First Person
Floating Wind Engineering
A Developer’s View: Floating Foundation Choices
Challenges and opportunities in choosing the right material and design for floating wind foundations, drawing on the author’s experience from the Eolmed project and exploring the innovation gaps in the floating wind sector. Thistle Wind Partners (TWP) is developing two projects after securing rights to almost 400k m2 of seabed under the ScotWind leasing round in 2022. Currently in development is the Ayre Offshore Wind Farm, a 1GW floating-foundation project located 33km to the east of Orkney, and the Bowdun Offshore Wind Farm, a 1GW fixed-foundation project lying 44km off the coast of Aberdeenshire.
Johan Daelman, Floating Foundation Lead Engineer, Thistle Wind Partners
Thistle Wind Partners (TWP) was founded in 2020 by DEME Concessions, Qair, and Aspiravi as a wind development business with a focus on Scotland. While our founders have a combined 60 years of experience in renewables with projects across the world, TWP is the new kid on the block in Scotland.
We attract a lot of curiosity at industry events, especially when it comes to our plans for floating offshore wind development – one of our project sites, which lies 33km to the east of Orkney, will be a 1GW floating wind farm (estimated start of construction – 2029).
How are we approaching design selection? What are our requirements for suppliers and fabricators? As a ScotWind developer, we have also set ambitious targets for the use of the local supply chain in line with the expectations set by the Scottish Government and Crown Estate Scotland. We need and want to develop a robust local supply chain, and this is a major factor in how we will procure our turbines and components.
Eolmed: Learnings from France
I came to the TWP project fresh from working on the design team for the Eolmed Floating Wind Farm, a Qair project in the South of France that is now entering its construction phase.
My role was to conduct the combined elasto-aero-hydrodynamic analysis of floating foundation designs using numerical modeling.
We took a technology agnostic approach, initially considering concrete as an alternative to steel. The local market conditions meant that on this occasion, the choice landed on steel, and we are now in the construction stage.
At TWP, we are starting the process of choosing floating foundation materials and designs once again. Concrete and steel floaters are on the table for us, and we will be pursuing conversations with foundation designers, fabricators, and supply chain in the coming year.
We expect that this is an area of development that will move on fast as we consider the options, but there are a few known pros and contras for using concrete versus steel.
Being agnostic, with the stretching targets we have for local content, we are exploring various solutions such as steel or concrete.
While concrete (although containing a lot of steel) is a solution that seems intuitively easier to implement, steel is a material that allows us to design complex, modular and adaptable shapes. We are exploring the possibilities in the local Scottish supply chain.
You do need to factor in the cost of having to use steel for the reinforcement, and a solution that can provide concrete steel-reinforced foundations at a cheaper cost than steel alone would be of interest to us.
We also need to consider the carbon recycling footprints of both solutions as well. When we considered this during the Eolmed planning, and when all considerations were weighed, the difference between steel and concrete was found to be negligible. Again, we are ready to have this perception overturned.
Looking at the durability of using each material, we are aware that steel has a drawback already well known (in marine activities): any steel structure immersed in seawater corrodes and requires an anti-corrosion system.
The most common method is galvanic cathodic protection, using a sacrificial anode (zinc or aluminium) that corrodes before the material being protected (essentially ‘taking the hit’).
However, as a promising technology – Impressed Current Cathodic Protection – uses an external power source and reduces the risk of any leakage into the environment.
That still leaves a supply issue for steel: but during our EolMed project, we found that early and supportive engagement with local suppliers resolved any doubts that we could source steel locally at a viable price. We worked with a joint venture between a local producer of steel sheets and a foundation fabrication company, keeping us to our 100% local ambition.
The legacy we are leaving in the South of France goes beyond supporting local steel production and fabrication, we are also working with another TWP founder company DEME under the SEMOP public-private partnership to lead operational development of the local port (Port-La Nouvelle) as a hub for heavyweight operations in the offshore renewables sector.
Innovation gaps in floating wind
This brings me to the question of innovation in floating wind and the burning issues that still need resolution from a developer’s point of view.
1. Lack of standardization
Floating wind is an area of active R&D, which is what makes it exciting from an engineer’s and a technology developer’s perspective. It also means that we have a great number of options on the table – few of them tried and tested. If the industry can come together to agree some standardized models, we will start to see costs reduce, which would greatly accelerate floating wind.
2. Structural compliance between turbines and floaters
The turbines on the market are primarily designed to be installed on fixed-foundations and are not structurally compatible with floating foundations (in terms of natural frequency couplings). Much like when you flick a plastic ruler and it reverberates, wind turbine towers reverberate in tune with their powerful rotors. When you place them upon a floating foundation, you create a higher frequency that is much more difficult to tackle than for a turbine fixed to the seabed. Solutions that can meet that challenge will be preferred.
3. Ever-growing turbines
The major achievement of offshore wind – the constant increase in the size of turbines – is also a spanner in the works when trying to plan. Where will we be in terms of size in 2029? Foundation developers and fabricators need to understand this as early as possible.
4. Dynamic cable resistance
The industry has not yet achieved a satisfactory way of predicting the behavior of dynamic cables out at sea. There is an intricate web of measurements we need to know – how will the cable move in a certain type of current? How will it withstand different types of forces? This is an area of active R&D that we will be watching closely.
What next?
For TWP’s Orkney wind farm, we are back to the beginning of the process once again. While we have taken learnings from Eolmed, we are determined to leverage upcoming technology developments for the Orkney site. Our team is currently assessing the entire spectrum of floating foundations that are out there – from next year, we will start whittling them down to a few favored options (that meet a satisfactory level of maturity and meet the conditions of our site).
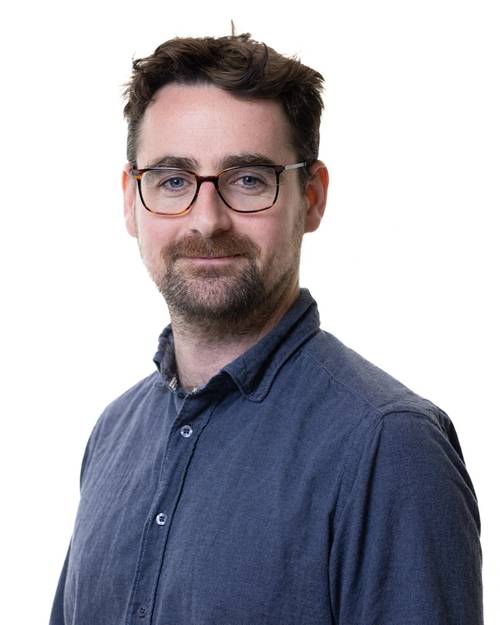
About the Author:
Johan Daelman has been part of the TWP team since the beginning of the Scotwind adventure back in 2019. He now leads the engineering of the floating foundations for NE2 (Orkney).
With a double Master's Degree in mechanical engineering from ENSTA Bretagne (France) and the Technical University of Prague (Czech Republic), he started his career in 2015, working on the development of an automotive electric motor; first, as a calibration engineer (in Germany), then as a software engineer (in Belgium), and finally as an R&D project engineer in Paris.