Subsea Cables
Fiber Optic Cable Systems
Subsea Fiber Optic Cable Systems for Offshore Energy Projects: Q&A with Pioneer Consulting’s Austin Shields.
Pioneer Consulting, a subsea fiber optic telecommunications consulting and project management company, was last year awarded a contract by Zemax-Planova Consortium to provide expertise related to the Petrobras Malha Óptica fiber optic system project, offshore Brazil. The project will link 13 FPSOs and one platform with two cable landing stations in Praia Grande, São Paulo, and Rio de Janeiro. Offshore Engineer has recently interviewed Pioneer Consulting’s Director of Client Solutions, Austin Shields, to learn more about the project and the subsea fiber cable trends in offshore energy in general.
OE: Thank you for taking the time to speak with us today. Could you introduce Pioneer Consulting to our readers and provide an overview of the company and the services it offers within the offshore energy sector?
Pioneer Consulting is an international telecommunications consulting, engineering, and market research company that advises clients on the planning and implementation of submarine fiber optic cable networks during all phases of system development. Our accurate, insightful, and thorough advisory services provide clients with objective and independent guidance in support of their projects and strategic goals. Pioneer’s capabilities range from market analysis and feasibility study to system design and engineering and supply, in addition to providing full-scale project implementation and management.
Within the offshore energy sector, Pioneer offers all consulting services applicable to other telecommunication projects, while leveraging over 20 years of experience in navigating the complexities of the oil and gas and offshore energy sectors. Pioneer provides clients with the project knowledge and planning they need. This is accomplished through deep understanding of the nuances related to the special products and rigorous requirements that are associated with offshore energy projects, which often include strict offshore asset restrictions, health and safety specifications, special powering and optical design principles, and the unique subsea equipment designed specifically for these types of projects.
OE: What are some interesting trends and practices you are seeing today when it comes to the adoption of subsea fiber optic cable technology in the offshore energy industry?
Recent trends in modern fiber optic communication systems point towards a growing need for robustness and reliability. Current systems are being designed and manufactured with redundancies in mind, both with respect to transmission paths (i.e. mesh networks) and at the component level. Not surprisingly, the main goal of any fiber optic communication system is to facilitate reliable communications, however, owners have been pushing for networks that also increase safety, automation, and monitoring -- specifically in the oil and gas sector. Expanding the usage of these networks on different fronts is also a recent trend in the industry, with suppliers working to provide more than just communication applications for their cable products. Suppliers and purchasers are looking to incorporate additional sensing capabilities into their networks, such as permanent reservoir monitoring and downhole applications to name a few in the oil and gas sector.
OE: Can you talk about the technical aspects of subsea fiber optic cables? How do these cables differ in diameter, capacity, length, material, cost etc.? How is this technology evolving?
Much like standard telecommunication systems, offshore energy cable systems typically consist of a backbone or trunk section that connects major onshore sites to the offshore assets. This backbone cable typically consists of the same type of cable, repeater, and branching unit products found in standard telecommunication projects, which provides the benefit of using off-the-shelf products in place of bespoke, specialized products. Moreover, existing cable protection products such as URADUCT and mattressing are used extensively to protect both the optical cable and the offshore energy assets that the cable crosses.
Beyond the backbone, however, are where the specialized products come into play. In order to facilitate connections to floating production platforms, specially designed umbilical and riser cables are required. These umbilicals are typically large enough to encompass multiple standard subsea telecommunication cables and thus average between 80-120mm or greater in outer diameter, depending on the application. These umbilicals are designed with similar strength steel wire members, and polyurethane and armor layers, compared to the optical cable that they house, and can also support a wider range of applications, including power cable, electrical monitoring, and hydraulic and injection hoses. Umbilicals provide connectivity between subsea assets and offshore assets, such as floating oil platforms, via a specially designed catenary or free-hanging section of cable. This catenary is suspended in the water column using buoyancy and ballast modules affixed to the umbilical cable.
Evolution in optical umbilical products is expected to follow similar design trends as standard optical cable regarding increased fiber count and a potential shift towards cheaper power conducting materials, though not much detail in that regard has been shared lately. As a specialty product, these umbilical cables are often sold a premium and can generally be expected to cost more than commercial subsea cable products.
OE: What are some of the main benefits for oil and gas operators who chose to go the subsea fiber optic cable route?
The main benefit of fiber optic cables for oil and gas applications is the advantage of direct fiber connectivity between onshore sites and offshore facilities and assets. Having direct, high-capacity traffic connectivity to floating oil platforms provides all the benefits of reliable communication that any standard telecommunication system would likewise provide. Considering the harsh operating environment and remoteness of these production platforms out in the ocean, a stable and reliable line of communication and data flow are critical.
Additional benefits of fiber optic cables unique to oil and gas include increased automation and controls, along with the ability to process high volumes of data generated through emerging fiber optic technologies such as downhole sensing and permanent reservoirs monitoring. Fiber optic cables also help to create a safer operating environment with a more connected workforce and more flexibility and reliability compared to satellite connections that can be severely impacted by weather and other natural events.
OE: Are there any distinct differences between commercial subsea fiber optic projects and those in the offshore oil and gas industry?
As mentioned previously, the oil and gas industry often presents unique design constraints that require specialized products to overcome. Specific requirements include OADM traffic flexibility to/from multiple offshore production platforms, while simultaneously restricting the use of powered equipment on the cable segments leading to these platforms.
Other differences in oil and gas projects include a particular attention to installation operations and health and safety. It is not uncommon for an entire project to be put on hold due to a crew member on a vessel not wearing the correct PPE, and vessels and their crew often have strict requirements for training and approach protocols when entering the “exclusion zone” surrounding the floating production platforms. Additionally, cable installation operations often have requirements not typically found in commercial subsea fiber optic projects, including live touchdown monitoring and cable protection when crossing pipeline assets, strategic placement of cable between pipeline anodes and electrical constraints, and unique shipboard representative accommodations.
Lastly, a major difference in oil and gas projects comes from the subsea technology products needed to facilitate connectivity to the floating platforms. Since many aspects of oil and gas are dynamic and consist of moveable production facilities, the optical network must be flexible enough to support new connections to offshore assets. The Subsea Umbilical Termination Assembly (SUTA) and other similar products are unique to the oil and gas industry which adopt highly specialized components to allow for such flexibility. SUTAs utilize wet-mate connector technology and advanced fiber termination assemblies to allow for direct connections to be made undersea via an ROV. These SUTAs connect the offshore assets via umbilicals to the fiber optic backbone, allowing for multiple connections to existing and future oil and gas assets without the need to install additional fiber optic backbone cable or recover and splice into pre-installed branching units or OADM units.
OE: You were recently awarded a contract to support Brazilian oil giant Petrobras’ Malha Óptica project. Can you tell us about the project in general and what it aims to achieve?
Currently under construction, the 1,200 km Malha Óptica makes use of a traditional, two-fiber pair (2FP) repeatered trunk and branch architecture with 13 power-switched branching units (PSBU). The network will initially connect 13 floating production and storage offloading (FPSO) units to the trunk via branching units with OADM technology to deliver 200 Gb/s of bi-directional communications to each cable landing stations (CLS) – one located at Praia Grande, state of São Paulo and the other at Praia da Macumba, state of Rio de Janeiro.
Petrobras is highly motivated in increasing capacity and security in the transmission of real-time data from offshore platforms. This increase in capacity opens up a range of possibilities, such as live video support from suppliers via video transmission, adoption of digital technologies on a large scale, and real-time remote monitoring of production facilities.
OE: What exactly is your scope in the project, and what do you believe was the key factor that contributed to the company winning the contract?
Pioneer has been hired by a consortium between ZMAX Blue Marine Telecom and Planova Planejamento e Construções, both Brazilian companies, which is responsible for the integration of the Malha Óptica system. Pioneer has been hired to help bridge the “language” gap between oil and gas and commercial telecoms. Our role in this project is to provide expertise, experience, and advise on all aspects related to oil and gas telecom equipment, marine survey, and installation activities. Since we started working on the project in April 2022, we have taken on an active role coordinating various subcontractors, providing our expertise in installation planning and procedures, supporting on-site factory acceptance testing, and assisting with other roles as needed to help move the project forward.
We believe that there were a few key factors that contributed to our winning the contract. Our general knowledge of the project based on years of planning by Petrobras, coupled with decades of installation and planning experience in oil and gas were likely distinguishing factors. We also had more general experience working in Brazil on telecom projects through the past two decades.
OE: It's now been several months since the contract was awarded. Can you give us an update on the status of the project?
As of January 2023, the entirety of the trunk cable, repeaters, branching units, and branch cable has been manufactured, with system assembly and test (SAT) ongoing.
Manufacture and integration of the SUTAs and umbilicals will be completed during the second quarter of 2023, the same as installation begins for the trunk.
The 13 initial FPSO umbilical connections are scheduled to occur throughout 2023, and the entire Malha Óptica is on schedule to be completed by late 2023.
OE: What makes the Malha Óptica project unique compared to other subsea telecom projects Pioneer Consulting has worked on?
In addition to the various nuances described above, Malha Óptica is unique in its somewhat “disaggregated” approach to design and implementation.
Many aspects of this project are being handled by separate manufacturers and installers, each with expertise relative to the oil and gas sector. The ZMAX-Planova consortium is acting as the integrator, pulling all of this expertise together to deliver a completed network for Petrobras.
Of course, this approach creates unique challenges in the coordination of materials, equipment, and subcomponents between suppliers and installers.
Although Pioneer is very familiar with a disaggregated approach to system construction for commercial telecom systems (for example having just completed the CrossChannel Fibre system using this approach), this level of disaggregation is unique because the disaggregated scopes are much larger than they would be for a commercial system.
Of course, this approach is quite common in the oil and gas industry, but not so much in commercial telecoms, at least at this scale.
OE: Finally, are there any drawbacks to using subsea fiber optic cables in the offshore industry? How is the cable's structural integrity, cybersecurity, and data safety ensured? And what can operators expect in terms of maintenance costs?"
Drawbacks to using fiber optic cables in the oil and gas industry are similar to the drawbacks of using fiber optics for commercial use, which include challenges in installation and repair operations, potential issues in permitting and regulatory hurdles, and the high cost of developing these types of systems. The oil and gas industry introduces additional challenges during installation, and repair operations due to the restrictions associated with nearby offshore energy assets, and, occasionally, the need for specialty equipment can drive up the development costs.
Cable structural integrity is ensured through typical cable protection requirements, which are aligned with the International Cable Protection Committee’s (ICPC) recommendations.
Cable structural integrity is ensured through typical cable protection requirements, which are aligned with the International Cable Protection Committee’s (ICPC) recommendations.
Leveraging existing transmission equipment, and network management services, the offshore energy sector sees all the same benefits in cybersecurity and data safety as the commercial sector. One unique aspect of these types of oil and gas networks is that they are generally private. Malha Óptica will be 100% owned by Petrobras, so they’re able to decide if and how the data may be connected outside to public networks. At that point, security is the same as any other communications system.
Regarding maintenance costs, offshore operators experience similar costs as commercial operators. There is no difference in terms of ongoing operational costs. However, depending on proximity to offshore assets, if cable repairs are required, they may require more precise and specialized operations compared with commercial telecom systems.
This is to ensure the integrity of the abundant infrastructure deployed on the seabed. But, as mentioned earlier, what might be seen as a more challenging operation for the commercial telecom industry is seen as “business as usual” in the offshore oil and gas industry.
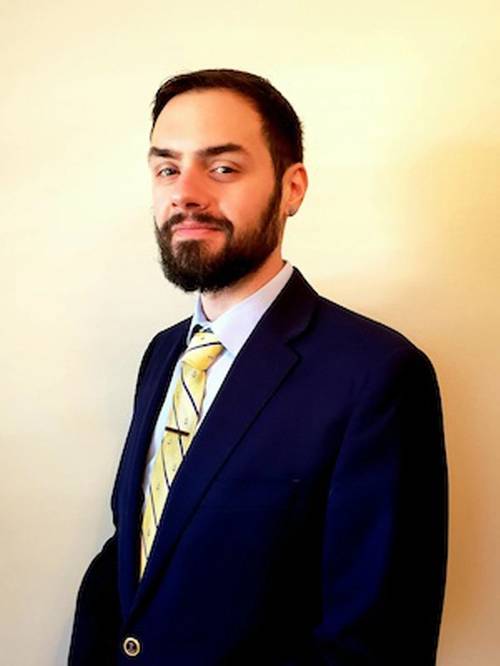
Austin Shields’ Biography
As Director of Client Solutions at Pioneer Consulting, Austin Shields has 8 years’ of submarine cable experience in both mechanical and electrical engineering. With a background ranging from network design and architecture, testing and verification, design, manufacturing, and qualification, to full-scale project management of undersea fiber optic cable systems, Shields brings a wealth of experience to clients. Shields holds a Master of Science in Electrical Engineering (Signal Processing) from New Jersey Institute of Technology, Bachelor of Science in Mechanical Engineering from Rutgers University, School of Engineering and Bachelor of Science in Applied Physics from Stockton University.