Tech File
Pile Driving Hammers
It’s [Menck] Hammer Time!
Driven by a “massive step change in offshore wind turbine technology” premised on growth of the per unit size and output, Menck – an Acteon brand – last month unveiled what it touts as a “game-changing” MHU 6000W Wind Hammer, the largest hammer in its repertoire and a continuing a legacy of innovation since 1868 from this north Germany industrial company.
By Greg Trauthwein
We recently visited with Fabian Hippe, Marine Foundations Sales Director, Acteon, for a discussion on the new pile driving unit and the markets it will serve. Hippe, based just north of Hamburg, is well-suited to discuss the company and the market evolution, as he joined Menck in 2006 and for a five-year stretch to 2021 served as its managing director.
“We are approaching the limit that mankind can build right now,” said Hippe, “as with the 6000 we have maximized the weight of the ram that we can build.”
Though the Menck hammers were originally designed for [and still used in] the offshore oil and gas market, the MHU 6000W is designed to meet the growing demands of the offshore renewable sector, opening up new possibilities for offshore wind projects by handling larger and heavier piles in increasingly challenging environments.
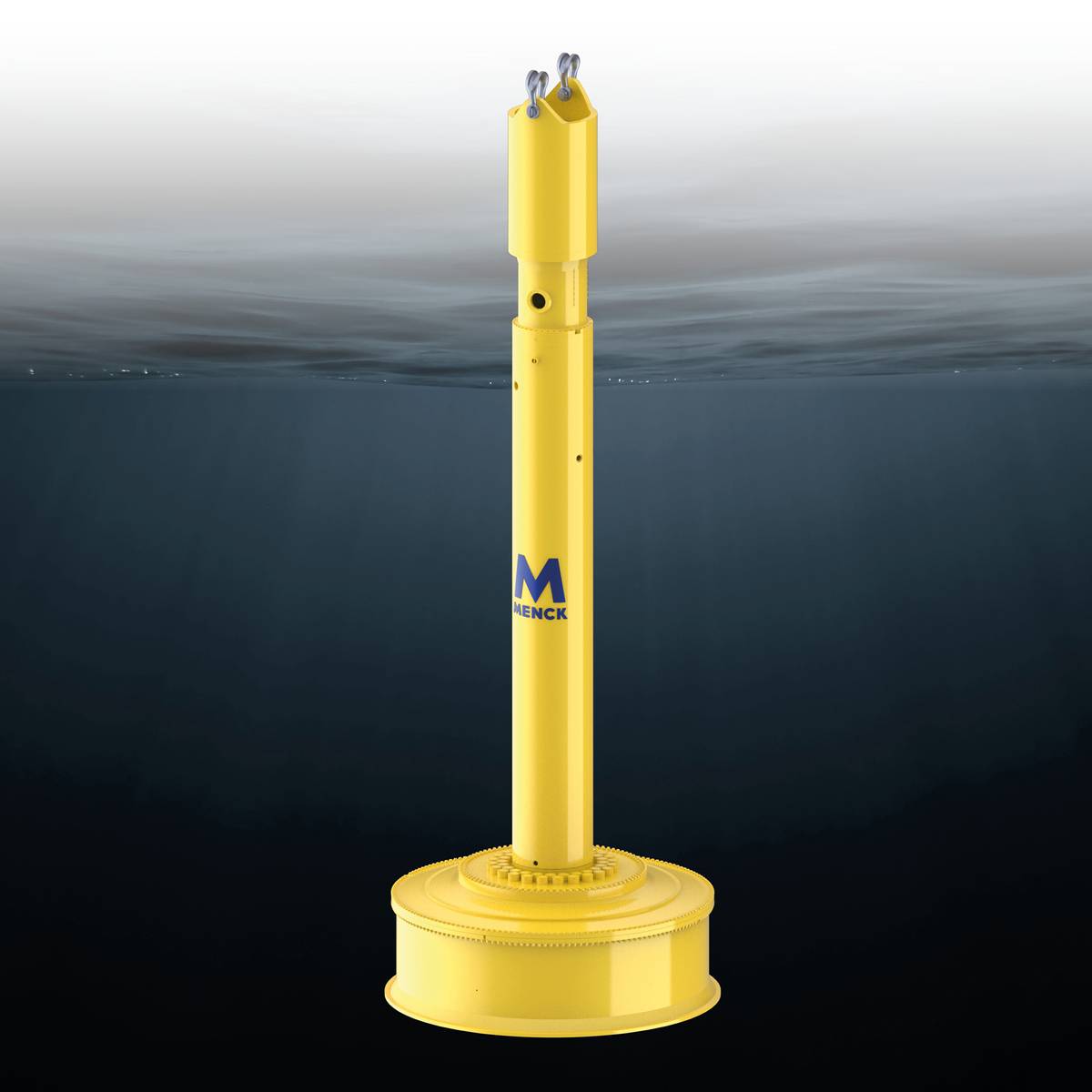
“Fifteen [or so] years ago we were talking about 2-4 MW turbines; today we’re installing 15-16 MW turbines, now we’re talking about 25 MW turbines. This is a massive step changes in technology,” said Hippe.
Everything about the offshore renewables market is big, and while there are starts and stops in some regions, Menck and Hippe are eying massive market growth for units of this size starting in 2028. Hippe said that today Menck has committed to the forgings for the new MHU 6000W, and the plan is to have them built and available for use by the start of 2027 – aiming for 2027 to have it available.
To put the growth of renewables in perspective, Hippe said that five years ago, offshore oil and gas accounted for about 60% of Menck’s revenue, the other 40% to offshore renewable energy. Today that script is flipped, and while the offshore oil and gas business has been stable, “there has been a tremendous growth in renewables,” and today about 75% of Menck’s revenues come from offshore renewable energy with about a quarter from oil and gas.
Image courtesy ActeonTo put the amount of power being laid down by its hammers in perspective, Fabian Hippe said the smallest unit in its arsenal today – a 100KJ, double impact hydraulic hammer – delivers a force analogous to a Porsche crashing into a wall at about 28 mph. The new hammer coming to market in 2027 is a 6250KJ system, “which is the equivalent of a Porsche hitting a wall at 190 mph!
The Tech Behind the Hammer
The Wind Hammer is engineered to drive larger piles in tougher environments and install longer piles in deeper waters, to enable the deployment of a future generation of monopiles with top diameters of up to nine meters. Delivering from 100 kJ to 6,250 kJ of energy to drive monopiles with diameters up to 9 m and beyond, the Wind Hammer provides unmatched power and efficiency.
When Menck was formed more than 156 years ago by “two guys who joined together to manufacture boilers,” even in the first year of business they developed a steam-powered engine to drive a pile, said Hippe.
To put the amount of power being laid down by its hammers in perspective, Fabian Hippe said the smallest unit in its arsenal today – a 100KJ, double impact hydraulic hammer – delivers a force analogous to a Porsche crashing into a wall at about 28 mph. The new hammer coming to market in 2027 is a 6250KJ system, “which is the equivalent of a Porsche hitting a wall at 190 mph!
Key features of the hammer include a double-acting hydraulic drive, closed-loop control, shock absorber cartridges and comprehensive safety mechanisms. By driving a larger hammer at a lower energy, the Wind Hammer also reduces machinery wear and tear and minimizes underwater noise.
While driving impact is critical to efficient build out of offshore wind farms, so too is doing the job with a minimization of noise as ‘noise pollution’ is increasingly a point of contention in the world’s waterways.
“We need to drive the pile, but we need to be quieter in the water column to adhere to regulations,” said Hippe. He said making the equipment larger has actually had a positive effect on the noise emitted.
“Oversizing the equipment has a positive impact on noise, as you’re striking with a heavier weight at a lower velocity and delivering the same energy.”
By incorporating the Menck Noise Reduction Unit (MNRU), the Wind Hammer ensures efficient and environmentally responsible installations, reducing noise, pile fatigue and operational costs.
In addition, the MHU 6000W machinery will be connected to Menck’s real-time digital and data platform, meaning the machine draws on decades of pile-driving experience and places that knowledge at the fingertips of the operator offshore, while giving full situational awareness to offshore operations and onshore engineering and equipment management real-time support.
“As the offshore renewable sector expands beyond traditional regions, we face new challenges, including unexplored natural soil deposits,” said Hippe. “The MHU 6000W Wind Hammer is designed to meet these challenges head-on, delivering the power, precision and operational insights to install the ever-larger foundation structures required as wind turbine sizes continue to grow. As we venture into deeper waters and navigate changing soil conditions, this innovation is critical to ensuring we remain at the forefront of the renewable energy landscape.”