Green Hydrogen
Electrolyzers
Electrolyzers Tech Ramps Up to Meet Green Hydrogen Demands
Electrolyzer technology is going to have to get cheaper and more scalable if it is going to enable a global green hydrogen economy.
By Wendy Laursen
Somewhere on a benchtop in Brimsdown, London, there is a lab-scale prototype that can extract the platinum and polymers from PEM electrolyzer membranes so they can be recycled into new membranes.
Why? To reduce the cost of electrolyzers and therefore green hydrogen. Electrolyzers use electricity to split water into hydrogen and oxygen, and to meet global expectations for 2030 and then 2050, they must produce green hydrogen cheaper than hydrocarbon-based methods. They must also be able to do this at scale.
Electricity makes up most of the production cost of green hydrogen, and researchers around the world are trying to reduce that, but Johnson Matthey’s benchtop unit is also representative of the fact that, despite new electrolyzer technologies well past lab-scale testing, there will still be a major role played by more established technologies such as PEM and alkaline electrolyzers.
Current technologies can be roughly categorized into two main groups: those suitable for use with intermittent renewable energy like PEM, pressurized alkaline and anion exchange membrane (AEM) and those suited to grid power or being incorporated into industrial plant like atmospheric alkaline and solid oxide electrolysis (SOE).
SOE is a growing technology that can also operate in reverse to act as a fuel cell, and AEM, a development of the PEM concept but with cheaper materials, is an emerging technology. While alkaline electrolyzers use a liquid electrolyte, and PEM electrolyzers use a polymer electrolyte, SOE use a solid-state ceramic electrolyte and requires heat to operate. But new variations on existing themes continue to emerge as the industry tackles cost and scalability challenges, and each have different materials, chemistries and heat and pressure requirements.
Using solar and wind energy, green hydrogen can be produced at peak times by running electrolyzers and then storing the hydrogen for later. “Here, there’s an important role to play for green hydrogen which can operate at a different scale to batteries to balance out fluctuations in the supply of, and demand for, renewable energy production,” says Synne Myhre Jensen, Public Affairs Advisor at Norwegian hydrogen company Hystar. As part of the company’s HyPilot project, collaborator Equinor is planning to demonstrate dynamic hydrogen production tailored to the variable output typically found in offshore wind applications.
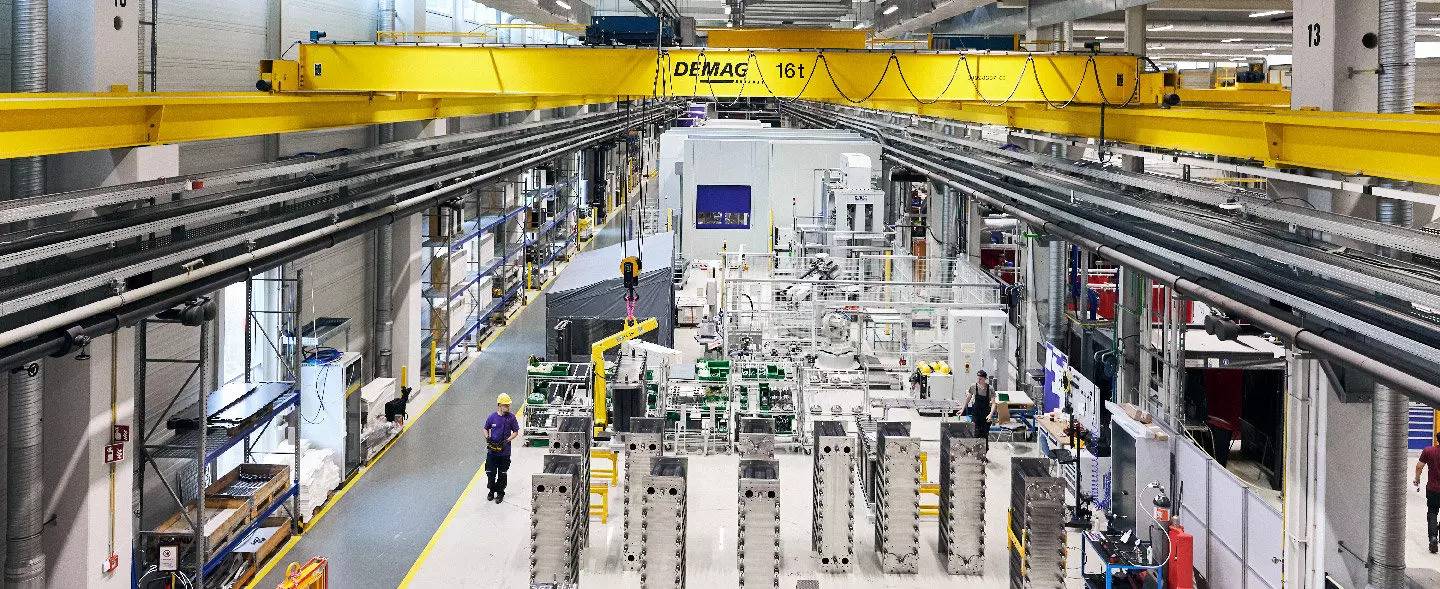
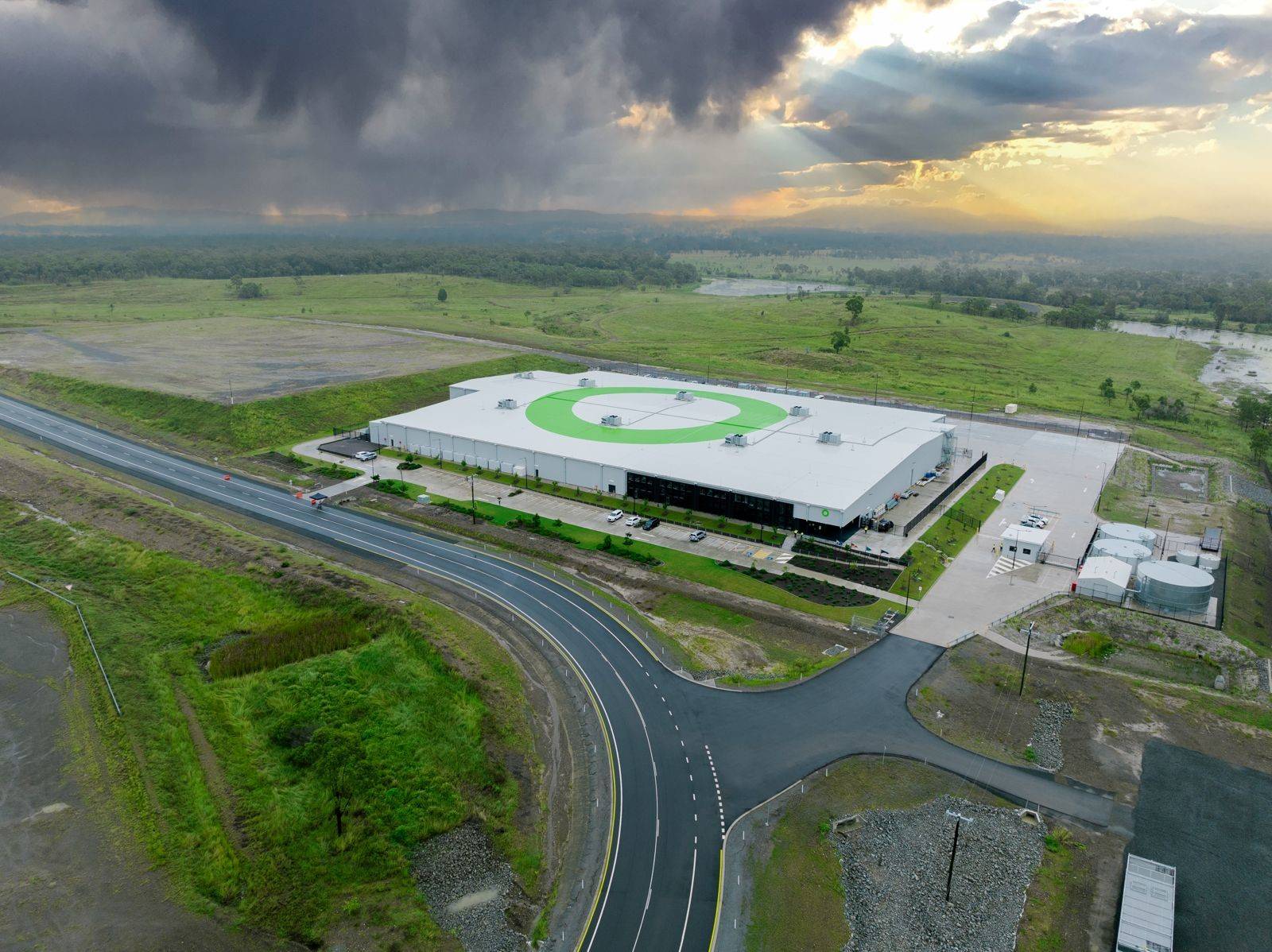
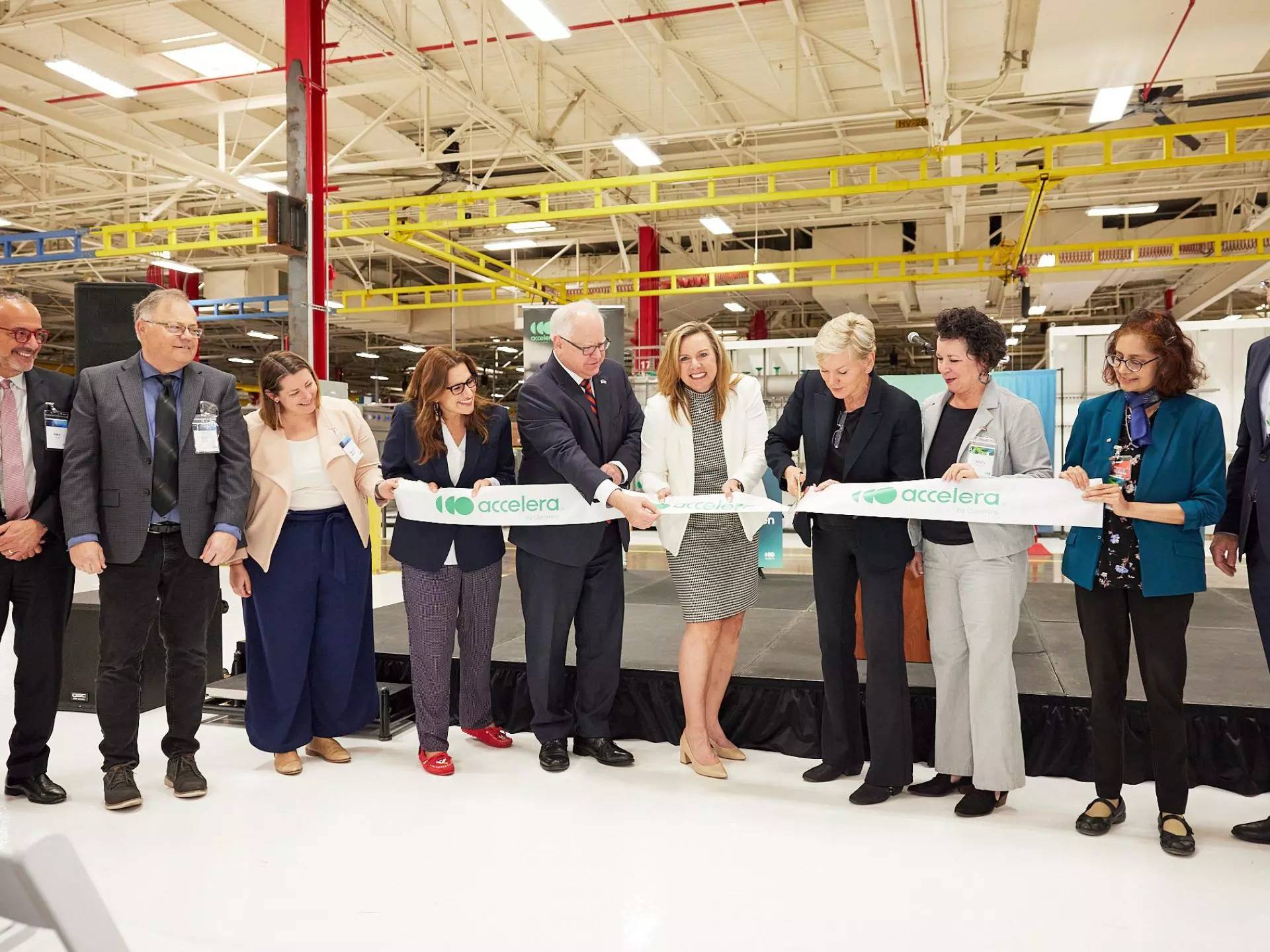
Johnson Matthey will supply membrane electrode assemblies for Hystar’s patented PEM technology. “Each of our stacks can produce two to three times more hydrogen than a conventional stack, enabling more hydrogen production at peak production times and capitalizing upon lower electricity prices,” says Jensen. “During these moments, the exact energy consumption is not important, as the electricity price is low anyway. It is then a matter of how much hydrogen you can produce by fully utilizing the renewable sources available.” The technology is also more compact and safer than traditional PEM electrolyzers due to built-in air circulation to prevent combustion, she says.
Another project, the EU-Funded HYScale project, aims to upscale an efficient, durable, sustainable, and cost-effective AEM electrolyzer technology. Project partner CENmat claims to have re-engineered electrolysis from scratch to produce a system that operates with catalysts and electrodes free of critical raw materials and anion exchange membranes free of forever chemicals.
Australia’s research organization CSIRO is developing both PEM and SOE technology. Its high-efficiency tubular SOE technology uses a series of sintered ceramic tubes and easily obtainable metals and can efficiently produce hydrogen and syngas (a mixture of hydrogen and carbon monoxide) – something that distinguishes it from existing PEM and alkaline technologies. It is also highly scalable.
“There is a limit to what extent efficiency of electrolyzers can be further improved,” says Dr Sarb Giddey, Senior Principal Research Scientist and Group Leader at CSIRO. “The efficiency will stay in the 70-75% range maximum due to the thermodynamic limits and the losses related to balance of plant. The electrolyzer cost, electricity costs, and scale are still the major challenges for the large-scale adoption of hydrogen production via electrolysis for decarbonization of various energy sectors.”
While SOE technology holds promise for power-to-X applications, it has a limited lifetime and its dynamic capabilities are currently a barrier to large-scale commercialization, so Denmark’s Dynelectro has developed a novel SOE technology that uses a mix of alternating and direct current and can accommodate fluctuating green power and temperature variations. This is expected to increase the lifetime of SOE stacks from two to 10 years.
The scale-up of well-established technology is already underway. Accelera is developing 25MW PEM electrolyzer modules suitable for larger electrolyzer projects (>200MW). The systems will be manufactured in its new US facility and also at another new plant in Spain.
Manufacturing speed is also increasing. Air Liquide and Siemens Energy officially inaugurated their joint venture gigawatt PEM electrolyzer factory in Berlin last year. The factory leverages robotics for series production, as does Fortescue’s new PEM factory in Australia.
As a result of all the development underway, DNV predicts that electrolyzer costs will drop 25% by 2030 and 50% by 2050. Another prediction is that electrolyzer capex will drop and the market will consolidate mid-term, especially for large-scale electrolyzers. This could lead to supply chain optimization that could further reduce production costs.
But where? China could disrupt the industry and take the same commanding market share it has in other industries despite the US pumping money into the industry (Nel and its partners received around $90 million from the Department of Energy for seven electrolyzer projects in March).
While much of China’s electrolyzer production is currently satisfying the domestic market, that is likely to change. Bright-H Technology recently claimed industry leading energy efficiency for its alkaline technology, and Sungrow Hydrogen says its latest electrolyzer not only breaks the record of hourly hydrogen yield per PEM stack in the Chinese domestic market but also catches up with advanced international technologies in a number of key indicators.
So, the future of electrolyzers may well be found on a test bench in Hefei.