Case Study
Decommissioning
SIMOPS & the Schooner Platform Decommissioning
A summary of the operational benefits of SIMOPS – as seen during the Schooner platform decommissioning campaign.
By Drew Duncan, Senior Well Abandonment Engineer, Well-Safe Solutions
Simultaneous Operations (SIMOPS) are multiple activities carried out at the same time in a single location, often in close proximity to one another. The risks of SIMOPS working on a live marine asset, often in a small workspace, requires careful mitigation so that personnel and assets are kept safe.
The Schooner platform, operated by Norwegian operator DNO, is located in the Southern Basin of the UKCS. A twelve-slot Normally Unmanned Installation (NUI), 10 of the 12 slots have wells still open to the reservoir. One slot has a previously abandoned well and the last remains empty.
In typical scenarios, wells are abandoned sequentially, with wireline-based intervention carried out to install barriers and remove any hydrocarbons present in the wellbore (stage AB0). The tubing is then removed with the BOP installed, with abandonment barriers set in place (stages AB1 and AB2). Conductor cutting and recovery is then generally performed as a batch operation as part of stage AB3.
Digital Slickline Operations
Well-Safe Solutions proposed a program of SIMOPS batch digital slickline operations to significantly improve operational efficiency and reduce the total cost of abandonment. This enabled eight of the 11 wells to be entered and abandoned to AB0 status, with two digital slickline units operated at the same time. One unit worked from the drill floor through a high-pressure wireline riser, while the second carried out operations from the Schooner platform’s weather deck.
Due to the tight space constraints of the weather deck, Well-Safe’s engineering team led the design, fabrication and installation of moveable beams installed below the drill floor, which supported the lubricator above multiple well slots and maximized the length of lubricator available for maximum toolstring length.
An unusual challenge in this scope was the discovery that one of the wells contained 14,000 ft. of slickline above a toolstring; present since 2006 when previous attempts at fishing had been unsuccessful. Peak mobilized their heavy-duty fishing system, with approximately 11,575 ft. of wire successfully removed over 24 runs. This successfully cleared the tubing and allowed access for the deep-set plug.
As we weren’t sure exactly how long it would take for the execution of fishing operations, our digital slickline SIMOPS enabled three other wells to be entered, abandoned and suspended concurrently. This not only delivered a considerable time saving for the client, but crucially was able to be carried out with no detriment to operational safety.
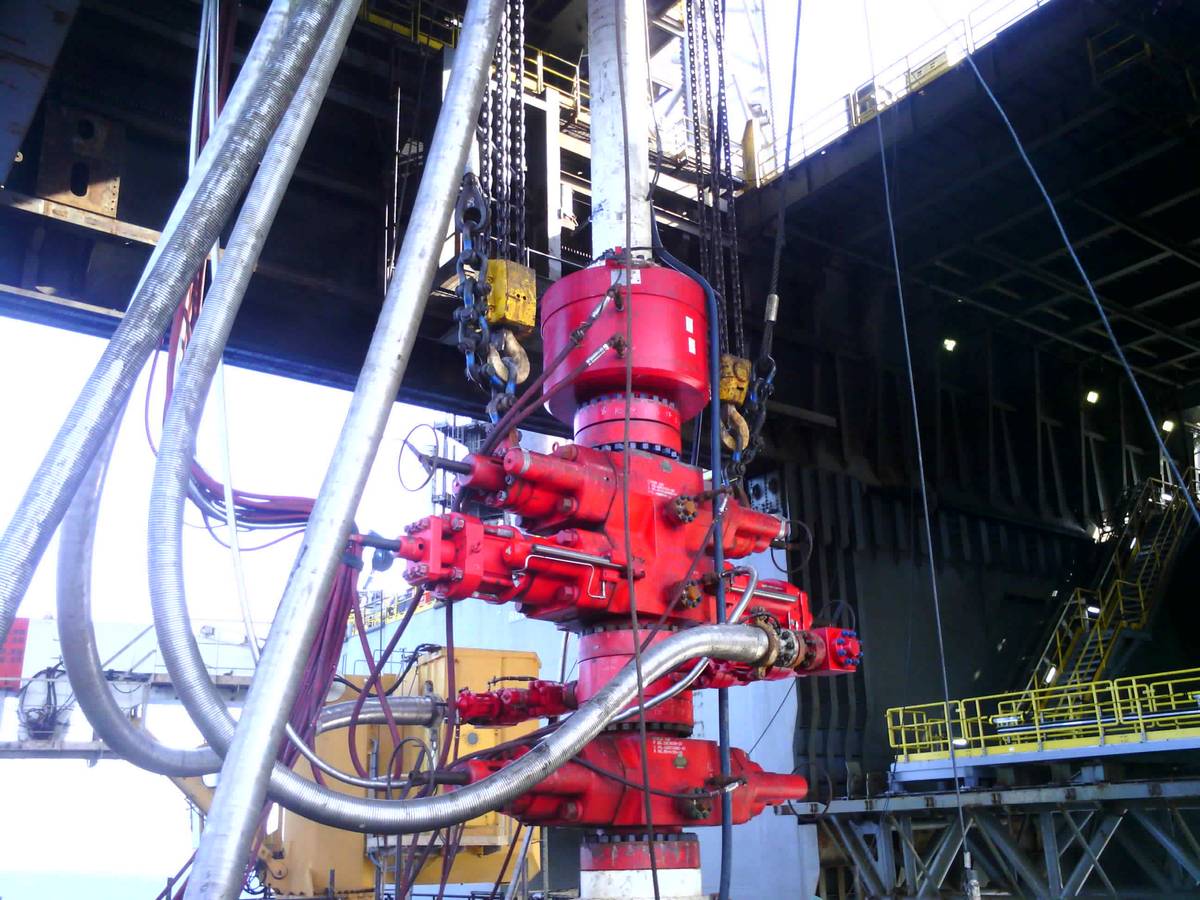
A key tenet of Well-Safe Solutions’ offering is its dedication to collaborative working, enabling lessons learned to be shared throughout the industry. Our drive to reduce the cost of decommissioning for our client led to the use of several specialist technologies.
Two digital slickline units were used to support SIMOPS, using industry-leading digital slickline services. This method enabled execution to be streamlined by combining two services into one cable conveyance. Real-time services including performing mechanical jarring, explosive and non-explosive plug-setting and utilizing tubing cutters.
In addition, this technology enabled a higher level of operational efficiency through reduced equipment handling, as there was no longer a requirement for additional rig-ups between conventional slickline and e-line (or wireline) equipment. Wellbore data was also enhanced by the digital slickline system’s ability to provide real-time toolstring pressure and temperature data.
Pressure wave valves provided by Oilenco enabled an additional run to be removed from the scope, following deployment of the blow-out preventer (BOP) and pressure-cycling of the valve. These intelligent practices further reinforced the time savings achieved by the SIMOPS carried out earlier in the project.
Every Little Bit Helps
The use of SIMOPS was not the only optimization measure used on the project. With operational efficiency one of the central goals of the scope, Well-Safe Solutions was able to halve the time the BOP was off the well, by ‘hopping’ it between wells. This avoided the removal of choke and kill hoses along with the bell nipple, which is normally a time-consuming process. This procedure enabled the high-pressure riser to be removed, the rig to be skidded to its new location, the tree to be removed, and the high-pressure riser to be reinstalled – all while the BOP remained suspended, increasing the value of savings for the client.
For NUIs such as the Schooner platform, day trips using helicopters for limited-duration work campaigns are the norm. Lack of daylight, as well as instances of poor weather, can create considerable difficulties in enabling access to and egress from the platform. Air-gapping operations, where surface well barriers are proved and flowlines are removed, were originally planned to be carried out ahead of the drilling rig’s arrival to the platform by way of a helicopter or walk-to-work campaign. Well-Safe proposed to DNO that this operation could be safely carried out as SIMOPS, with the air-gapping carried out simultaneously to the concurrent batch digital slickline activities.
SIMOPS methods enable Well-Safe Solutions to realize significant cost savings to benefit the client and the wider decommissioning industry, with no detriment to operational or personal safety.
About the Author:
Drew Duncan is Well Intervention Team Lead at Well-Safe Solutions, drawing upon over three decades of practical experience in well intervention techniques.