Subsea Robotics
UUVs, AUVs, ROVs
Robotics Drive Offshore Efficiencies
For subsea inspection, maintenance and intervention, robotics solutions are increasingly brought to the fore in the name of efficiency and safety.
By Amir Garanović, Managing Editor at Offshore Engineer
Oceaneering solidified its position as one of the leaders in AUV tech with significant projects in 2024. One of the key highlights includes its collaboration with TotalEnergies, where Oceaneering’s advanced hybrid AUV/ROV system was deployed for subsea inspection and monitoring tasks. Late in May 2024, Oceaneering’s Freedom AUV concluded the pipeline inspection industrial pilot project in the North Sea, which covered an inspection of over 120 km of subsea pipelines, resulting in a reduction in time, and emissions, of an estimated 50% compared to existing methods with equivalent quality of the inspection, according to the companies.
The Freedom AUV design incorporates a multi-thruster design which provides six degrees of freedom in vehicle maneuverability. It features onboard adaptive behaviors, developed to provide additional insights into subsea features. The onboard autonomous capabilities, together with high specification instruments – including a laser scanning system and multibeam sonar technology – resulted in a detailed external inspection of subsea pipeline features. In addition to commercial applications, Oceaneering has been engaged in projects with the U.S. Navy, where the Freedom AUV has been used to evaluate capabilities of the platform for potential future development of a large displacement unmanned undersea vehicle (LDUUV) prototype.
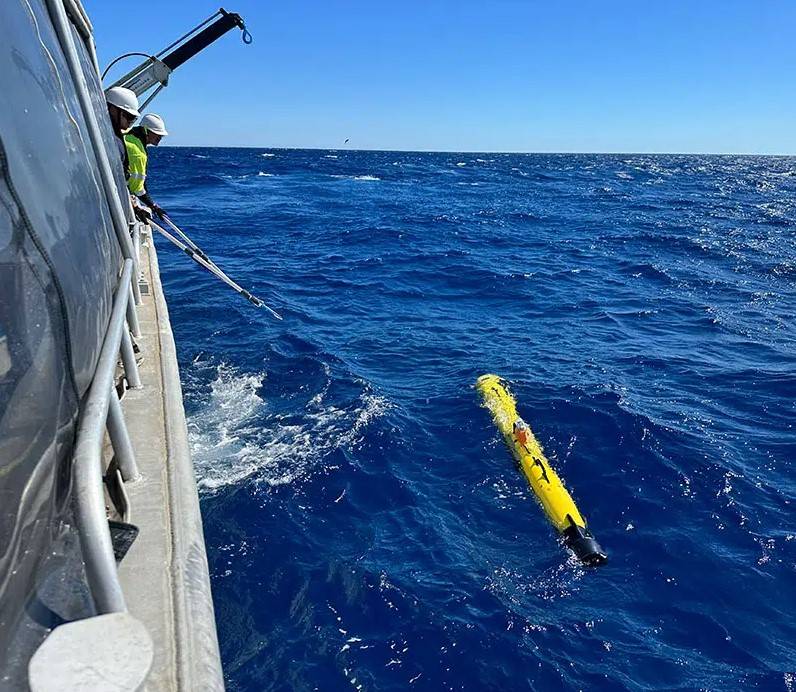
UTEC tested its upgraded Teledyne Gavia AUV offshore Australia earlier in 2024, achieving several milestones – including the deepest dive and the first-time positioning with the new subsea ultra-short baseline (USBL) system, which aids the vehicle inertial navigation system positions. The Gavia AUV is suited for use for reconnaissance surveys, route surveys for cable and pipeline pre-engineering, site surveys, as well as pipeline and platform inspections. The upgrades to the Gavia AUV conducted by UTEC included the addition of INS/Doppler velocity log (DVL) modules (PHINS C3 and Pathfinder DVL); battery modules increasing mission endurance from six hours to 12; cNode USBL modules and nose cone enabling USBL tracking, aiding acoustic communications to the AUV and incorporating a new eight-megapixel camera in the nosecone.
The most significant upgrade, however, is the addition of the module that enables subsea USBL aiding of the vehicle INS positioning. This means the vehicle does not need to surface periodically to update the internal position and account for INS/DVL drift, creating efficiencies by allowing the vehicle to remain subsea and on task for the full 12-hour mission endurance as well as allowing use of the full 1000 m depth rating.
Previously, the requirement for the vehicle to return to the surface to update real-world position using Global Positioning System (GPS), meant that the deepest that the AUV had worked was 100 m, as anything deeper was too inefficient with the time spent diving and surfacing to update the position in deeper waters.
Exail, RTsys and Abyssal Team
In a significant development for seafloor mapping, Exail has joined forces with RTsys and Abyssal to advance the capabilities of AUVs in complex subsea operations as part of the French government-backed project CARMA, that aims to develop swarms of AUVs for efficient ocean floor mapping.
The companies will work together to create a solution in which a multi-sensor underwater drone, capable of diving to 3,000 meters, will coordinate multiple AUVs to increase the surface of the exploration area, with the deployment of operational demonstrator expected in 2026.
As part of this project, for which the companies entered into strategic partnership in July 2024, Exail will improve the capabilities of its deepwater AUV A18-D to serve as the leading AUV to guide the swarm and enable navigation down to 3,000 meters.
RTsys will extend the capabilities of its newly developed AUV COMET-3000 to dive up to 3,000 meters. Multiple units will be provided to act as followers, along with the development of an innovative launch and recovery system for the AUV swarm.
ABYSSA will focus on developing exploration strategies for deep-water swarms of AUVS, and will also process the magnetic data collected to map the magnetic anomalies on the seabed. At the same time, the project will carry out a preliminary study on extending exploration capacity to 6,000 meters depth.
ROVs
In the ROV segment, companies like Reach Subsea, Seatools and DeepOcean are pushing the boundaries of what ROVs can achieve, offering more precise, autonomous, and efficient subsea operations, while some, like Soil Machine Dynamics (SMD), signal a shift to fully-electric ROV, having recorded its first sale of such unit in 2024.
SMD has developed a modular robotic range ROV, available in work-class and survey class forms. The Quantum EV platform is suitable for heavy-duty construction, IRM, salvage and science work. The lighter-duty Atom EV is well placed for renewables, drill support and IRM applications.
SMD claims that its new robotics range is twice as efficient as an older generation hydraulic ROV. For a given input surface power, a hydraulic ROV will only convert around 34% into usable thrust performance.
However, SMD said its EV range is capable of converting 63% of the input power into useable thrust performance.
According to the company, its robotics range does not just offer better performance and reliability but they also consume less energy and dramatically reduce potential oil contamination risk, making operations more cost-effective and environmentally friendly.
In March 2024, SMD sold its first electric ROV to Luxembourg-based marine contractor, Jan De Nul Group.
SMD’s Quantum EV will be integrated into Jan De Nul Group’s new cable laying vessel, Fleeming Jenkin, and deployed to offshore energy projects globally.
The new fully-electric ROV offers superior levels of stability, position-keeping, efficiency and reliability, for increased performance across a wide range of subsea applications, at a lower operational cost, noted SMD.
Seatools, a specialist in subsea technology, has partnered with Belgium-based offshore installation services firm DEME to develop and deploy a state-of-the-art fall pipe ROV. This ROV is specifically designed for subsea rock installation projects, where precise placement of materials is required to protect pipelines and other subsea infrastructure. The newly developed Fall Pipe ROV introduces several innovative features, including the integrated rotator, which enables the offsetting of the ROV’s heading relative to the vessel heading. This innovation ensures an optimal vessel heading, enhancing the workability level of rock installation operations while saving significant power compared to conventional Fall Pipe ROVs, according to Seatools. Another feature of the ROV lies in its expansive on-board survey equipment suite, employed for precise ROV positioning, monitoring operations and the environment, as well as conducting comprehensive pre- and post-surveys. The Fall Pipe ROV passed Factory Acceptance Tests (FAT), conducted by Seadrill, ahead of deployment on DEME’s rock installation vessel Yellowstone, which secured a job in the U.S. to work on the Coastal Virginia Offshore Wind project, where DEME is installing 176 monopile foundations, three offshore substations and subsea cables.
About the Author
Amir Garanović is managing editor of Offshore Engineer. He has covered offshore energy and maritime industry since 2014, with a special focus on renewable energy sector and emerging clean energy technologies.