Digitalization
Cloud-Based Wave Monitoring
Catching the (Miros) Wave
Real-time, cloud-based wave monitoring helps offshore operators perform more efficiently and safely, as Jonas Røstad, Chief Commercial Officer, explains the premise behind ‘Sea States as a Service.’
By Greg Trauthwein
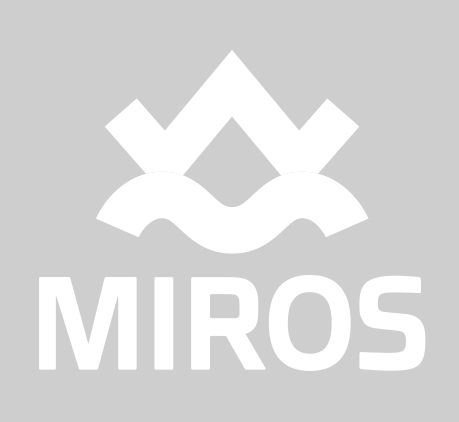
Necessity is the mother invention, and Miros started in 1984 as a ‘geeky science project’ to provide better sea state data for platforms in the North Sea – which at the time relied on buoys; buoys that provided good data but were ‘maintenance hungry.’
Born was a solution that was nurtured with the Norwegian national oil company Statoil (now Equinor), to create “the first prototypes of this wave radar, which was put on oil producing platforms in Norway and gave the same parameters as wave buoy would give out,” said Røstad in an interview at the company’s Oslo headquarters earlier this year.
Nearly four decades later, Miros has evolved into a technology company that specializes in measuring the ocean surface, providing sensors and systems for environmental monitoring to the offshore and maritime industries, including wave and current monitoring as well as oil spill detection.
Offshore Wind Efficiency
“Today, typically, offshore wind projects use weather forecasts, but what we can do is to give the actual sea state at any given point,” said Røstad, helping, for example, vessel operators in the offshore wind sector cut wasted vessel trips and increase safety.
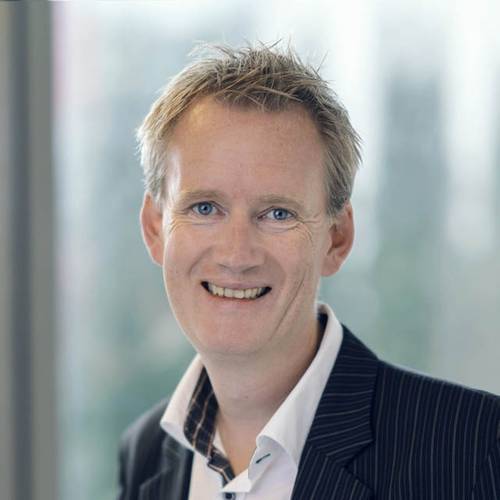
Jonas Røstad, Chief Commercial Officer, MIROS
“They start on the trip, and when they get out to the turbine, it turns out that the wave height is too high, so they have to make a U-turn and go back, which can also lead to turbine downtime. What we do is give real-time wave measurement within the [wind farm], and maybe mix it with the weather forecasts. It's all about maximizing the weather window.”
In fact, on some really large offshore wind farms with diverse bathymetry, wave conditions can vary significantly at different points in the wind farm. In such a dynamic and fast-changing environment, absolute accuracy is always an issue, but Røstad points out that Miros’ instruments are “the only DNV-certified wave measurement device(s) on what they call the Alpha factor.”
A big value proposition for the Miros solution is the fact that the sensors feeding data to the system are dry-mounted, not in the sea and directly exposed to saltwater, significantly reducing maintenance.
Once installed and operational, they simply shoot the data stream up to the cloud, making the information easy to access for anyone with proper credentials. The layout of the sensors is unique to each wind farm, dependent ultimately on the layout of the farm, water depth, and bathymetry.
“[Via a pair of case studies] we have found that if we arrange these sensors right, then we can reduce turbine downtime by 1%.”
Naturally there are savings to be had on the vessel side, too. In a study with ORE Catapult in 2019, Miros found that by utilizing the data from its wave sensors, CTVs and SOVs saved up to 5% of fuel and CO2 emissions, too.
Studies are one thing, real-world operations another, and earlier this year, Subsea 7 awarded Miros Group agreements to install its internet of things (IoT) dry-sensor WaveSystem on three of its pipelay support vessels to deliver accurate wave measurements via Miros' cloud-based graphical user interface (GUI) Miros.app.
As part of three 3-year contracts and project requirements for the monitoring of wave and current to a water depth of 10 meters, WaveSystem will be installed on Seven Waves, Seven Rio, and Seven Sun vessels, and the deal will see Subsea 7 gain access to Miros Cloud services delivering real-time sea state data.
On awarding the contract, Filipe Salvio, Operations Manager at Subsea 7, said, “the cloud-enabled WaveSystem onboard our three pipelay support vessels allows us to deliver the best service to our customer independently of offshore weather conditions. This system provides us with accurate wave, current, and speed through water data granting us to work safe, precise, and highly effective at all times”.
According to Røstad, Subsea 7 aims to use its system as a competitive advantage: “Subsea 7 wants to promise their clients that they can work more hours than the competitor. With knowledge about the sea state, they can work more hours because they take away that uncertainty.”
The other thing is that Subsea 7 can link this to external systems, like dynamic positioning, for example, to check if they can increase the working limits of the vessel based on real data. “So if you have limits and with experience from the data and how the vessel moves, they can actually change the limits to a higher number based upon the real-time data. Every vessel that has a limitation on the sea states [in which it could work] would benefit from this.”