Gas Turbine Air Intake Filtration System
By Pete McGuigan, Global LNG Market Manager, Filtration & Energy Solutions Division, Parker Filtration Group
Parker Neptune high velocity intake system.
Image courtesy Parker FiltrationRegional conflicts and growing international security concerns more generally are prompting the world’s navies to expand their operational fleets. Gas Turbine (GT) propelled surface vessels and marine warships are at the heart of many of these taskforces, helping deliver an advanced capability to manoeuvre and to quickly engage and pursue targets at sea.
Modern naval vessels are moved through the water using powertrain combinations of either reciprocating engines, electric motors and/or gas turbines to provide the propellor rotating forces necessary. In many instances when GTs on employed, they are engaged only when additional speed is required, perhaps in pursuit of criminal gangs or during evasive manoeuvres, or when the vessel is close to shore and combustion exhaust emissions are more stringent. A reliable propulsion system, however, is always critical to the vessels’ function and the primary power sources employed simply cannot be allowed to fail to operate when called upon. It is difficult to envisage any single characteristic more important to a naval marine surface vessel engaged in combat operations than the reliability and availability of its propulsion system. Image 1 below shows some common powertrain configurations available for propeller driven naval surface vessels.
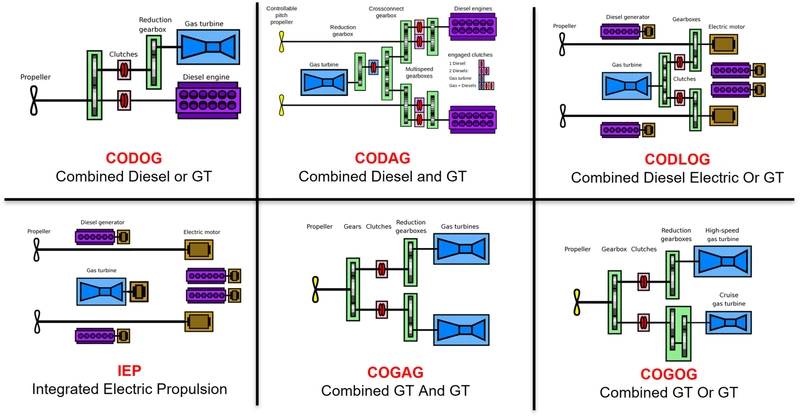
Gas Turbines ingest enormous amounts of ambient air as part of their combustion process, air that left untreated will contain all manner of airborne contaminants, all of which will do serious damage, erosion, corrosion and fouling of the highly optimised GT internals. Harsh weather conditions, high levels of small airborne particulate in the form of sand, dust, airborne hydrocarbons and salt aerosols, added to the concentration seasonality of these contaminants are just some of the challenges faced by a gas turbine air intake filtration system operating at sea. The offshore environment is brutal for any piece of equipment, let alone one that needs to continuously run in the face of harsh storms, sea spray, mist, fog and almost every other type of water challenge. Naval marine vessels can also be located anywhere in the world, near or far from the shoreline. These systems therefore need to be designed to be able to remove sand and particulate blown seawards from the land as well as the corrosive salts churned up from the ocean.
Salt: The Turbine Killer
Salt is particularly perilous to the GTs on naval vessels because there is so much of it stirred up from the sea and continuously present in the ambient air. While the filter system housing and internals will typically be manufactured from 304 or 316 grade stainless steel, sodium from sea salt (NaCl), if allowed to get downstream of the filtration system, will still combine with sulphur in the fuel to create sodium sulphate (Na2SO4). This chemical reacts with the base metal of the turbine blades in the high temperatures of the hot gas path causing rapid corrosion and component failures. This very common effect is known as hot corrosion or sulphidation. Chlorine in the salt also very commonly acts as a pitting corrosion initiator in colder parts of the turbine, potentially leading to catastrophic damage.
Salt can be difficult to handle because of its hygroscopic nature, meaning it has an affinity for water. It absorbs moisture readily and can move easily from solid to liquid form with changes in ambient relative humidity. A filtration system therefore needs to efficiently defend the turbine from both liquid and solid phase contaminants. When salt is wet, it easily sticks to turbine blades and attracts other contaminants, quickly affecting the aerodynamic performance of the turbine. Unlike contaminants that cause fouling, one of the major problems with salt, however, is that the corrosion it causes is often not perceived in monitored turbine performance data until something physically breaks. Naval vessels by their very nature will always be exposed to a great deal of salt laden sea spray. To handle this salt effectively, a filtration solution needs to allow for input concentration, aerosol size distribution and aerosol physical state, whether droplet or particle. The right solution must also consider the impacts of increased pressure drop introduced by adding multiple filtration stages with salt protection.
Salt can also contribute to erosion and crucially for salt compounds, are a substantial factor in the corrosion of turbine internals such as compressor blades, combustors, bearings or even elements of the turbine section. Corrosion and wear will inevitably reduce the service life and increase the requirements for maintenance. Again, while this is costly, for military endeavours a more significant concern is that servicing and repairs have direct implications for service readiness - any downtime is a major issue in terms of naval responsiveness and repairing or replacing worn components can be a lengthy procedure, especially if the vessel is at sea.
The same considerations apply to less severe contamination too. A typical response to compressor stage contamination is an offline wash cycle which will restore most if not all the lost performance. However, it also necessitates shutting down the turbine with an inevitable, if short-term, loss of availability.
The marine environment in general then is particularly unforgiving when considering precision equipment like an advanced gas turbine and with bad weather, rain, fog and sea spray on top, these issues are only exacerbated. Thus, a critical consideration for naval turbine reliability is to prevent corrosive materials like salts and other airborne contaminants from entering the machine. This places huge emphasis on effective air filtration.
In Search of Space
With gas turbines widely deployed in both terrestrial and marine applications with PARKER designed combustion air intake systems, such as electrical power generation on land or mechanical drive on offshore Oil and Gas production installations, air intake filtration, its nuances and particular challenges are well understood. However, on board military vessels, there are additional issues that must be addressed when designing effective air intake filtration systems. In particular, the significant limitations on available physical space. The demands and extreme limits for real estate on military vessels tends to relegate intake filtration systems down the priority list and can see considerations such as accommodating turbine ancillaries developed almost as an afterthought. Consequently, while the air intake filtration system must be effective in terms of ensuring turbine reliability and performance, it must normally achieve this goal whilst remaining extremely compact, up to 4 time more compact than for a comparable land-based application.
Having then developed such a system, many of the world’s navies will commonly deploy multiple iterations of the same design across the fleet. A particular configuration will be specified for the gas turbine propulsion system for relevant vessel types, such as a class of frigate or destroyer, which will then be repeated across all vessels of the same type. Thus, while the vessels may see some updates between hulls, such as accommodation or radar systems and weapons platforms, the design of the turbine and its combustion air intake system may not change throughout the design life of the ship class and there will be multiple deployments across a fleet. In many cases, Parker Hannifin has delivered more than 20 air intake systems for a particular naval class of vessel. This approach places an absolute premium on the proven long-term performance of the unit and all its related systems. Parker began its GT air intake filtration and system design business within the marine application space, developing compact, high velocity systems in the 1960s and 1970s that subsequently evolved into today’s market leading Altair-Neptune and Altair-Vega systems. To date Parker have supplied over 750 individual marine vessels with GT intake protection.
Compact, High-Velocity Filtration
Given the severe restrictions on space on board marine vessels, as already noted a key characteristic is the requirement for a compact, aerodynamically highly optimised, combustion air intake system. This necessitates high air stream velocities through the system whilst still meeting the very stringent airflow distortion limits at the GT face as specified by the GT OEM - an uneven velocity airflow creates more turbulence, is inefficient and leads to increased pressure drop across the system, all of which adversely affects GT performance. While applications such as FPSOs or FLNG vessels offshore already require compact high-velocity filtration systems, for naval propulsion this requirement is only enhanced. Given the intake filters are required to run at extremely high speeds this design obligation can potentially increase the opportunity for materials such as salt water to be carried through into the turbine internals. This danger becomes even more likely in rough seas or when travelling at high speed during pursuit or in combat.
In naval applications operating at extremely high airflow velocities the air intake filtration system to prevent salt water and particulate ingress is most commonly provided by 3 stages.
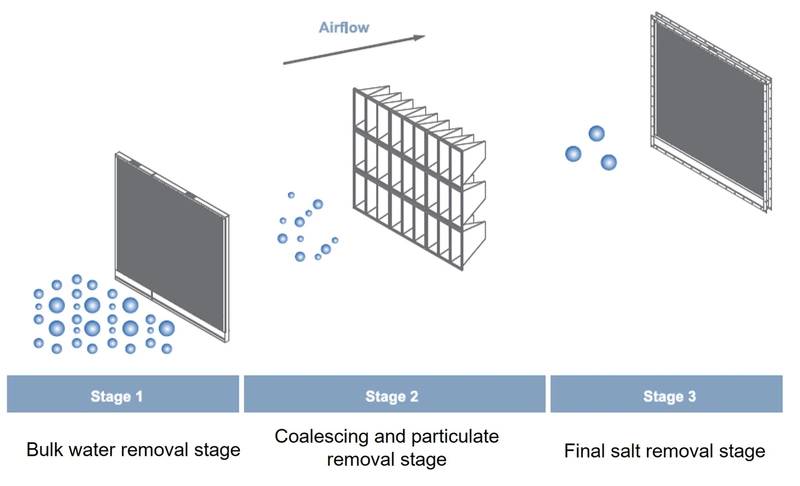
An inertial marine vane separator is the first stage. In this component, a assembly of which force the air stream to change direction multiple times, which removes large diameter liquid droplets and bulk water. Downstream of this a second, coalescing filter, stage, where any fine droplets that pass through the 1st vane separator are forced to coalesce/agglomerate, meaning they become larger and then removed entirely from the airstream by the 3rd and final stage marine vane separator. All of this needs to be completed with the lowest possible differential pressure drop.
The Full Package
For effective gas turbine intake filtration, the necessary design considerations must be included from an early stage of the ship design process. However, the filtration system is much more involved than simply the vane separators, filter and coalescing system. A lot more factors need to be considered and configured when designing an air intake system for a GT. Aerodynamics, acoustics, inlet heating (anti-icing) and enclosure ventilation system design, all play a huge part in optimising overall system performance. Shock and vibration testing, and performance validation are also a standard requirement for naval applications.
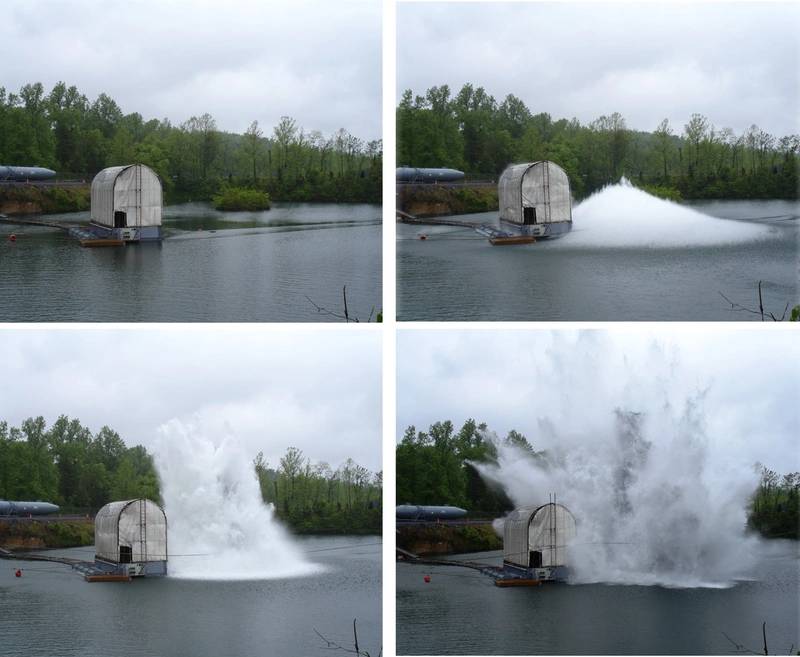
It is the complete, holistic design of the air intake system which ultimately ensures operational efficiency, reliability and availability is maximised and the vessel is ready to immediately react when called upon.
Another common feature for naval marine vessels are bypass (blow-in) doors. These allow unrestricted air flow to the turbine if the filter system is unexpectedly blocked somehow. In this case, the bypass doors open automatically when there's a very high-pressure loss to allow unfiltered air flow to bypass the filter housing, whilst ensuring GT operation remains. Again, the performance of these elements and the wider system are dependent on appropriate package design, which in turn demands the highest levels of experience and a deep understanding of aerodynamics, acoustics, computational fluid dynamics and many other requirements in addition to filtration. A comprehensive laboratory and field testing regime is needed to calculate all these parameters precisely and provide optimum filtration performance in a compact footprint with reliability and availability of the asset always at the forefront of considerations.
With fears of conflict growing and a higher priority given to military security, it is clear that more investment in naval vessels is taking place. Choosing the right partner to ensure gas turbine reliability is therefore critical. However, intake filtration is much more than salt removal performance given the requirement for extremely high velocities and the aerodynamic demands this places on design. There is also the need for a compact footprint and the flexibility to meet GT performance and airflow requirements in a highly challenging and restricted space. There’s the paramount demand for absolute unfailing reliability and quality over decades of service that a vessel type requires. Ultimately, it's this full package design that ensures naval marine vessels enable our armed forced to provide the military protection we need.
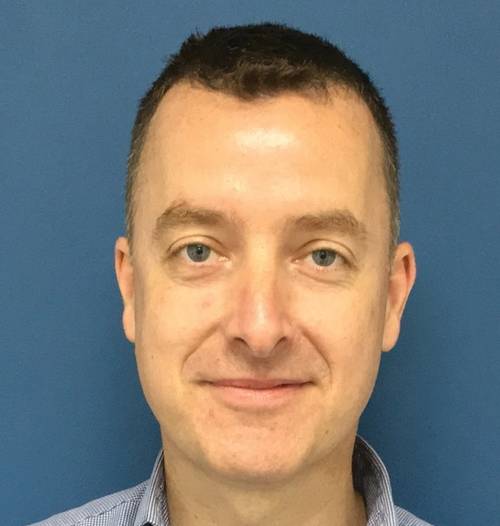
About the Author
Pete McGuigan is a Market Manager for Gas Turbine Filtration within the Filtration and Energy Solutions (FES) division of Parker Hannifin. Pete has published several papers, including at ASME and I-INCE.