New Technologies
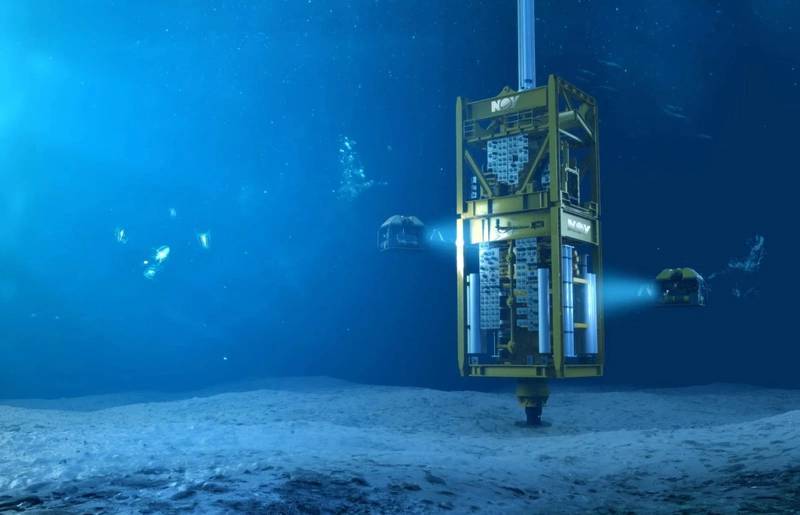
Shell, NOV Help Equip Stena Evolution
Stena Drilling’s Stena drillship is set to undergo a significant equipment upgrade with the systems supplied by Shell and NOV, which will make it capable of drilling and completing wells requiring 20,000 psi (20K) pressure control.
The upgrade includes the installation of cutting-edge drilling equipment and technology aboard Stena Evolution, starting from 2026.
Stena Drilling, together with equipment supplier NOV, and Shell, will install the 20K Subsea blow-out preventer (BOP) and other key equipment aboard its state-of-the-art 7th generation drillship, which was delivered to the offshore drilling contractor by Samsung Heavy Industries after a decade in the making,
A BOP is a large, high-pressure safety valve used to prevent the uncontrolled flow of liquids and gases during well drilling operations. Pressure control is a critical part of the drilling process, and, as a fail-safe component, a blowout preventer is essential to the safety of the rig.
When the new 20K equipment package is installed, the Stena Evolution will be able to perform completion operations in the Sparta field on behalf of Shell in the U.S. Gulf of Mexico, enabling the drilling in previously inaccessible reservoirs for Stena Drilling’s clients.
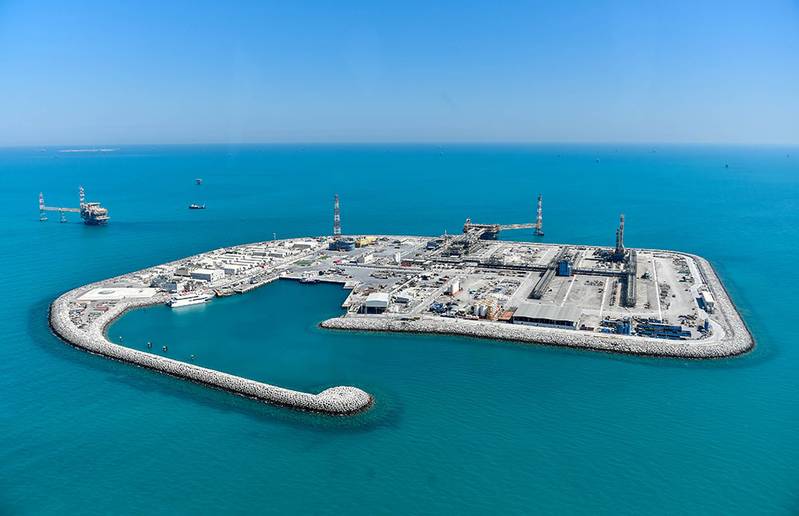
AI Boosts Offshore Oil Field Production
The implementation of Artificial Intelligence (AI)-enabled digital operations at offshore oil fields can significantly increase their production and at the same lower their carbon footprint, with the most recent achievement made by Abu Dhabi National Oil Company (ADNOC) which boosted the production at one of its Middle Eastern fields by 25%.
The technologies that deployed at ADNOC’s SARB field, which marked the significant rise in its production to a total of 140,000 barrels per day (bpd), include tools developed by AIQ, the Abu Dhabi-based AI champion delivering transformative solutions to the energy sector.
AIQ solutions DrillRep and OptiDrill process data from rigs and wells at the field, enhancing drilling efficiency and optimization.
By utilizing daily drilling data reports and rig sensor data, AIQ’s technology supports drilling operations with the necessary insights and actions to optimize the drilling process.
DrillRep is a web-based application that automatically analyzes the written description of drilling activities, and suggests code and sub-code allocations, based on analysis of accurate historical DDR data, which drives greater operational efficiencies.
OptiDrill on the other hand is designed to validate key data against proven quality-control processes, using powerful data integration and management tools to analyze the data from an entire drilling operation.
Requiring just one-time configuration to stream data from surface sensors to monitor drilling processes, OptiDrill reduces the gap between how actual procedures occur as compared to best practices in the given activity using micro-KPIs and real-time alerts.
Located 120 kilometers northwest of Abu Dhabi, the digital solutions implemented onsite at SARB allow the field to be operated remotely from Zirku island, 20 km away.
Remote monitoring, smart well operations and production management technologies are integrated at the remote control center for optimized real-time decision-making.
This has enabled the accelerated growth in field capacity with reduced costs and emissions. The field’s digitalization will enable the deployment of additional AI solutions to further enhance and optimize operations, according to ADNOC.
Equinor, SLB: Autonomous Drilling Reaches New Depths
A major step towards fully autonomous drilling operations has been achieved as Equinor and SLB set the record for the most autonomous well section drilled to-date offshore Brazil, leveraging SLB’s digital technologies for surface automation, autonomous on-bottom drilling, and directional drilling.
The combination of SLB’s technologies enabled 99% of a 2.6-kilometer section to be drilled in autonomous control mode. Over a five-well program, a 60% increase in rate of penetration was achieved, resulting in faster well delivery while reducing cost and carbon emissions.
Multidisciplinary experts collaborated to design and implement interconnected autonomous workflows, enabling the system to seamlessly drill the section.
On the rig floor, manual pipe handling and equipment sequencing tasks were automated with DrillPilot software.
On-bottom drilling performance was maximized using AI-driven technology in the DrillOps automation solution.
Neuro autonomous solutions determined the optimum trajectory and delivered the well plan, adjusting steering sequences and drilling parameters to reach the target as designed by the DrillPlan coherent well construction planning solution.
The DrillOps and DrillPlan solutions are SLB’s cloud-based applications on the Delfi digital platform. The platform combines apps, artificial intelligence (AI), physics-based science and free-flowing data to accelerate and improve exploration, development, drilling, production, and new energy operations.
With more than 30 engineering algorithms working simultaneously in the cloud and enabling a collaborative environment, the DrillPlan well construction planning produced drilling program, automatically calculating hydraulics, casing design, torque and drag, well integrity and more.
The autonomous drilling milestone was achieved at Equinor's Peregrino C platform, which produced its first oil on October 10, 2022 as part of Peregrino phase 2.
Peregrino phase 2 will extend the life of the Peregrino field to 2040, adding 250–300 million barrels of oil, while at the same time halving expected CO2 emissions per barrel over the field remaining lifetime.
Managed Pressure Drilling Systems
The integration of Managed Pressure Drilling (MPD) systems into drillships represents a significant advancement in offshore drilling technology, improving safety and efficiency of drilling operations, as confirmed Diamond Offshore which is installing the system on its Blackships fleet of drillships.
Over the course of the last year and a half, Diamond Offshore has been increasingly implementing MPD systems across its fleet of drillship, and has already achieved significant improvements when it comes to the efficiency of its operations.
Namely, four of its drillships have successfully drilled wells with a remarkably narrow 0.2ppg drilling window - a staggering 86% reduction compared to conventional methods, according to the company.
MPD systems on drillships are advanced technologies designed to precisely control the annular pressure profile throughout the wellbore during drilling operations. MPD is especially important in offshore environments, where wellbore stability and control over formation pressures are critical to avoid issues like well kicks, blowouts, and non-productive time. By enabling better control over drilling conditions, these systems improve safety, reduce operational risks, and allow drillships to operate in deeper and more complex reservoirs. According to Diamond Offshore, the MPD system allows it to compete for the highest day rates in the 7th-generation drillship market.
The company plans to complete the MPD upgrades on its drillships by the end of 2024.
Petrobras, GA Drilling: Next-Gen Downhole Drilling System
Slovakian drilling specialist GA Drilling has teamed up with Brazil’s state-owned oil and gas giant Petrobras to deliver more efficient deep drilling system, in an effort to reduce well construction costs and risks in challenging drilling applications.
The partnership pairs Petrobras with GA Drilling’s technology, a downhole anchoring and drive system that will form the cornerstone of an advanced autonomous reeled drilling system.
The collaboration aims to enable deep and complex offshore wells to be drilled from a light well intervention vessel rather than a more costly semi-sub or drillship, saving 30% of well construction cost.
GA Drilling’s novel system significantly improves drilling efficiency and enables the replacement of conventional drill pipe with reeled continuous tubing, thus minimizing pipe handling hazards, tripping times, and well control risk, the company claims.
The new technology includes sophisticated drilling automation and control systems and real-time wireline communications to the surface that optimizes and drives the drilling process downhole at the rock face rather than many thousands of feet above.
Wellube Debuts Double Isolation Pipeline Stopper Tech
Wellube launched the Double Isolation Pipeline Stopper (DIPS). This solution, developed in-house by the Wellube Research and Development team, marks a significant advancement in pipeline intervention and safety management.
The Double Isolation Pipeline Stopper (DIPS) provides a fail-safe isolation using a single size-on-size hot tap intervention, eliminating the need for additional tapping for bleed and vent ports. This approach reduces risks and enhances safety, making it ideal for use in critical and harsh environments.
Wellube’s DIPS technology is third-party approved and is designed to reduce the risk to both asset and operator in highly volatile operational situations, ensuring it meets the highest performance standards trusted by clients globally.