Australian Department of Agriculture, Water and the Environment has published the Australian biofouling management requirements, stipulating that incoming ships address biofouling; through proof of having a biofouling management plan, having cleaned the vessel of all biofouling within the past 30 days, or use of an Australian-approved alternative biofouling control method. While Australia is out in front with published guidance, the IMO’s Glofouling Partnerships Project is working on a global scale raising awareness and driving regulations to help protect the world maritime environment, and it would be naive to think that Australia will stand alone.
At the risk of oversimplifying things, any ship making a transoceanic voyage to Australia is going to have to prove that they have been recently cleaned, or otherwise demonstrate that they are not creating a biosecurity risk to Australian waters. A proactive cleaning approach will support compliance with these, and similar, regulations. A ship leaving a port with a clean hull and making a continuous oceanic transit to its destination will have, at most, early stage microfouling, and what microfouling that is present will be pelagic in nature rather than littoral from the previous port, and thus present minimal risk to the new environment.
Barriers to Proactive Cleaning
The benefits of proactive cleaning seem fairly straight forward, however the concept has yet to gain a commercial foothold. Why? In simple terms, until recently the only way to undertake a proactive cleaning regimen would be to use the reactive solution on a frequent, routine basis to tackle microfouling instead of waiting for macrofouling. This is suboptimal on a couple of levels.
First, the tools for reactive cleaning are designed for removing macrofouling, not microfouling. As such, these tools may not effectively remove the microfouling, and their more frequent use may be detrimental to the health of the coating system.
Second, a reactive cleaning system can take multiple days to clean an entire ship, removing the ship from its normal operating routine. Doing this once a year may be fine, but once a month will have significant impacts to both the vessel operator and port facility. In this situation the vessel would be out of operation for a greater period of time, potentially losing an entire revenue generating voyage from its annual schedule, while the port facility would be locked up with a vessel undergoing maintenance.
Finally, it's not economically attractive. The cost for the reactive solution will be the same whether it's removing slime or barnacles.
Armach’s Solution
Armach Robotics offers a dedicated proactive cleaning solution that overcomes the barriers identified above. The cleaning methodology is optimized for removal of early stage microfouling, a vessel can be completely cleaned in a single day, and through the use of autonomy and reduced onsite infrastructure and manpower, the annual cost is significantly lower than a reactive solution similarly employed would be.
Armach offers a subscription based service for a clean hull that uses a fleet of small, autonomous robots (known as Hull Service Robots (HSR)) equipped with soft brushes to proactively clean vessels during a normal inport period, with minimal disruption to other inport activities. The HSR is a hybrid flying and hull crawling robot, approximately 1 meter long and weighs less than 35kgs that can clean approx 650 sq meters (7,000 sq feet) per hour. The brushes used on the cleaning head have been extensively tested to ensure they work optimally with the coating system being cleaned, effectively removing the microfouling while not damaging or accelerating the wear rate of the coating. The HSR is equipped with a forward looking sonar and forward and rear looking cameras to document the condition of the hull, pre and post cleaning.
Armach’s ultimate differentiator is the use of autonomy and precision on-hull navigation to overcome all three barriers.
If the HSR knows exactly where it is on the hull at all times, it can be programmed to cover the entire hull efficiently and prove that it provided 100% coverage of the hull. Efficiently providing 100% coverage of the hull is critical to a successful proactive cleaning approach. If spots are missed, the microfouling can grow into macrofouling, defeating the purpose of proactive cleaning. That's pretty obvious, however the HSR needs to provide that complete coverage in as little time as possible, minimizing contact time with any specific spot on the hull. An 8-12 hour inport period simply doesn’t allow for time for the HSR to run back and forth over the same spot on the hull. Equally as important as gentle brushes are to the coating system, repeated contact with the same spot, particularly if clean of fouling, is suboptimal to the coating system.
Because the HSR is autonomous, no one is needed to actively pilot it. Where a reactive system may require as many as 4-6 people to oversee operation of a single system, multiple Armach HSRs can be monitored by a single person. Because of the small size of the HSR, no significant infrastructure is required for its launch, operation and recovery. Multiple HSRs can be operated from a single operations unit, typically a commercial van or small trailer, located on the pier near the bow and/or stern of the vessel. Running multiple HSRs on a vessel allows for it to be completely cleaned within 8 hours or so, while still allowing routine pier operations to continue, avoiding any impact to the vessel's operational schedule. These factors all combine to create a more economical solution as compared to proactive use of a traditional cleaning system.
So How Does Armach Do It?
As described above, Armach’s solution and HSR seem like an approach that could be easily undertaken by any motivated service provider. Except that the methodology described above undersells the complexity of solving the precision positioning problem. Most positioning systems and methodologies in use across robotics are concerned with where the robot is in relation to the earth, and have varying degrees of tolerance for their accuracy. For a hull cleaning application, earth-relative positioning doesn't really address the issue - what matters is where the robot is on the ship. Even tied at a pier, a ship can move slightly, and that movement could exceed the required accuracy to ensure complete coverage of the hull. The HSR is designed with a proprietary system to identify and maintain position relative to the hull (hullographic position). Armach Robotics sister company, Greensea Systems, has been developing this hull relative positioning technology for the past 4+ years in partnership with the US Navy’s Office of Naval Research.
Built on Greensea’s industry leading OPENSEA open architecture software platform for marine robotics, the hullographic positioning system utilizes a fiber optic gyroscope based Inertial Navigation System (INS), Doppler Velocity Logger (DVL), precision odometry and forward looking multi-beam sonar to establish and maintain positional accuracy within 15cm regardless of distance traveled. After launch, the HSR is flown into position near the hull, rolled 90 degrees and attached to the hull, held into position by a low pressure adhesion system (no magnets needed!). The HSR then builds a map of the hull with the sonar as it crawls along the vessel. The INS, DLV and track odometry work together, monitoring precise alignment and distance traveled to update the vehicle’s position relative to the hull. Even the best INS-based systems will inherently develop an error over time, so a novel feature based sonar navigation capability enables the system to reference its position against previously identified features on the hull to update the vehicle’s position periodically, correcting for any accumulated error. The sonar also provides for obstacle detection and avoidance. With this positioning capability, cleaning patterns can be programmed within the control software, and the HSR can be turned loose to perform its work. Video, sonar and all positional information is logged during the evolution, providing a complete report on the pre and post cleaning condition of the hull.
The value of Armach’s pre and post cleaning report can not be overstated. Foremost, it provides proof to the owner and operator that the complete hull was addressed, and that the service paid for was the service provided. Further, it provides a meaningful output that can be incorporated into existing and future performance monitoring systems, allowing for real world data regarding hull fouling to be included, enabling increased performance optimization. Owners and operators will have routine reports available that can be provided to regulatory agencies to meet invasive species/biosecurity control requirements, including providing proof of actual hull condition and entry into an active biofouling control program. Additionally, the reports can be provided to the maintenance teams to aid in drydock planning cycles.
Now. And the Future
Proactive cleaning is the future of hull maintenance, and it is available now! Join the revolution by contacting Armach at solutions@armachrobotics.com.
About the Author:
Karl Lander is the Director, Regulatory Compliance and Outreach at Armach Robotics. He joined Armach following 4+ years with Greensea Systems, where he was Director, Hull Robotics. Prior to joining Greensea, he served in the US Coast Guard for 20+ years as an Engineer and Cutterman.