Tech Feature
Digital Twins
Digital Twin Technology Can Help Floating Offshore Wind Realize its Enormous Potential
One technology that will be critical in the energy transition is floating offshore wind, which, although in its adolescence, is a rapidly maturing technology with enormous potential. It is not without its challenges, but digital twins are here to help.
Guillaume Lechaton, Sales Director for Wind and New Energies, Akselos, and Seth Price, VP, Head of Technology, Principle Power.
WindFloat Atlantic - Principle Power's floating wind farm off the coast of Portugal
© Principle PowerThe world is in the midst of a huge challenge. To avoid the worst of climate change and leave a habitable planet for future generations, we must transition to net-zero emissions by 2050.
One technology that will be critical in the transition is floating offshore wind, which, although in its adolescence, is a rapidly maturing technology with enormous potential. In European seas, approximately 80% of the world’s offshore wind resource potential is in water deeper than 60 meters, where the most reliable renewable energy technology that can be built is floating wind turbines.
Obstacles to Growth Holding the Industry Back
However, there are several barriers to growth that are hampering the potential of offshore wind and putting at risk the transition to net-zero 2050.
The first of many challenges is the growing expense of sending technicians offshore to perform routine maintenance or fix issues due to their location far out at sea. To yield the highest output, floating wind farms are located in remote areas and are highly exposed to the elements. Unlike other offshore industries, wind turbines are trickier to navigate safely in bad weather without the protection of platforms.
Also, weather windows limit the time work can be conducted safely and efficiently. If a significant issue of fault requires a turbine shutdown, it may have to remain inactive for some time if the weather does not permit engineers to reach it safely to bring it back online - resulting in a loss of time and money.
A lack of reliable data is also slowing progress. As a relatively new industry, floating wind has little performance data to draw on to inform engineers of design improvements that could be made to make operations more efficient.
To date, design safety factors have also been based on conservative factors commonly used in the offshore oil & gas space, which, while helpful, are not directly applicable. With the data made available via new and exciting technology, designers can challenge these conservative factors to optimize the design for the specific risks and failure impacts aligned with floating wind projects.
Digital twin technology can be the solution
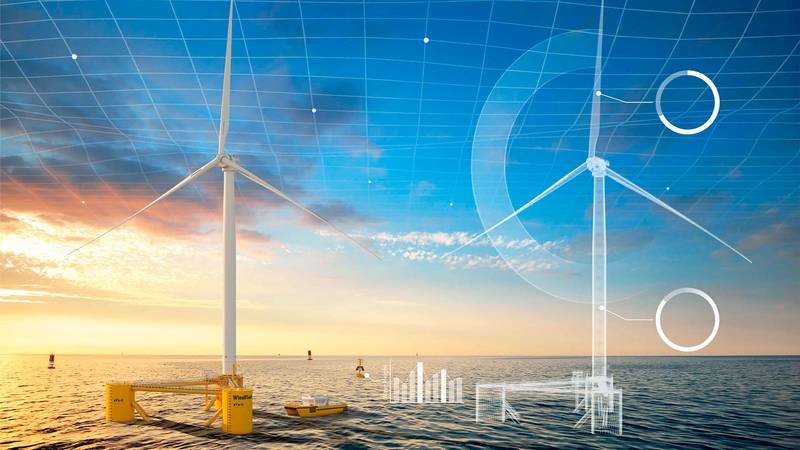
Digital Twins are real-time, virtual representations of assets such as floating wind turbines
The floating offshore wind industry can overcome these challenges and supercharge its growth by embracing digital twins, virtual representations of physical, real-world objects.
To create a digital twin of an asset, engineers first build a detailed model, reflecting the “as-is” condition as much as possible, and then pair it with real data, including inspection and sensor data. This data is then fed into the model to create a structural digital twin. This twin can run near real-time simulations, analyze performance issues and suggest improvements that engineers can make to the original asset to increase energy output.
Since they are fed with near real-time data from the asset, digital twins provide a clear picture of asset health which operators can use to pinpoint issues proactively before they become critical. As a result, operators can fix problems before they escalate into costly failures, reduce the number of expensive and time-consuming trips offshore, and schedule work to minimize waiting on weather and lost production.
Digital twin technology is being developed to optimize floating offshore wind platforms.
Today, Principle Power, with digital twin pioneer Akselos, is building a structural digital twin of the WindFloat Atlantic offshore wind farm.
This digital twin is being constructed as part of the DigiFloat Project - aiming to develop the world’s first digital twin software tailored to floating offshore wind applications. When completed, the solution will help Principle Power reduce the amount of maintenance required on the assets and provide valuable, actionable data to help further improve this growing industry.
The floating wind industry has enormous potential to scale the energy transition and drive us to net zero by 2050.
By embracing digital twin technology, the industry can reduce the maintenance required on turbines and platforms, helping to improve operations, bring down costs and increase uptake. Moreover, the more systems that utilize digital twin technology in the future, the more valuable data will be available to guide designers in creating optimal designs.
About the Authors
Seth Price, VP, Head of Technology, Principle Power Inc.
Seth Price is a licensed professional engineer with a diverse career in offshore energy sectors spanning more than a decade.
Price brings a passion for the floating offshore wind industry after starting his career in offshore oil & gas engineering services. He brings about extensive project experience in floating hull and topside systems spanning from conceptual studies to detail design and fabrication management.
Price has managed diverse and multi-disciplinary engineering teams across a multitude of geographic regions.
HE has a Bachelors' in Civil Engineering from Lafayette College and a Masters' in Structural Engineering from Texas A&M University. He is energized by strategic technology development and cultivating a happy and intellectually curious workplace.
Guillaume Lechaton, Sales Director for Wind and New Energies
Guillaume Lechaton is Akselos’ Sales Director for Wind and New Energies, driving global sales and business development in the offshore wind industry. Guillaume has over 11 years of experience in the wind industry, having worked for a world-leading asset owner and a top three wind turbine manufacturer.