Technology
ROVs
ROVs – Innovation Enablers
By Rhonda Moniz
Seatools completed Factory Acceptance Tests (FAT) for a Fall Pipe ROV developed for DEME, to be deployed on DEME's upcoming subsea rock installation vessel Yellowstone, scheduled to join the fleet in the first half of 2024.
Image courtesy SeatoolsThe world beneath the ocean's surface remains one of the last frontiers of exploration, where the mysteries of the deep beckon to be uncovered. In this realm, Remotely Operated Vehicles (ROVs) are indispensable pioneers, venturing into the abyss to conduct critical tasks in industries ranging from offshore oil and gas to marine research and underwater construction. Work class ROVs and other ROVs differ primarily in their capabilities, design, and intended applications. They are a class of remotely operated vehicles designed for heavy-duty tasks in demanding underwater environments. They are larger, more robust, and capable of performing complex operations at significant depths, making them essential tools in various industries. As technology advances, work class ROVs experience significant trends and innovations. The work class ROV market is dynamic, characterized by continuous innovation and adaptation to industry needs. Several notable trends are shaping the work class landscape.
-
Advancements in Automation and Autonomy: Autonomous and semi-autonomous work class ROV technology has developed significantly in recent years. These systems have advanced computer vision, machine learning, and artificial intelligence (AI) capabilities, allowing them to perform tasks more autonomously. Automation reduces the workload on human operators and improves efficiency and safety.
-
Enhanced Maneuverability and Versatility: Work class ROVs are becoming more agile and versatile. Innovations in thruster technology and control systems enable them to navigate complex underwater environments, making them well-suited for a wider range of tasks. Enhanced maneuverability is particularly valuable in confined spaces and subsea infrastructure inspections.
-
Data-Driven Insights: Data is king in the modern world, and work class ROVs are no exception. These vehicles have advanced sensors, cameras, and imaging systems that capture real-time high-resolution data. This data is invaluable for immediate decision-making during operations and post-mission analysis, predictive maintenance, and trend analysis.
-
Compact and Portable Solutions: While traditional work class ROVs are often large and require dedicated launch and recovery systems, there is a growing trend toward developing compact and portable work class ROVs. These systems are easier to transport, deploy, and operate, making them suitable for a broader range of applications and reducing overall costs.
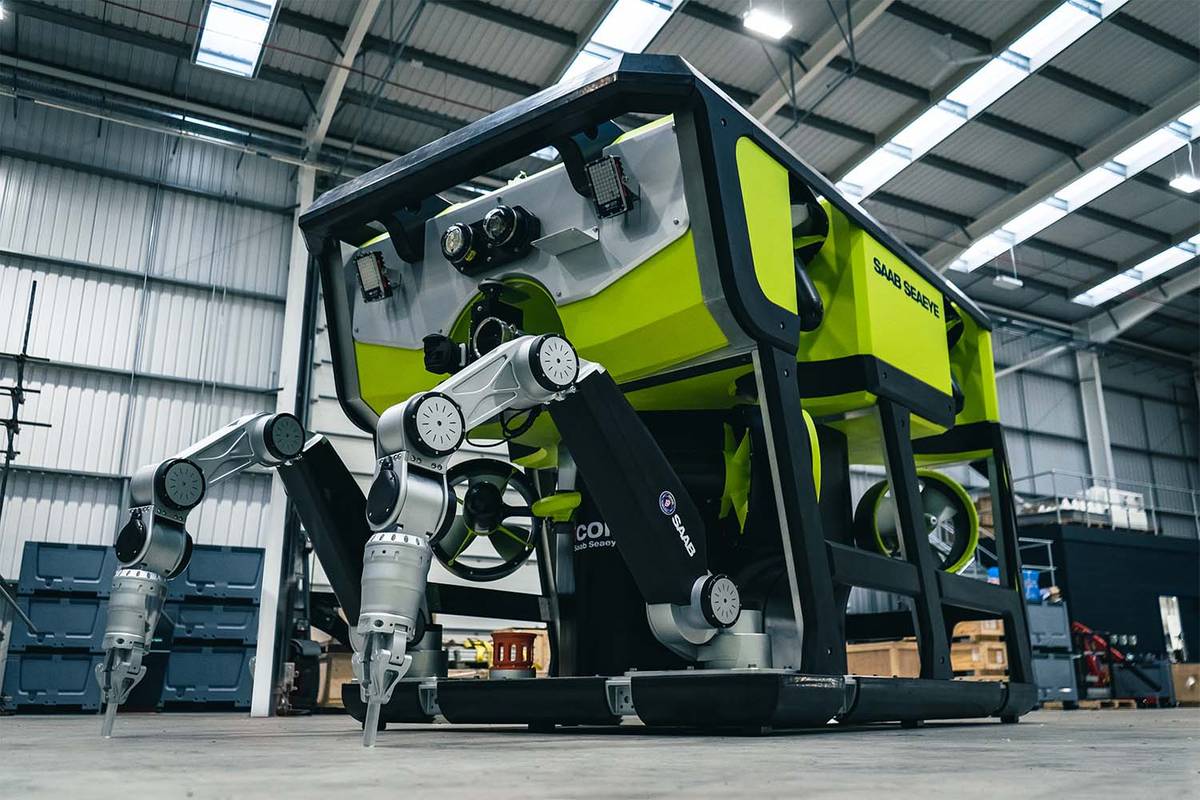
The Future of Work Class ROVs: Navigating Uncharted Waters
As work class ROVs continue to evolve, several emerging trends offer a glimpse into the future of underwater operations:
-
Deep Sea Exploration: Work class ROVs will continue to play a pivotal role in exploring the Earth's most remote and extreme environments, including the deepest parts of the ocean, venturing into uncharted territories, and discovering new species and geological phenomena.
-
Renewable Energy: With the growth of offshore wind and tidal energy projects, work class ROVs will be instrumental in the installation, maintenance, and repair of renewable energy infrastructure.
-
Advanced Materials and Durability: Future work class ROVs will likely incorporate innovative materials and construction techniques to enhance durability and longevity, enabling longer missions at greater depths.
-
Artificial Intelligence and Analytics: AI-driven analytics will become more sophisticated, allowing ROVs to process and analyze vast amounts of data. Autonomous navigation and operation using AI algorithms will enable ROVs to navigate autonomously, while AI-driven navigation systems will help with obstacle avoidance, enabling the ROV to follow pre-defined transects and mission parameters while adapting to changing conditions.
AI will also improve imaging and data analysis using machine learning algorithms to process and analyze images and sensor data in real time, helping pilots and scientists make informed decisions during missions. Data transmissions from the ROV to the surface can be optimized by prioritizing and compressing the most relevant data for faster and more efficient communication. AI will also assist in predictive maintenance when ROV components may require maintenance or replacement based on historical performance, minimizing downtime and reducing maintenance costs. AI will revolutionize ROV technology by enhancing their autonomy, data processing capabilities, and efficiency. These advancements will enable ROVs to perform a wider range of tasks in underwater environments more effectively while reducing risks to human operators.
As AI advances, the potential for ROVs to contribute to scientific research, industry, and environmental monitoring in marine and aquatic ecosystems will only increase. Overall, the convergence of technological breakthroughs, scientific curiosity, environmental concerns, and economic opportunities is making this an incredibly exciting time in subsea technology. As we continue to push the boundaries of what is possible in underwater exploration and operations, the potential for new discoveries and innovations is virtually limitless, and the impact on various industries and our understanding of the underwater world is profound.
Updates on the Latest Vehicles and Capabilities
SEAMOR and Voyis have partnered together to combine the SEAMOR Mako ROV with Voyis’ Discovery Stereo Camera, transforming the applications and abilities of both and reimagining what can be done in underwater inspection and exploration. The portable Mako ROV is rated up to 600 meters and can be remotely operated on umbilical lengths of up to 950 meters. Its size and build make it ideal for pipe inspection, aquaculture, port security monitoring and various marine research operations. Likewise, the Voyis Discovery Stereo Camera is a widely applicable piece of technology offering high level clarity and precision in visual captures of underwater environments and immediate creation of real-time 3D models. The integration of both opens up unparalleled capacities in aquaculture management and hydroelectric applications, offering an efficient, cost-effective and reliable house for the stunning visual capturing capabilities of the Voyis Camera. Applications that look to be significantly improved in the ease and accuracy of data collection and monitoring include routine net inspections, equipment recovery, and surveying and sampling of the seabed.
Seatools’ new Fall Pipe ROV, the Yellowstone PLC, introduces unique and innovative features that offer high levels of precision in navigation and movement, advanced data collection and processing, and efficient workability and task execution. Featuring an integrated rotator which allows for the offsetting of the ROV’s heading relative to vessel heading, the Yellowstone can save significant power compared to conventional Fall Pipe ROVs and offer vastly enhanced workability or rock installation operations. The vehicle has an expansive on-board survey equipment suite developed for optimal positioning and operations management, as well as for prime ability to monitor the environment and conduct pre- and post-surveys with Seatools’ specially developed multicore processing technology.
Some companies have recognized the strong potential for autonomy optimization in the recent advancements in AI technology, and this includes underwater robotics company QYSea Technology and their newly modular, AI-powered advanced imaging and observational marine robot, the FIFISH E-GO. The E-GO offers a range of advanced capabilities not often seen in the subsea tech market. With a detachable motor, lighting, camera, and battery, module replacements can easily and quickly restore operability. This feature also allows for extensive expansion and customization of components. The E-GO has integrated AI into almost all operational aspects of their vehicle. With AI Vision Lock, it has high-level adaptive stabilization and can lock onto target objects with ease. Its plankton filtering algorithm is also AI bolstered, automatically optimizing visuals, monitoring tasks across aquaculture, search and rescue, hull check-ups and more, and even its laser scaling and measurement systems use AI automation for increased accuracy and the ability to identify damage in underwater structures. The FIFISH E-Go is QYSea’s most powerful professional-class underwater robot and is now available across all QYSea platforms.
Latest innovation from Copenhagen Subsea is the enhanced Gorilla ROV, now equipped with an advanced 3D camera system. By integrating a 3D camera from Danish UVision, we have unlocked a new level of subsea exploration and inspection capabilities. With this cutting-edge technology, the Gorilla ROV now has the ability to capture highly accurate and detailed 3D scans of underwater environments. The 3D camera, mounted on the Gorilla, enables the creation of precise 3D models, providing invaluable insights for various applications. The 3D camera delivers exceptional image quality and resolution. Its advanced scanning capabilities allow for rapid data acquisition and precise measurements, ensuring accuracy in subsea mapping and inspection tasks. With the Gorilla ROV and its integrated 3D camera, subsea operators can now visualize underwater structures, assess damages, and plan interventions with greater precision than ever before.
Seatools completed Factory Acceptance Tests (FAT) for a Fall Pipe ROV developed for DEME, to be deployed on DEME's upcoming subsea rock installation vessel Yellowstone, scheduled to join the fleet in the first half of 2024.
The new Fall Pipe ROV introduces several unique features, including the integrated rotator, allowing for the offsetting of the ROV's heading relative to the vessel heading. This helps to ensure an optimal vessel heading, enhancing the workability level of rock installation operations while saving significant power compared to conventional Fall Pipe ROVs.
Another feature of the ROV is its expansive on-board survey equipment suite, employed for precise ROV positioning, monitoring operations and the environment, as well as conducting comprehensive pre- and post-surveys. To handle the vast amounts of data and complex control algorithms related to dynamic positioning, the ROV is equipped with Seatools' in-house developed multicore processing technology. The Yellowstone ROV PLC, featuring a quad-core processor, efficiently distributes tasks among individual cores, resulting in improved control task execution, particularly beneficial in complex control loops like electro-hydraulically driven dynamic positioning (DP) systems
SMD has been developing work-class ROVs for more than three decades. In 2023, the company’s latest products were the electric Quantum EV and Atom EV ROVs, which are more compact than previous generations, help reduce CO2 emissions, and can even operate autonomously when equipped properly. According to SMD, Quantum EV is a 270hp heavy construction vehicle with a high payload and powerful thrust output. Atom EV is a 130hp light construction vehicle suited to shallow-water, high-current work in offshore renewables. The ROVs feature a new DC power transmission system that is said to be far more efficient and environmentally friendly than previous generations. Further, the ROVs employ advanced flight control computers to help complete operations faster and maintain control in arduous conditions, such as high currents, SMD explains. The flight control system can also link to other SMART systems unlocking autonomous functionality. They use unique electric propulsion technology that offers extreme performance in fast-moving water, but not at the expense of fine control. “All this adds up to a range that can work where current generation vehicles can’t, that opens up the operating weather window and delivers higher quality results. All while being more environmentally friendly,” SMD says. Looking to the future of work class ROVs, SMD shared, “Work class ROVs are a multipurpose tool. And as with any tool there is always a focus on how well it does the job, its reliability, and its dependability. But the offshore energy mix is changing. And we are also seeing changes to the way people work (and go to sea) with much more emphasis on work-life balance and the environment. So, the robotic tools that construct and maintain energy infrastructure need to evolve. In the future, the tools we today call work class ROVs will need to be suitable for uncrewed vessel and resident work; we may see less cabled connections to the surface and onboard power systems; we will probably see AI start performing tasks, with a move from person in loop to person on loop-command to control. It will be easier and faster to undertake tasks and see the results, with real-time information at the fingertips of stakeholders anywhere in the world.”
About the Author
Rhonda J. Moniz is a highly accomplished and renowned underwater forensics expert specializing in diving technologies and subsea systems. She has more than 25 years of experience as a remotely operated vehicle pilot, master dive instructor, scientific diver, and dive safety officer. She is the president of the board of directors for the Northeastern Regional Association of Coastal Ocean Observing Systems (NERACOOS). She is on the U. S. Integrated Ocean Observing System (IOOS) board of directors.