Leading Off
Subsea Cable Failure
Data & Design: The Twin Approach to Solving Subsea Cable Failure
By David Hoyle, Senior High Voltage Materials Engineer at the Offshore Renewable Energy (ORE) Catapult
In past decades, the UK has established itself as an underwater technology pioneer with 40% of the global market share.
The North Sea oil and gas sector has fueled a great deal of this innovation to date. Still, as the energy transition accelerates, there is an opportunity for offshore renewables to provide fresh stimulus and innovation.
The subsea cables network is an area that we consider ripe for disruptive technologies: offshore wind’s future growth ambitions, profitability and energy output rely upon it.
Tomorrow’s cables will need to cope with more wind power and achieve reliability over longer distances as operations push further and deeper offshore.
Looking ahead to the future, we will also see the commercialization of floating wind platforms using dynamic cables, more high-voltage direct-current cables (HVDC), offshore hydrogen charging stations coming online, and the meshing of all of these into the ‘Supergrid’ of the future.
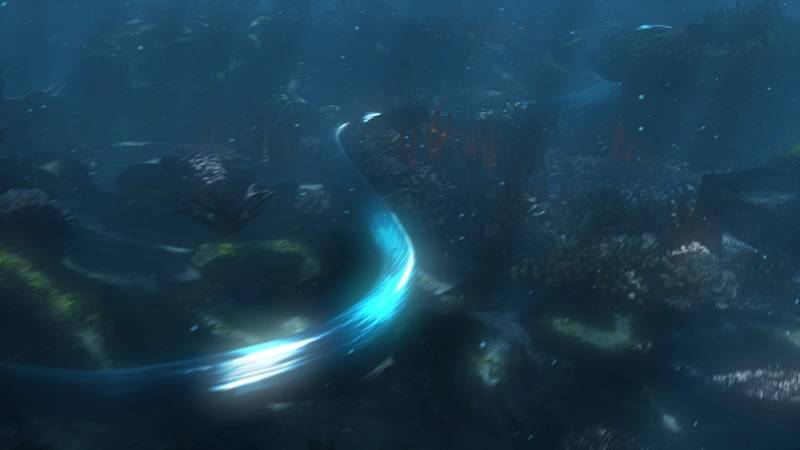
That is why innovation in subsea cable technology is heavily focused on investigating why cables break down and developing ways of predicting and pre-empting it. With the losses from a single cable outage costing as much as £12.5 million and taking three to five months to repair, there is a strong motivation to reduce failure rates.
The first step in our action plan is to gather better data. Limited or dispersed sources of cable failure data in the sector make it difficult to establish a clear picture of trends, root causes, and the effectiveness of management strategies. This spring, ORE Catapult launches ELECTRODE, the first program of its kind that will continuously collect anonymized data around subsea cable failures in offshore wind. We will take this vital operational data from offshore wind farms and anonymize it for trend analysis.
Another project underway in our research labs is monitoring the behavior of dynamic cables, which will be used for floating wind turbines, to anticipate failure due to water treeing within the layers of insulation (dielectric layers).
By being able to predict points of failure from the start, floating wind operators will be able to conduct pre-emptive maintenance, halving the repair bill for their wind farm in one move.
Whilst predicting failures will have a hugely positive impact on the industry, I believe that it still needs to be combined with innovations in the cable design that will improve protection from failure and provide asset managers (and insurers) with heightened confidence in their future reliability.
Self-healing materials
An interesting branch of research that promises to build resilience into design is the use of self-healing materials. This solution equips the cable to heal itself, preventing fatigue-related micro-cracks from developing into larger, more damaging effects.
There are different approaches to self-healing technology, including chemical and mechanical. A chemical solution would use micro-capsules containing resin that can break open in response to a crack in the material. Once released, the resin re-cures the material and repairs the damage. Mechanical self-healing solutions react to damage slightly differently: the material responds by swelling to fill a crack or void.
In collaboration with industry, ORE Catapult has been testing these solutions in its hyperbaric pressure chamber and materials laboratory at the National Renewable Energy Centre in Blyth, Northumberland.
This includes an Innovate UK-funded project to investigate the potential of a water-activated, self-repairing cable layer, and early results have shown promise in its water-blocking abilities. This is especially good news for the dynamic cables for floating wind which typically experience greater mechanical stress during operation. Self-healing water-blockers would keep water out of cable insulation systems and prolong their life expectancy.
Although at an early stage in development, the future potential for self-healing innovation to reduce subsea cable failure is an exciting area of research for the offshore wind industry. I’m looking forward to seeing the results of our work to demonstrate how effective it could be, and of course, how it can become a key solution amongst other research to de-risk and significantly reduce costs associated cable failure.
Offshore wind giant Ørsted has made a warranty provision of 800 million crowns after it discovered cable problems at its offshore wind farms in Europe.
Investigations into the extent of the issue are ongoing, Chief Financial Officer Marianne Wiinholt told a media briefing but added the problem was limited to ten offshore wind farms at most. They are in the United Kingdom and Continental Europe and equipped with a cable protection system Orsted no longer uses.
Orsted estimated fixing the problems could cost 3 billion crowns in total between 2021 and 2023.
Sydbank analyst Per Fogh described the issue as a "significant expense," but said Orsted's underlying business was doing well, despite earnings coming in below expectations.
By Offshore Engineer Staff