Emerging Leaders
Max Braddock, Ship Superintendent, Detyens Shipyards
Emerging Leaders: Max Braddock, Ship Superintendent, Detyens Shipyards
Running ship repair projects is part engineering, part art and all tenacity. Max Braddock, Ship Superintendent, Detyens Shipyards brings all of this and more to the table. A 2019 graduate from the United States Merchant Marine Academy, this Kings Pointer combines not only his education but his role as an outside linebacker on the USMMA football team to help deliver signature Detyens Shipyard service to commercial and government clients, domestic and foreign. We recently had the chance to visit with Braddock for an in-depth discussion on his most challenging ship repair and conversion jobs to date.
By Greg Trauthwein
Max, to start us off, can you give a personal and professional background with insights on why you became interested in the maritime industry to start?
I am at Kings Pointer, class of 2019, a transportation and logistics management major, and I've been [at Detyens Shipyards] ever since. I got married two years ago and I have an 18-month-old baby girl, Brooklyn, with my wife, Jessica, who is an estimator here at Detyens.
I've been a ship superintendent for about five years, working with my project manager, Hugh Chambrovich, also at Kings Pointer. We've co-managed more than 30 ships together, including one I have leaving today, the USS Pathfinder.
Did you always know that yours would be a career in Maritime?
No. In my senior year of high school I had a recruiter come out and look at me for football. He said he's from the United States Merchant Marine Academy, and [at the time I thought] "I don't know what that is, please tell me more about it." At first it didn’t sound interesting to me, so I brought [the information] home and threw it in the trash. My mom picked it out of the trash and said "Max, this could be a really good opportunity. I think that we should pursue it." So I filled out the application and I'm here today.
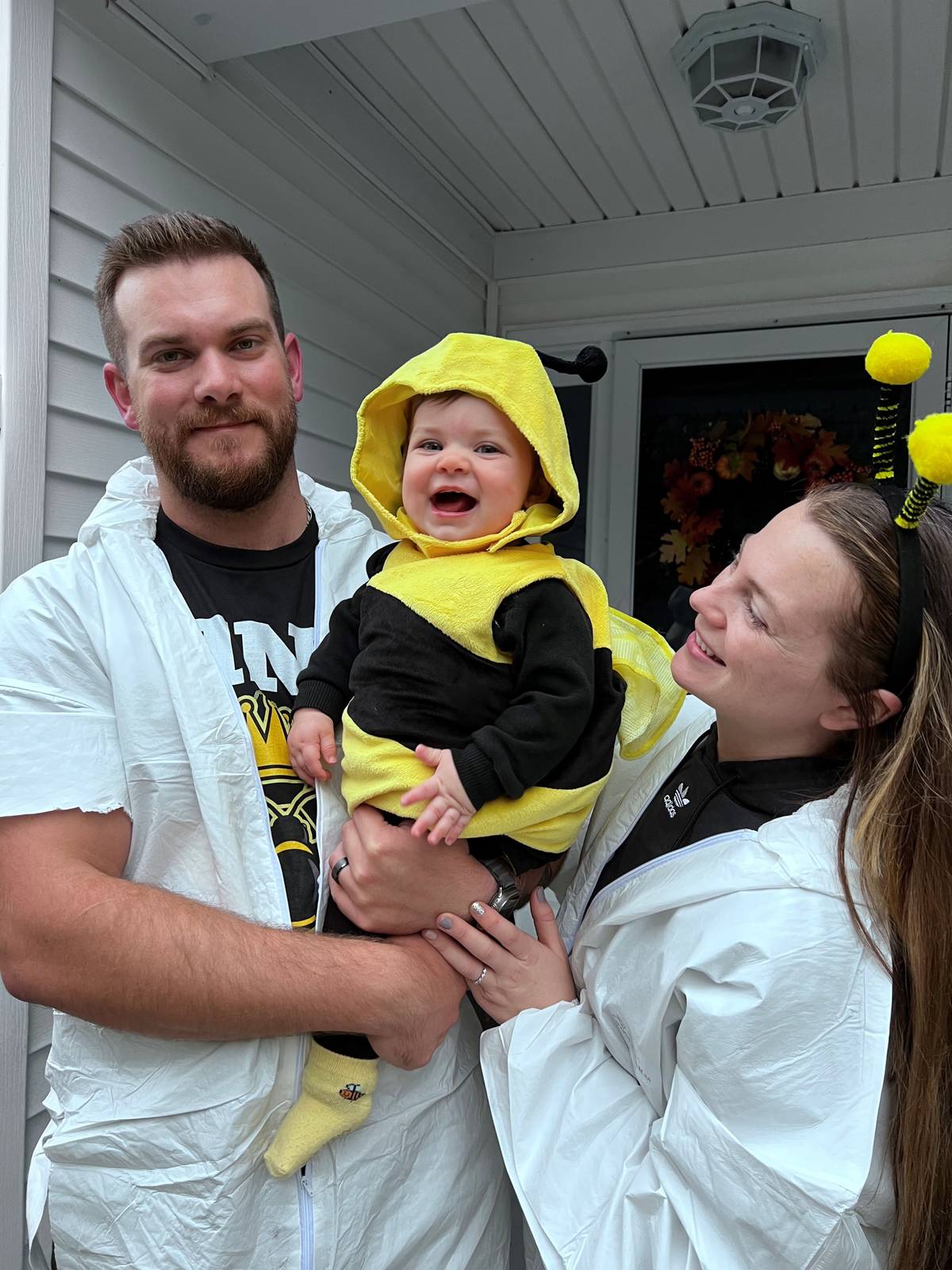
As superintendent, what specifically are your responsibilities at the shipyard?
I manage the day-to-day operations, I'm the ground guy, I'm on the ship with seven or eight of the shops that report to me.
Looking first at Detyens Shipyards’ commercial side, I understand you recently worked on a McDermott cable layer. Can you give the breadth and scope of this job?
The North Ocean 102 contracted by McDermott came in a couple of months ago looking for an aggressive, 30-day dry docking package. It was five main propulsion units that needed to be swapped, so it involved two main thrusters and two tunnel thrusters, as well as one drop-down thruster, as well as a 100% blast of the underwater hull freeboard. [With the work package and aggressive timeline] it was a big coordination effort between paint and the Kongsberg [thruster] reps [to line-up the work]. It was tough, especially in that aggressive 30-day window. But they left a couple weeks ago, and spoke nothing but good words about our professionalism and the quality of work.
As this is the ‘navy’ edition, can you discuss the military/government side of your work? Specifically, I understand that you were involved in a recent foreign military sales job, the conversion of FFG USS Robert Bradley for the Bahrain Navy.
It was a year and 10 month availability … I think originally it was supposed to be nine months. As soon as it got here, we could tell that it was going to take more than nine months.
The crew from the Royal Bahrain Navy (RBN) came over, about 90 RBN personnel here at the shipyard, so we set up a barracks right across the yard for them. [Right from the start] we had a great working relationship with them, and they were with us every step of the way to learn.
The scope of the project was basically head to toe. That ship was laid-up in Philadelphia for nearly 12 years, and it wasn't laid-up in correctly. They had water in the piping, they had fuel and piping, and being in Philly there was freeze damage to every system. From the chill water systems to the salt water systems to the fuel systems, everything was [pretty much] cracked and in disarray.
It was a mess, but it was a great learning experience; great to be part of that foreign military sales, great to work with the Kingdom of Bahrain, they were awesome to work with.
[One challenge was the installation of the FM-200 firefighting system to replace a Halon system]. Basically, we had a subcontractor show up and say, "All right, here's the equipment. Go ahead and install it," with no drawings, no expertise … nothing. Basically, myself, the other project manager and VSE's industrial manager and the government port engineer came up with our own FM-200 system that would provide fixed firefighting system to all auxiliary spaces and the main engine room.
We had a 100% blast of freeboard, underwater hull. We had main propulsion work with the MRG, shaft work, the superstructure was completely blasted and painted, the flight deck was completely blasted and painted. We installed a 76-mm gun with the Coast Guard supervision, which was pretty cool.
The best was the experience with the Bahrain crew; we became pretty close, as you would imagine for a year and 10-month project. On their ceremony day, and when they left the next day, there were tears in everybody's eyes; we were practically like family at that point. [They basically] bought a junk [ship] and ended up sailing away with a new one.
That sounds like an incredible experience. It sounds like your job is planning, but also thinking on your feet and changing based on the condition of the ship.
Correct. You can plan as much as you want, but sometimes as soon as you step on the ship, that plan is right out the window. We definitely had a lot of challenges, but we overcame them and they got their [new ship] in the end.
I know there are still a lot of really old ships around, particularly in NOAA. I understand you've had a couple recent experiences with some NOAA work, particularly with the Pisces and Oregon Two?
The Oregon Two came in a couple of days after the RBN ship left, and Pisces came in about four hours after Bahrain left. So, I went from a year and 10-month job straight to NOAA. Both ships went in the Dry Dock One, where the Oregon had a complete a 100% blast on the freeboard and underwater hull. The Pisces had a 100% blast on the freeboard and spot on the underwater hull.
The Pisces was interesting because they have a centerboard – pretty much a 30-foot paddle – with a bunch of sensors and equipment on the end of it. It retracts into the ship while they're underway, [and when deployed] it sticks about 10 to 15 feet down into the water. We had to pull that centerboard out through the O3 level, through the bridge. They actually had a soft patch on the bridge, and then on the flying bridge we had to pull both of those out with our large crane. We had to pull it all the way out, blast and paint it, do some work on the transducers and sensors on there, and then reinstall that thing. That was a job in and of itself.
They both had main engine room work. They had diesel overhauls on the Pisces. And on the Oregon, they had MRG work. That engine room was packed, and you could tell that the ship was built around that engine room. So, in order to pull the generators out, we had to basically cut the entire upper level of the engine room out and rig those things out to fit them, which was a job.
NOAA has a great crew of port engineers, and they were here for about two months each, so I worked them simultaneously.
One last question. When you look at the shipyard around you today, are there anything you'd like to highlight? Anything that recently or will soon be brought online?
So, we just upgraded our power on Delta Pier. For as long as I've been here that pier's been an issue or it's had an issue with power, so we just upgraded our Phoenixes on that pier. Our wharfs are in great shape; fendering system's great. We've been putting a lot of maintenance and repair into our yard to make our facilities great. [For us here at Detyens Shipyards thought it’s all about] safety, safety, safety. We harp on safety; we get regular weekly toolbox talks. While production is everything, safety comes first. We need these guys here the next day, so we need them to work safely today, going home to their families. As a shift superintendent, you have to push to get stuff done now, but you if needed you have to take a step back and say, "Hey, that's not safe. Let's do it in a more safe manner."
Watch the full interview with Max Braddock, Ship Superintendent, Detyens Shipyards on Maritime Reporter TV: