Tech Feature
Valves
Re-engineered Valves Improve Performance in Demanding Navy Applications
This white paper explores three valves that were re-engineered, tested and qualified to improve performance and reliability in mission-critical Navy and Coast Guard applications.
Georges Mankarious, Product Marketing Manager, Americas, for Navy at Emerson & Colton Waldron, Business Development Manager, Industrial at Emerson
ASCO’s bilge valves with modified manual reset
Image courtesy EmersonWhen it comes to battle-tested valves for Navy and Coast Guard shipboard systems, commercial off-the-shelf valves are not designed to meet these harsh conditions. Valves in these applications are required to pass rigorous shock and vibration tests and incorporate durable, corrosion-resistant features that prolong the valves’ lifespan in saltwater environments. As military specifications evolve to meet the needs of modern fleets, ASCO provides flexible engineering expertise and strong testing capabilities to comply with the latest standards.
This white paper will explore three valves that were recently modified to meet the evolving specifications and operating requirements of the modern Navy. They include: a bilge valve with upgraded materials and solenoids designed for longer service life; a fire-hardened valve with new welded union ends to avoid external leakage during a fire; as well as a chilled water valve with improved sealing and tamper-proof capabilities.
These new and improved designs demonstrate how already-proven valve technologies must often be modified, tested and qualified for even greater reliability in demanding, mission-critical Navy applications.
Modified Bilge Valve Incorporates Higher-Grade Materials
Our first example is the ASCO® manual reset three-way flange valve, which was modified to meet the requirements of MIL-V-16556. For use with freshwater distilling units, these valves bypass the distillate and bilge whenever the salinity-indicating system signals that the distillate isn’t in compliance with the ship’s freshwater system. Available in 1- and 1.5-inch flange sizes, these units include an electrical indicating switch that closes when the valve shifts to the bypass position and opens when the valve is manually shifted, enabling distillate flow.
Modifications to this valve, which included the incorporation of higher-grade material and longer-lasting solenoid technology, were the result of the change from MIL-V-16556 Rev E to MIL-DTL16556 Rev F, which reflects the decades of shipbuilding and operating experience within the US Navy. These updates incorporate many lessons learned while operating in the naval fleet and ensure the longest lasting products are used in the naval fleet to ensure ship operations are not hindered.
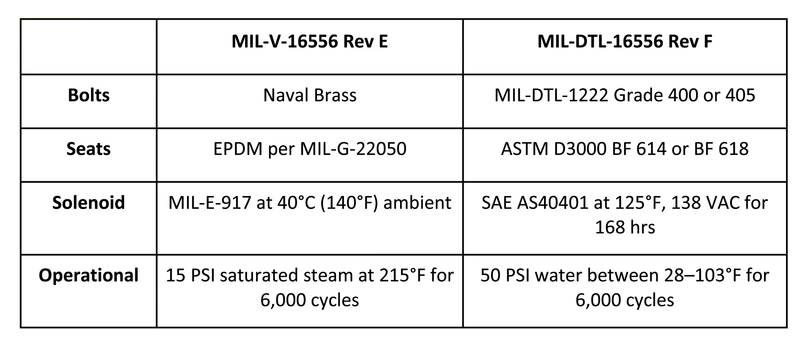
A cut-away shot of the RedHat II epoxy-encapsulated coil system.
To comply with these updated performance requirements, engineers performed several additional tests related to the valve’s flow coefficient (Cv), solenoid lifespan and media performance. For example, based on their flow tests, the engineers determined that the valve can maintain proper flow with as little as a 7-PSI pressure drop across the valve.
The engineers also tested the valve’s solenoid coil to comply with the higher lifespan requirements of SAE AS40401, the global specification for electrical axial- and rotary-stroke solenoids. They placed the coil in an oven at an ambient temperature of 125°F, energized it and then monitored the coil for 168 hours, or one week. By the end of this and subsequent tests, they found the coil was still operational and did not experience any negative effects.
But perhaps the most significant change to the bilge valve involved the new operational media requirement: 28–103°F water at 50 PSI. Engineers elected to test the 1.5-inch version of the valve, as this model includes an additional component in the form of a piston. Located on top of the stem, this piston uses the system’s water pressure to move the valve from the closed to open position. Engineers underwent several iterations of testing to ensure the valve met these new media requirements, successfully exceeding the 6,000-cycle requirement.
In addition, to meet the new MIL-DTL16556 Rev F standard, the engineers made several material modifications to the valve to increase its durability and reliability in shipboard applications. These modifications included:
- Changing the solenoid coil to an epoxy-molded insulated design, improving valve performance and extending the component’s lifecycle.
- Upgrading the switch stem to a carriage bolt for better switch engagement.
- Upgrading the pin, which holds the piston to the stem, to Monel®.
- Changing the discs from EPDM to Buna rubber, which has a higher tear strength.
- Integrating a higher retaining wall and larger retaining cap to better hold the discs in place.
- Altering the stem retaining nut and increasing thread size for longer life.
ASCO’s fire-hardened valve.
Fire-Hardened Valve Eliminates Sil-Brazed Union Ends
In this second example, engineers modified a two-way solenoid valve to safely survive a fire without leaking additional oxygen into the air. The original valve design, which is direct-acting and normally open, integrates soft seating to provide tight shutoff, as well as a brass body and valve seat. It also meets the high-shock requirements of MIL-S-901, the military specification for high-impact mechanical shock for shipboard equipment. Primarily used on Navy air compressors, these valves also meet the requirements for chilled water systems, as specified by MIL-F-1103.
To meet the updated military specifications for fire-hardened valves, the two-way solenoid valve could not include sil-brazed union ends, as the brazed joint could melt during a fire and leak compressed air into the room. As a result, engineers modified the unit to include stainless steel material and welded copper-nickel (CuNI) union ends.
ASCO’s upgraded chilled water valve with manual operator.
Durable Chilled Water Valve Features Innovative, Tamper-Proof Design
In our third example, engineers upgraded a chilled water valve used in shipboard cooling systems. These new units now serve as simple drop-in replacements for legacy models. They also feature a new tamper-proof design and improvements to the electrical enclosure and solenoid coil system.
Legacy units comply with MIL-R-16743, which covers mechanical Naval shipboard refrigerating systems using a reciprocating compressor and dichlorodifluoromethane refrigerant. The original design of these internal, pilot-operated valves included sil-brazed union ends or flanged ends, forged brass or bronze bodies and a manual operator. Valves also met the high-shock requirements of MIL-S-901. But despite the valves’ quality performance in Naval applications, certain design features required an upgrade to address key concerns related to unwanted tampering, electrical sealing and corrosion resistance.
The latest chilled water valve now integrates RedHat II coil technology, which prevents condensation and corrosion in the housing. It also features all-stainless steel hardware, a tool-based manual operator and provisions for internal and external grounding for greater safety in the field.
-
Improved electrical enclosure seals sensitive electronics. The RedHat II epoxy-encapsulated coil system protects the valves’ magnetic conductors from being shorted by exposure to seawater ingress, which would prevent the valve from operating. As part of this upgraded design, units also include an enhanced aluminum junction box that prolongs valve longevity in humid marine environments. They also feature four captive screws and retaining gaskets that take up a smaller area on the valve, lowering the risk of condensation and corrosion in the housing. In addition, the valves feature screw terminal connections and cable glands that meet MIL-S-19622, which outlines nylon stuffing tubes for shipboard electrical cables, as well as name plates that meet MIL-DTL-15024.
-
Tool-assisted manual override prevents unwanted tampering. The upgraded valves also feature a tamper-proof design, which overcomes a challenge faced by legacy units. The legacy valves include a manual operator that sailors could operate by hand, overriding the room thermostat and impacting the efficiency of the cooling system.
To prevent tampering, the upgraded valves now include a tool-based manual operator. This new construction features a #6 spanner head screw head that requires the use of a special wrench to manually operate the valve, reducing unauthorized operation in critical applications.
In addition, corrosion-resistant hardware — including all stainless steel screws and bonnets — further improves the valve’s corrosion resistance.
-
Fully tested to military shock, vibration and submergence requirementsEngineers have ensured the latest version of the chilled water valves still meets, and in some cases, exceeds, the military’s requirements for vibration, shock and submergence:
-
MIL-STD-167 vibration test. The upgraded valves are vibration-tested to 4–50 Hz (double amplitude) with all three axes energized and de-energized, exceeding the standard military specification of 4–33 Hz (single amplitude).
-
MIL-S-901D shock test. Units also meet MIL-S-901D, which covers high-shock testing requirements for shipboard equipment, verifying their ability to withstand weapons-related shock loadings. The upgraded valves are tested to all 18 blows at 1, 3 and 5 feet with all three axes energized and de-energized, meeting Grade A, Class I, Type A shock requirements.
-
MIL-STD-108 submergence test. Thanks to the enhanced RedHat II solenoid technology, the upgraded valves exceed the MIL-STD-108 submergence requirement of 15 feet for 24 hours.
-
To learn more about Emerson battle-tested valve technologies for modern Naval applications, please visit our product page.