Feature
Floating Power
Floating Power: Electricity and Future Fuels
Beyond shoreside hotel power, there’s floating, utility-sized power, or floating power plants. At the core of these are some familiar names in marine propulsion and national grid power — Wartsila, Siemens Energy, MAN Energy Solutions. Challenging the status quo and working with these paradigm power producers are consortia of companies from the renewables and offshore sectors. Driving development are developing-world demand, the renewal of diesel plants, subsidy and electricity shortages worldwide. Sweetening the pot is a chance to produce unproven fuels hydrogen and ammonia.
By William Stoichevski
Methane-driven: Wärtsilä’s triumphal Kivuwatt FPP floating in and drawing methane from Lake Kiwu, Rwanda, in 2016.
Photo: WärtsiläLow-water marks in reservoirs that once provided the cheapest electricity in Europe now trigger electricity price shocks and national power-bill bailouts in the world’s richest country. The government action here and everywhere during the 2022 energy crisis are stirring new faith in power projects. What follows is a survey of floating power players and projects with heavy backing.
In Norway, going greener has pushed bewildered politicians into supporting the electrification of oil platforms from land. That has helped jack-up power bills, as the raw, equivalent diesel power required by an offshore oilfield can be equated to the power needs of a city. The solution, says a coalition of companies in Norway, is floating gas-fired power plant, or FGPP, that captures and injects carbon-dioxide into subsea reservoirs and can send power to shore.
As elsewhere with emergent floating power, Siemens Energy is at the core of Norwegian designs to float a gas-fired power plant, or FGPP, out to somewhere between land and power-hungry offshore platforms. Together with gas process engineers, Kanfa, Siemens Energy is part of the Blaa Stroem (Blue Power) alliance that aims to put a GPP aboard a Sevan cylindrical rig and sequester and pump the CO2 it produces, its flue gasses, into the oilfield reservoir as “gas lift” to keep pressure and oil production up and increase reserves: or just to store the maligned gas permanently in a saline aquifer. The floater’s tanks could be used to store fuel, CO2, well stream or, conceivably, hydrogen — turning “grey” (flue-gas derived) hydrogen “blue” (produced via steam methane reforming, or SMR, with carbon capture and storage/sequestration, or CCS). H2 can also be derived from heated sea water (electrolysis) or directly from natural gas.
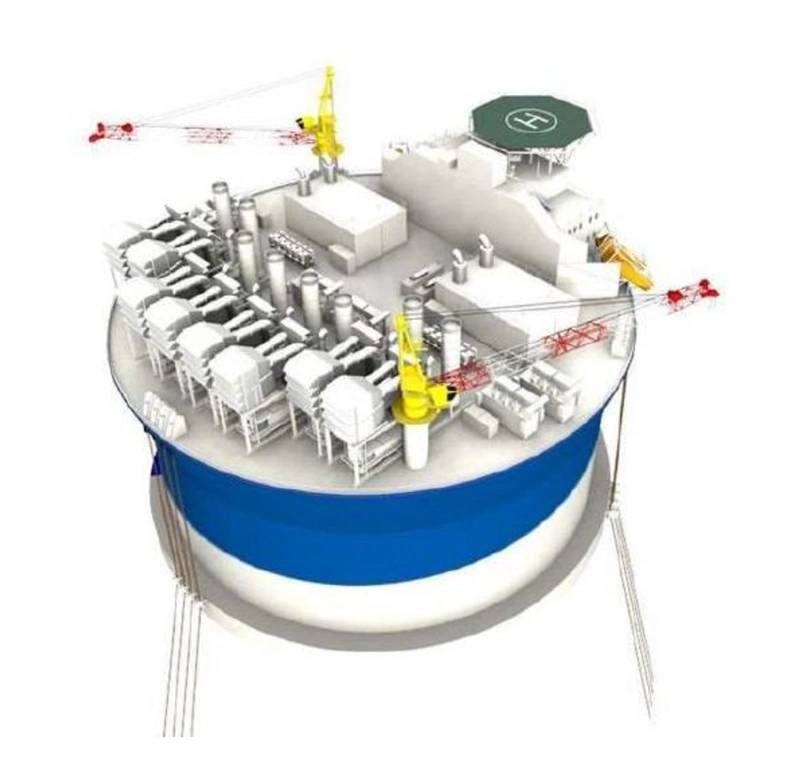
Dual-use: an engineer’s design of an SSB GPP able to supply electricity to both offshore installations and onshore population centres while sequestering carbon-dioxide.
Floating Gas Plant
Yet, there’s much more to the idea’s potential than meets the eye. A Sevan SSP engineer Maritime Reporter spoke to says the concept is very scalable for shoreside power production if desired. Conceived by Erling Ronglan (who studied at Norway’s answer to MIT, NTNU), the project’s heart is technology from a “start-up” called Ocean GeoLoop, part of a greater alliance that includes Siemens Energy and others under the Blaa Stroem umbrella.
“The business model is to connect with (offshore or grid) operators in order to provide offshore power to their installations,” Ronglan says. “There’s a discussion in Norway right now on power from shore to sites offshore, but this is an alternative and a better way of utilizing electricity and producing it locally and using it locally.”
Launched two years ago, the combined Ocean GeoLoop carbon capture storage and utilization tech, or CCSU, and the floating offshore or nearshore GPP attracted shareholder Chevron in September. Yet the plan — to power the platforms and, possibly shore — offers the chance to produce “blue H2 ” and “blue power”. Hydrogen is central to an EU scheme to get largescale (but very modular) H2 -electrolyzers producing ammonia fuel and H2 fuel cells onto BMW’s — ASAP.
We haven’t done any benchmarking, but for a newbuild like this — with all the facilities available at a typical yard — it should be cheaper than purpose-building (a GPP with CCS) somewhere on land, where they might be lacking in (key) people and (vital) equipment. The hull doesn’t drive costs much, and inshore, we might change to a different hull to be cheaper to construct Erling Ronglan,
Ocean GeoLoop.
Chevron’s $10 million investment in the concept gives the major greener hydrocarbon production and, if desired, upstream and downstream gas and electricity — or even tradable carbon credits for the sequestered CO2 — plus the inherent earnings.
Ronglan, an FPSO expert with Sevan, is aware that Siemens already has a number of floating barge power concepts (keep reading!). The Ocean GeoLoop/Ocean-Power CCSU tech can alone, or with a GPP, also be barge-mounted. In the Blue consortia, Siemens Energy is providing engineering plus the floater’s grid equipment and FGPP’s combined heat and power gas- and steam turbines and generators.
The FLPP-produced electricity offshore is seen costing from about $0.03 to $0.05 per kilowatt hour, or far less than prices charged by Norway’s land-based gas-fired power plants. Current electricity prices on land soared recently to as much as $0.70, before settling back down with government to about $0.27/kWh, on average.
CCS-to-Power
The cylindrical FPSO-style FGPP would bring CCS offshore while sourcing gas fields for fuel
“CCS … and yes power, because the idea of a GPP is to sell electricity and get fuel gas from a nearby host and produce electricity to sell to nearby platforms. But, also onshore. There is that possibility. Power cable is for any purpose, including power to shore. What we’re providing the Blue Power partners is electricity sales.”
Using traditional gas turbines, “There is nothing new in that, but the exhaust from those turbines is where we use the GeoLoop tech in order to capture CO2 from the exhaust,” Rogland says.
A barge of the same tech would work nearshore. The FGPP’s draft can be reduced, and plant weight is but a fraction of a storage tank. Its (beam) is “very small”.
“The draft is no problem. You can keep it quayside,” he says, when asked if it could function in FGPP-only mode.
With Siemens turbines providing primary gas-fired power, or heat and power, Ocean GeoLoop’s CCS tech may also provide surplus electricity. While still in the pilot-stage, well-entrenched backers can rejoice at the Ocean GeoLoop’s successful capture of phosphorous from a papermill’s water supply, another aspect of the loop. The turbine tech also seems to show that any flue gas can be captured and “burned” for electricity production. The papermill pilot is succeeding in parallel with an industrial-scale CCS build-up. The “applied CCS”, or CCUS — “utilization” — is partly aimed at offering industry extra electricity.
Self-Finance
“We’ve not indicated a timeline for this second generating technology, whether onshore or offshore, it’s the early sprint from the design stage,” said Ocean GeoLoop CEO, Oddgeir Lademo, who cautions that, “It’s too early to say how the system will link to CCS. The CCS-power-generation part is a work in progress.” Moreover, “Utilization of the e-Loop is expected to provide significant positive cash-flow effects through sale of surplus energy to the emitters and/or downstream users.”
Company documents laud the “embedded electricity generating capacity of the e-Loop”, from which surplus power is derived from the “100-percent” of flue gases captured by its “point-source” process unit. “The technology is designed to achieve … unprecedented capacities,” including being “100-percent self-financed” plant, where Ocean Power or its industrial clients can produce electricity to cover its operation with a surplus sold to clients. The process plant, the company says, «mimics nature» by using small heat differences between liquids and gases to power a hydropower turbine.
Floating power: the arrival in downtown Santo Domingo of a Siemens Energy Seafloat, complete with energy storage.
Siemens Energy
While the Norwegians look offshore with concepts that also serve shoreside industry and potentially “regions”, Siemens Energy’s flagship FGPP, Seafloat, keeps evolving and “is relevant for all locations with access to the sea or large river systems”.
“SeaFloat can replace conventional power barges which often run on diesel or heavy oil,” says Siemens Energy SeaFloat sales lead, power plants, Stavros Zissis. The most recent SeaFloat, the del Mar III, was put together in Singapore by shipyard and gas plant fabrication crews. Modular Siemens plant was hoisted onto a fabricated barge which was no match for the season Sinaporeans accustomed to mammoth semisubmersible builds. The voyage of Estrella del Mar III showed it piggybacking onto a heavy lift vessel and passing on its barge through narrow canals.
Building blocks: a graphical rendition of a Seafloat showing modular process-plant placement.
Shipyard-capable: The Seafloat hull as it appeared in 2021 when completed in Singapore.
Seafloat
“You cannot simply put a gas turbine constructed for land-based applications on a floating vessel,” Zissis says, adding that SeaFloat GPPs are “marinized” tech “optimized” and specially made “to withstand motions, accelerations, and hull deflections”.
“The gas turbine and steam turbine packages are installed on three-point mounted frames, forming single-lift structures that facilitate and expedite the installation and erection efforts at the shipyard. It’s like putting together big LEGO bricks,” he says. SeaFloats, he adds, are “wet- or dry-towed” from the shipyard. The barge’s layout and size are dependent on whether the unit is fully integrated with LNG storage, regasification and power plant — the Siemens FSRP concept — or related to power output.
The 150-megawatt (MW) combined-cycle Estrella del Mar III began powering the Dominican Republic with its two SGT 800 gas turbines in 2022, two years after being ordered. It has “5 to 10 megawatts” of power from energy storage onboard for “primary frequency response”. SeaFloats mainly come in 145/150 MW, 220 MW, and 300 MW models — increasable by lifting aboard more “blocks”, modules that might in future be hydrogen electrolysers to enable both H2 and ammonia production. The LNG storage capacity can reach 180,000 m3. The barge itself can be floating, fixed, or bound to a mooring dolphin, a steel construction piledriven into the sea or river bed and visible above water.
The Estrella del Mar III is reportedly “quieter” than downtown Santo Domingo, where it’s moored. Its size — 80m x 35m — is half the size of a comparable, land-based plant.
At-anchor: a mooring dolphin used to secure a FPP.
Integrated plant: inbound LNG, an LNG terminal and a FGPP.
Propulsion Players
Propulsion powerhouse Wärtsilä is also a major provider of grid power in the United States.
Wärtsilä delivered the FPP Dominican II to the same Caribbean nation. The Finland-based company has also delivered diesel FPPs, and now gas or dual-fuel power plants are sought, as they allow for the switching of fuels as markets and supplies swing. Combined cycle heat and power steam turbines and desalination are offered as options. “When required, various NOx and SOX reduction options are available,” a commercial note says. “When natural gas becomes available, plant can be converted”. How’s that for flexible fuel!
Like the other barge and cylindrical “drum” FGPPs, Wärtsilä points to “short construction time” for barges that range in length from 64.8 m to 90 m. All are 27.4 m across.
Air intake filters below exhaust outlets, roof-mounted ventilation and radiators make models like the Wartsila 32 Power Barge ideal for the tropics. Between 1990 and 2011, FGPPs in Bangladesh and Papua New Guinea joined two in the Dominican Republic on the Wartsila hot weather, salt water client list.
MAN Energy Solutions
MAN Energy Solutions also offer flexible dual-fuel or gas engines (as well as trusted diesel models). MAN bases its LNG-to-power floater concept on the flexibility premise, as well as efficient gas turbines that deliver 10 MW to 300 MW. It’s about “low-cost energy production” and “independence from gas suppliers”, both super-topical in November 2022.
MAN gas turbines of from 6 MW to 13 MW offer gas-fired power generation fed from centrifugal pumps transferring LNG to a vaporizer “injecting” natural gas. Condensing turbines or steam turbines offer the ability to produce electricity from a variety of energy feedstocks, where turbines are either “backpressure” or “saturated” types in modules meant to work with some of the types of innovations we’ve obliquely referred to. The MAN steam turbines target combined heat and power; biomass production and burning; steam from concentrated solar power; geothermal energy (the Icelandic government is an Ocean GeoLoop partner); waste-to-energy and regeneration in energy storage. The MAN steam turbine power-generation portfolio — turbines like the new, “urban and industrial” MGT6000 — covers the range up to 180 MW, or the equivalent of a medium-sized hydropower dam.
Hydrogen PP
In the most technologically advanced states, especially in Northern Europe, “green, blue and pink” hydrogen are touted as the future, and gas plant that can burn gas now and hydrogen later is seen as the right backstop.
“With our H2 -ready concept, we can confirm we are in the planning phase for new power plants suitable for future use with hydrogen,” Zissis says. “As a turbine manufacturer, we ensure the burners and combustion chambers are designed for H2 , as this has different combustion properties than natural gas. In addition, other auxiliary systems, such as piping and explosion protection, must be designed … The independent certification body TÜV SÜD issues certificates for H2 readiness in a power plant’s design phase,” he says.
So, there’s a FGPP’s readiness to take on hydrogen as a fuel. There’s also a hydrogen supply chain, including bunkering for and by vessels that’ll service floating hydrogen power plants. Hydrogen supplier networks, some only in name, have mushroomed across Europe in imitation of the Boston medical cluster (much lauded in these parts). Norway alone has several “zero-emission supply chains”. “Centers of excellence” address energy transition strategies, and hydrogen “learning” is on the agenda all across the Continent.
Still, Class informed the Norwegian Arena Ocean Hyway Cluster that “there are uncertainties” in H2 infrastructure. From handling to the production of compressed hydrogen, liquid hydrogen and ammonia.
Water-to-Fuel
It's in the Far East, however, where a certain hydrogen PP offers clarity on the future path of “floating HPPs”.
September 2022 saw Keppel Energy decide to build a $526 million, 600 MW advanced PP based on a combined-cycle gas turbine. Mitsubishi will engineer and build the Keppel Sakdra Cogen plant as “the first hydrogen-ready power plant in Singapore”, a communique heralds. “Running initially on natural gas as primary fuel, the (plant)) is also designed to operate on fuels with 30-percent (H2 ) content and has the capability of shifting to run entirely on (H2 ). Starting in 2026, its produced steam will bolster industry energy and chemicals customers on Jurong Island.
As certain fuels are banned (at least in emissions-control areas, or ECAs), the ability of FPPs to produce future fuels, like ammonia, might become “standard”. The Keppel deal includes an “aside” MOU with Mitsubishi Heavy Industries for “a feasibility study on the development of a 100-percent ammonia-fuelled power plant on a selected site in Singapore”. That’s 3-for-1: gas-firing at the same plant gives way to H2 either from water or natural gas, which is then converted to ammonia. Energy trilemma solved.
“When completed, this asset will grow Keppel’s power generation portfolio from the current 1,300 MW to 1,900 MW,” Keppel says, although Mitsubishi Power CEO, Osamu Ono, adds, “Mitsubishi … looks forward to supplying … Sakra Cogen …with our hydrogen-ready JAC gas turbine.” The race is on.
There’s no word on whether compressed or liquefied hydrogen will be the goal at Sakra, or whether refrigerated or pressurized liquid ammonia will be made. There’s no certainty, either. “Today 95 percent of (H) is produced from fossil fuels, more than half is used for ammonia production, and almost 90-percent (of that) is used to produce fertilizers,” the Lloyd’s Register report says (for perspective).
Capture loop
As for the Ocean GeoLoop? The Norwegians whose designs and capital have helped fabricate many a gargantuan, super-complex, Singaporean floater newbuild are already building a small and a large pilot, at least of the CCS.
Whether a Sevan cylindrical semisub with GPP on top, or a barge, ship and fabrication yards are in our survey are not expected to have difficulty building FPP floaties or their associate plant (although Siemens suggests the “controlled environment of Singapore” for a newbuild FPP). The plant providers have perfected their module stacking procedures, so “a crane” and secure wet dock are all the physical pieces that need to be in place (followed by heavy lift availability).
Forecasts
“We haven’t done any benchmarking, but for a newbuild like this — with all the facilities available at a typical yard — it should be cheaper than purpose-building (a GPP with CCS) somewhere on land, where they might be lacking in (key) people and (vital) equipment,” Rongland says, adding, “The hull doesn’t drive costs much, and inshore, we might change to a different hull to be cheaper to construct.”
The Blue Power partnership comprises many parts. “We provide the electricity and the transport (of gas and the FPP with CCS). We can even own and operate the installation if required.”
Indeed, looking around the North Sea and elsewhere, offshore and grid operators seem to like that model. So do certain national governments.
Point of capture: a graphical drawing showing the theoretical layout of CCS and CCSU capture tech.