Five Things to Consider to Increase the Value of Digital Twins as part of Digital Transformation
By Leo Learth, Upstream Oil & Gas Manager, Radix Engineering and Software
Much has been said about Digital Twins. It has the potential to bring huge value to the oil and gas industry. However, in the last couple of years, the topic became an empty buzz word and many companies have developed software to get a grasp of their own concept of Digital Twin, without thinking about the bigger picture and the particular challenges of the Oil and Gas industry. At the end, the new software becomes another silo to keep and maintain, and organizations lose the chance to build an infrastructure that will serve as a solution enabler.
The Digital Twin topic is one component of a digital transformation. It typically has three levels of granularity: Enterprise, Asset and Main Equipment, each one including their own different data sources; data standardization (naming conventions, anthology and taxonomy); and data processing instances (such as compilations, simulations, rollups etc.), that may or may not be integrated among themselves.
However, a good digital transformation implementation is not about technology, breaking silos and systems integration. It is in fact about people, processes and responsibilities joining to achieve business and financial goals enabled through technology. Some key aspects I have observed in a good digital transformation program are:
- Know what needs to be achieved – Although a digital twin implementation brings indirect gains and may serve as an enabler of new continuous improvement programs, it is important that the teams know ahead of an implementation what business and financial results need to be achieved. These expectations must be communicated to the entire team and stakeholders together with their methods of measuring success (success criteria). A lack of methods to measure success often lead organizations to overspend in these implementations.
- Start small and grow – Even though you believe you have the best concept and architecture; you will probably be learning along the way. The best way to minimize risks and overspending is breaking down projects into small measurable chunks and build them one small piece at a time. This also takes into consideration the human factor: the end-users will learn with the phases, and will provide more value to the tool that will have a greater chance of adoption.
- Take the chance to organize the house – A project that become an enabler serves as infrastructure to other projects. As a digital twin often integrates different silos in transactional, engineering and real time data, it is important that the organization takes the chance to align and implement an enterprise wide taxonomy that is both able to correlate all these realms of data, and appropriately measure their quality, as well as minimize future interfaces. This is often done in a well-managed standardization layer.
- Adopting a specific vendor tool is one of the possible ways to achieve what is needed – One of the most common failure causes we have seen is that some organizations marry to a specific vendor and not to their own concept. The tools must be accelerators to achieve the concept and companies must not put all eggs in a single basket. Each selected vendor must solve one specific problem and be easily switched if the project needs.
- It is all about people – Remember, a system is made for people to use and benefit from. It is all about them. Build a forum of end users and communicate with them, even if it is not ready yet. During the implementation process, it is very important to capture their thoughts, comments and feedback. It is the only way to go through the adoption process with maximum buy-in and also keep them engaged enough to rely on the tool.
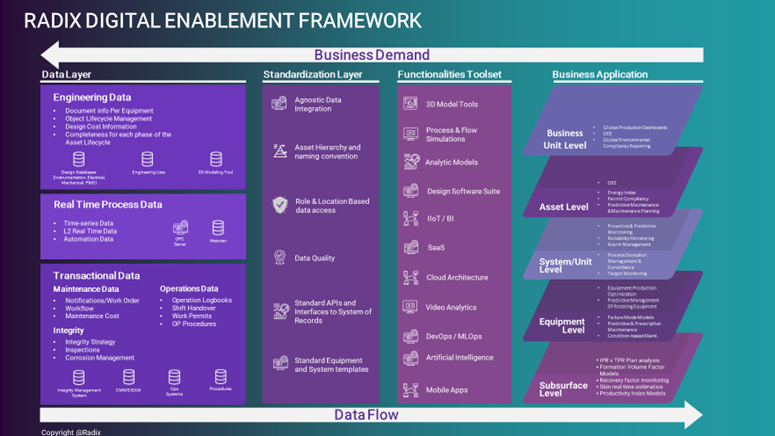