Tech Files
Robotics & UXO
To Boldly Go … on the Hunt for UXO
Detection and remediation of unexploded ordnance (UXO) certainly fits the bill when talk turns to removing the diver from dirty, difficult and dangerous situations. Here’s a look at a few systems that are making waves.
Greensea Systems reportedly successfully demonstrated its capabilities on a mission to locate buried munitions in the surf zone. This UXO survey demonstrated the value of OPENSEA to rapidly integrate and deploy a new sensor suite for the task while showcasing the capabilities of the Bayonet 250 AUGV, which was selected as a finalist in The Defense Innovation Unit's (DIU) Autonomous Amphibious Response Vehicle (A2RV) program's rapid prototyping phase. Out of 67 proposals, the Bayonet 250 crawler prototype, developed in partnership with Greensea, was chosen for its performance and potential to detect, identify, and neutralize naval mines and other explosive hazards in the surf and beach landing zones.
Operating over eight days and covering 18 square kilometers in depths of up to 10 ft., amidst wave heights of 4-6 feet in the challenging surf zone, the Bayonet 250 provided a stable and reliable platform for conducting the survey that included a towed sled equipped with White River Technology's (WRT) marine APEX technology, integrated into Greensea’s software platform, OPENSEA.
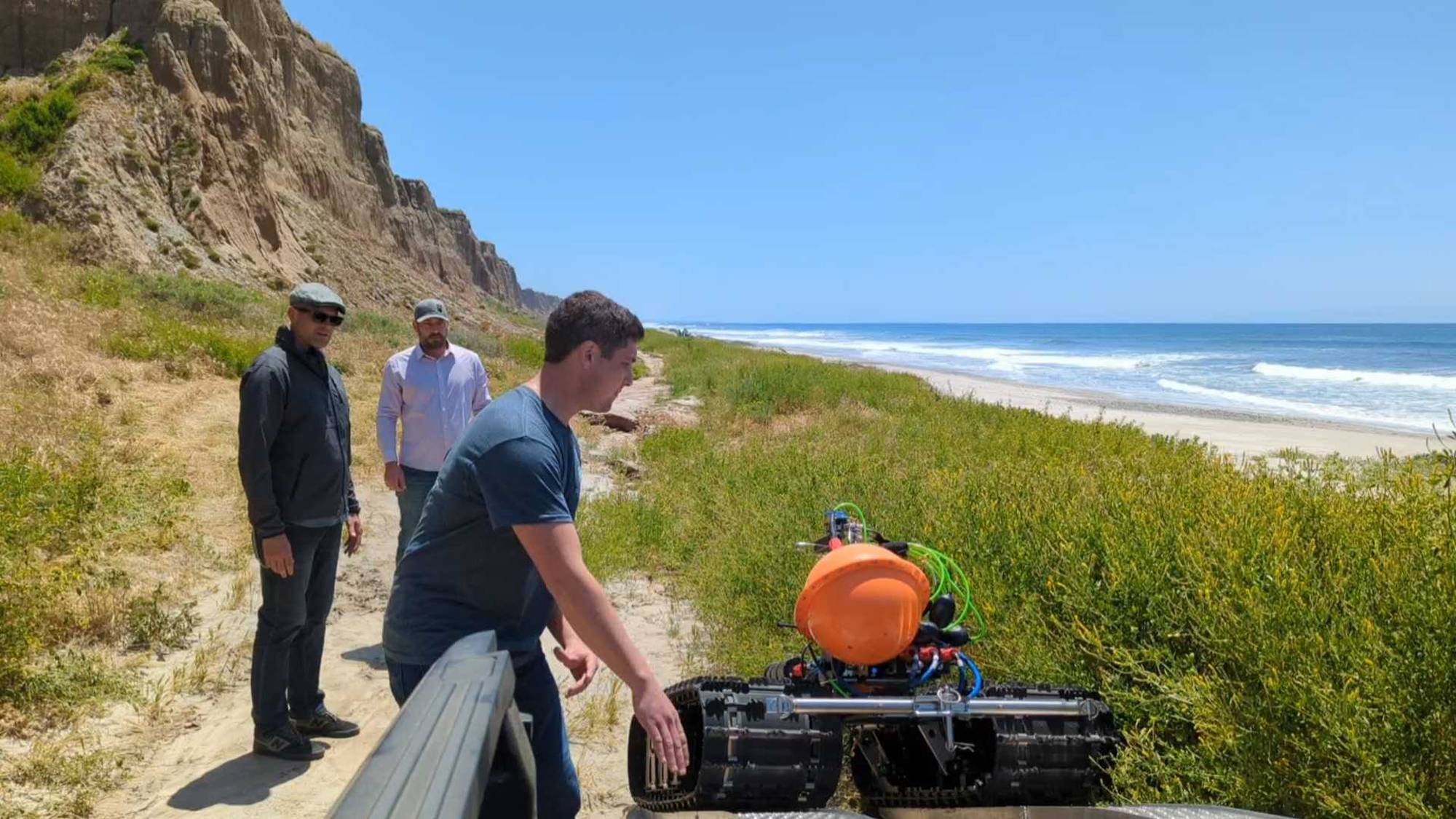
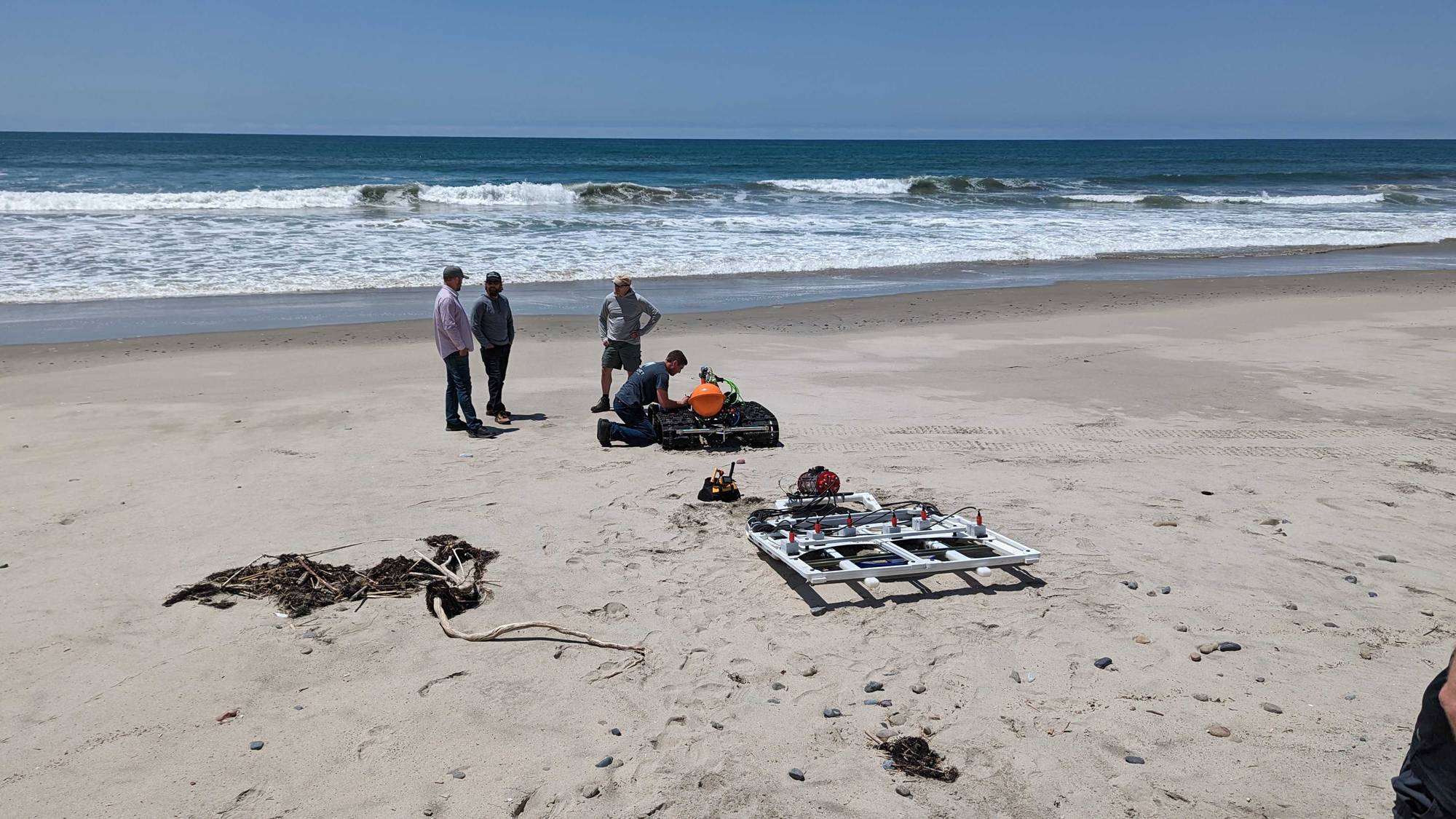
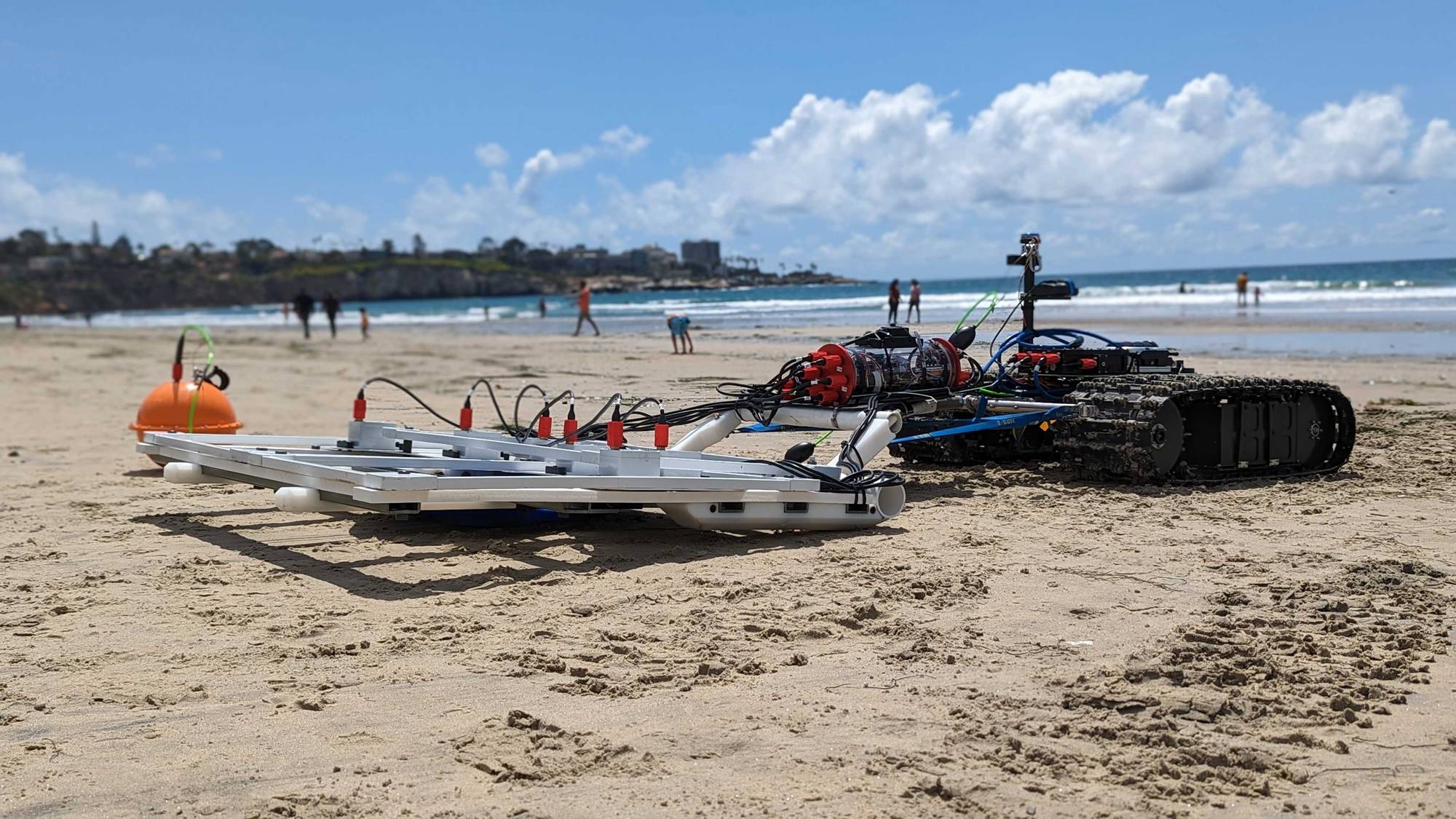
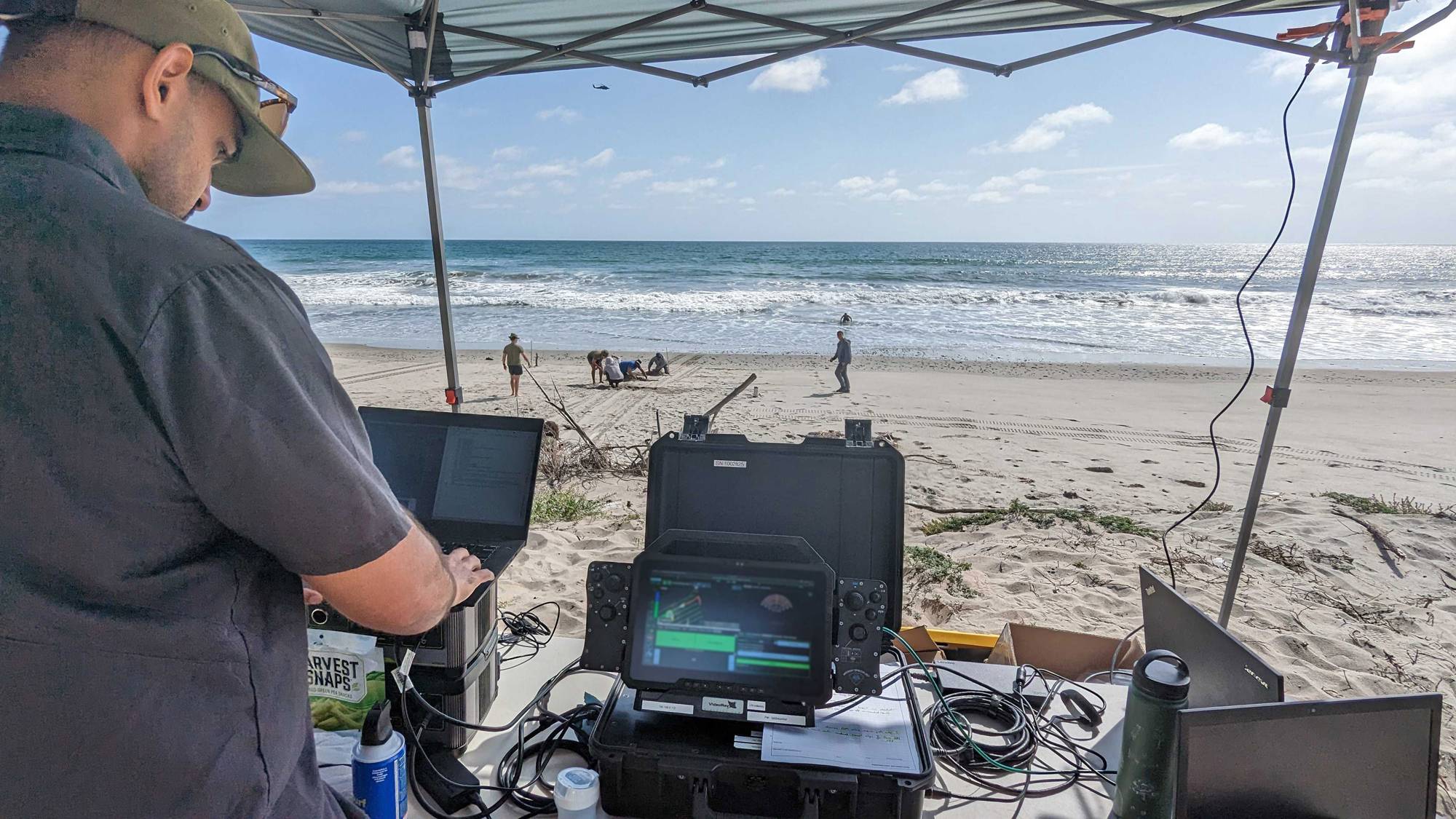
"We are very excited about the recent success of crawler-based 3DEM sensing for advanced geophysical classification of munitions in the most challenging environments like surf zones”, said Greg Schultz, CTO for WRT. “The combination of autonomous amphibious crawlers, like the Bayonet units, and the WRT APEX dynamic electromagnetic classification arrays, appear ready to go where divers and towed systems have not been able to in the past".
The rapid integration of the sensor sled facilitated the detection and classification of objects, with a buried depth of up to three meters based on material composition.
“By quickly integrating a new sensor for buried UXO and munitions, mobilizing an operations team, and collecting data in demanding conditions, we have demonstrated our capability to locate and address explosive hazards in one of the most dynamic and challenging operational environments,” said David Pearson, Program Manager at Greensea.
Throughout the mission, the Bayonet 250 successfully identified buried targets based on burial depth and signal signature, highlighting its ability to detect and identify explosive hazards in both the surf and on beach landing zones.
DFKI AI Helps to Recover Munitions
By some estimates, more than one million tons of munitions dumped in the North and Baltic Seas during and after the two world wars still today poses a threat to humans and the environment. Technologies designed to enable robots to identify and mitigate UXO are being developed by the Robotics Innovation Center of the German Research Center for Artificial Intelligence (DFKI) headed by Prof. Dr. Frank Kirchner in the current CleanSeas project.
The German Federal Ministry of Education and Research (BMBF) is funding the CleanSeas project with around one million euros from January 1, 2023, to December 31, 2025. The project aims to create the technological basis which enables robots to autonomously detect and handle critical infrastructures underwater. To that end DFKI’s Robotics Innovation Center is developing AI solutions for the following three areas:
-
Precise navigation in the close range of critical objects,
-
3D reconstruction of objects using various sensors, and
-
Whole-body control for (partially) autonomous object manipulation.
The autonomous underwater vehicle (AUV) Cuttlefish, developed at DFKI, serves as the robotic test platform. The AUV has two deep-sea capable gripping systems for flexible handling of objects underwater. Thanks to its design and AI-based control, it can change its center of gravity and buoyancy during a dive and assume any orientation. Comprehensive environment perception thanks to sensor fusion and generative AI In the case of recovering munitions from oceans, the AUV must be able to approach its target object without colliding with it. For this purpose, the vehicle is equipped with a variety of sensors such as sonars, cameras, laser scanners and magnetometers.
However, due to the highly variable environmental conditions underwater, the robot can only partially sense its surroundings at a low resolution, impeding navigation and object detection. So the scientists combine acoustic and optical sensor data using probability-based sensor fusion. Thus, the quality of the high-resolution camera data especially depends on the prevailing light and visibility conditions. Acoustic sensors, however, are independent of visibility conditions, but only provide data with significantly lower resolution. In addition to that, their functionality is limited at close range. To close the gaps in object detection, the researchers are also relying on the use of generative AI algorithms. This involves training a neural network so that it can generate camera-like images based on low-resolution sonar data. That way, a comprehensive reconstruction of the target object in 3D is possible.
To enable precise arm movements, the entire vehicle, including the arms, must be included in the control. Therefore, the scientists are resorting to modern approaches of whole-body control, which they combine with learned behavior. A deep neural network-based algorithm learns how the vehicle behaves under different conditions. Thanks to the learned hydrodynamic model, the AUV can precisely readjust its pose automatically at runtime. To avoid arm collisions, the researchers are also developing software that coordinates arm movements in real time. Tactile force sensors on the robotic grippers allow sensitive and, in case of doubt, compliant handling of ammunition residues.
The aim of the manipulation is to attach lifting gear to the casings of old ordnance in order to lift and transport it.
The technologies developed will initially be tested under controllable laboratory conditions. For this, the researchers have access to the DFKI's Maritime Exploration Hall in Bremen, where they will sink old ammunition in the 8-mdeep saltwater basin, which contains 3.4 million liters of saltwater, and place it in sandboxes installed inside.
Seamor UXO Detection System Trialed
Seamor Marine’s Chinook ROV is making waves in the field of undetonated explosive ordnance (UXO) detection after a successful compact magnetometer integration with subsea engineers at Ocean Floor Geophysics.
Magnetometers are typically bulky, towed by a manned marine vessel or larger autonomous underwater vehicles (AUV), and scan the seafloor through a lengthy process.
The compact maneuverability offered by remotely operated vehicles holds promise to subsea engineers designing magnetometer scanning systems. However, technicians have been challenged by the electro-magnetic interference created by the electrical systems of these smaller units; that is, until recently.
Earlier this year, Seamor Marine was contracted at the request of a private client through Ocean Floor Geophysics for a third-party integration of their magnetometer with the Chinook ROV. “Seamor’s Chinook is compact, maneuverable, and reliable,” said Nathan Ehrenholz, subsea robotics engineer at Ocean Floor Geophysics.
“ROVs are complicated devices with many electronic and mechanical components,” said Robin Li, President at Seamor Marine. “However, the design of the Chinook meant very little baseline interference which helped our magnetometer integration to go smoothly.”
Most ROV pilots make use of the built-in, movable camera during inspections and scans, but that was not an option for this trial. “The solution was to fix the camera in place, using the Chinook’s quiet thrusters to reposition the magnetometer while mapping rather than the pan/tilt feature of the built-in camera,” said Li. “The submerged explosives might induce a flux of 5-20 nanoteslas, while the tilt mechanism might induce a flux of up to 500 nanoteslas which is far too much interference to get accurate readings. I’m glad to say that, when put to the test, the magnetometer trial integration for the Chinook was a success.”