Tech Talk
Valve Replacement
Izomax Aims to Revolutionize Maintenance Without the Downtime
Time was when a defunct butterfly valve could shut down an entire LNG plant for maintenance and repairs. With the patented AOGV (Add-On Gate Valve) technology gaining traction with major operators, Stavanger-based Izomax enables the execution of crucial maintenance and repair work without shutting down operations and impacting uptime and revenue.
By Kjetil Aamodt, Principal Engineer, Izomax
Preparing an Izomax AOGV for servicing in the workshop.
Photo by Rune HavnThe AOGV technology has proved its capabilities over the seven years that have passed since the initial operation, on the Goliat installation in the Barents Sea. Since then, Izomax has delivered a total of 200 operations worldwide that have caught the eye of the energy sector. This summer, Izomax signed a three-year global frame agreement with Shell. The supermajor has ambitions to use AOGV to reinvent their maintenance practices and introduce predictive maintenance measures to reduce downtime and unplanned outages while maintaining revenue streams.
In this article, I will highlight two case studies proving the versatility of the AOGV system and give a short account of the R&D process.
Case Study 1:
Replacing a Flow Meter on a Live Butane Pipeline
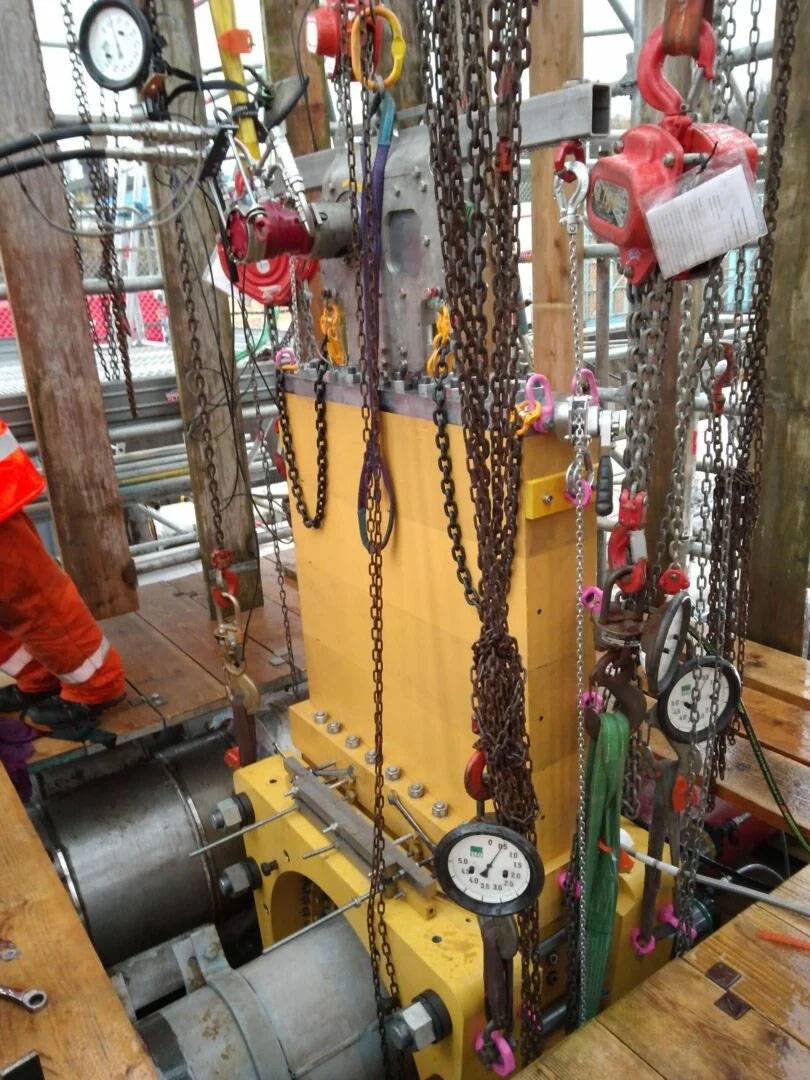
An 18-inch class 300 butane pipeline, spanning 11 km and operating at 12 bar (175 psi), had a leaking flow meter that needed to be isolated for replacement during a brief, three-week window. Pipeline design entailed that it could not be fully drained and refilled, making conventional solutions impractical. Located in a residential area, the asset owner sought to avoid the risks and costs associated with a complete pipeline replacement. There were no suitable isolation points near the defunct meter, limiting intervention options. Several alternative solutions had been deployed to attempt to solve the external leak, without success. Further complicating matters, asbestos was discovered in the gasket, requiring specialized handling, decontamination, and disposal procedures.
Izomax’s patented AOGV provided a mechanical isolation solution without hot work. The tool can insert and retract a blind spade between flanges on a pressurized system, allowing for the isolation of sections for repairs and replacements. In this case, the AOGV enabled the flow meter replacement on the butane pipeline while minimizing gas freeing and keeping the main process operational.
An 18-inch ASME Class 300 AOGV was designed, engineered, and manufactured for the application. Working closely with the facility owner, we attended a HAZID on the site and hosted a Factory Acceptance Testing at our Stavanger workshop.
Identifying Asbestos within the gasket in question, Izomax engaged with specialist handlers in advance, while developing a brushing tool to safely remove any remaining debris. The performance of the AOGV was verified for high pressure services using finite element analysis and by pressure testing to 1.43 times design pressure (as per the EU Pressure Equipment Directive (PED) (2014/68/EU) and EN 13445 – Unfired Pressure Vessels prior to deployment).
A team of five Izomax AOGV specialists carried out this onshore operation, lifting the AOGV into place via a mobile crane, before scaffolding and rigging was used to assemble and deploy the system. Providing positive isolation, the AOGV mechanical isolation tool inserted an isolation spade between a flange pair and a built-in isolation valve, enabling depressurisation and gas-freeing of a very short section of the pipeline. The isolation allowed for removal and replacement of the leaking flow meter, whilst keeping the liquid butane inventory within the pipeline.
Timely completion was essential, as the terminal’s butane tanks had only three weeks of production capacity. Izomax completed the operation in two weeks. The AOGV’s ability to isolate the pipeline provided the only effective solution. The operation was executed without any health, safety, or environmental incidents, and no non-productive time was incurred.
No hot work was required, significantly reducing time, cost, and health, safety, security, and environmental (HSSE) risks. The asbestos in the existing gasket was safely handled and disposed of through an approved decontamination process on-site. The integrity of the system was maintained throughout, and the plant was restored to its original operating condition without complications.
By avoiding a production shutdown, the Izomax AOGV system saved the operator an estimated $15 million USD. This direct financial saving, combined with the mitigation of operational risks, made the AOGV technology the key factor in the success of the project. Without it, a much costlier and riskier alternative would have been necessary.
Developing the AOGV
The research and development journey leading up to this and many similar successful case studies, was made possible with the help of friends and a small team of colleagues. I was on double duty, as both manager and engineer in the Pipe Intervention team at Stavanger-based IK Group (which later spun out Izomax). Back in the early 2000’s, IK group was working both on subsea and topside piping maintenance and repairs.
Replacing a valve or intervening in a processing plant required a shutdown, isolating the problem area with the existing system valves, emptying the affected area of liquids and/or gas to make it safe and then starting work. If hot work was involved, a further set of risk management and health and safety procedures were implemented to ensure a safe working environment.
The basic idea for what would become the AOGV initiated after a facilitated HAZOP for a Hot tap and stopple with the purpose of opening a pair of flanges. We asked ourselves: What would it take to open a flange pair while a system is running? Working directly on flange pairs instead of using existing valves seemed like a better approach to isolate the problem area, rather than shutting down whole sections of piping.
The question was left unanswered at that point, but it kickstarted something in my engineering mindset; something that would keep me occupied on an off for the next years. With my experience from manufacturing pressure holding clamps for subsea use, I knew a lot about pressure containment and piping engineering that I could put to use solving the problem.
Instead of being dependent on the pre-installed valves that come with the plant, I wanted to do something radically different. Operating directly on the flange meant coming up with a method to separate the flange and insert a device that mechanically blocks the flow through the pipe, isolating one side of the device (and the contents in the pipe) from the other. And it was how to do that separation that eluded me for many years.
The main challenge when separating a bolt circle on a flange on a live, pressurised system is the pressure within the pipe. Depending on the pressure, the separation force pushing the sections of pipe away from each other can be hundreds of tons. To loosen the bolts on the flange, I needed to find a way to both compress the flange so bolts could be loosened, and at the same time contain gas or liquid at pressure escaping through the loosened flange seal.
I understood that the idea was a radical one and was hesitant to share the process until it was more mature. So, I spent the next years mulling this problem, on and off. Mostly while spending time at my cabin in the mountains of scenic Telemark in Norway, chopping wood and hiking.
I would be drawing sketches on scraps of paper lying around, trying to figure out a way to make the idea work, then leaving it dormant for months at the time in between. I finally figured it out one day in 2015, and I experienced physical reaction when it finally dawned on me. I remember the hairs on neck standing on end as I had this pretty intense Eureka moment! Then I grabbed some cardboard divider sheets from an old ring binder lying around and made the very first working prototype of the mechanism. With this in hand, I could approach a small circle of trusted friends and colleagues to refine the principle.
Building a Pressure Chamber Around the Flange
In essence, the principle of the AOGV is to build an entire pressure chamber around the flange to contain the pressurized contents. The pressure chamber unit incorporates bolts that can compress the flange, relieving force on the original bolts so they can be loosened. A separation of a couple of centimetres then allows a mechanical blocking device like a blind spade or a spectacle blind to be inserted before re-tightening the flange. The same principle allows for a wafer butterfly valve to be replaced, as the valve is situated between pipe flanges.
To isolate a section of pipe, blind spades may need to be inserted at several points, leaving the section mechanically isolated so work can be done. Achieving smart interventions on a working process plant, requires that there are redundancy sections that can take over the operational workload. The inherent capabilities of the AOGV technology uncovers at lot more of micro redundancy with its ability to insert positive isolation in any flange pair.
Pressure is definitely one of the main challenges, but so are the dimensions of the piping involved and the complex nature of a processing plant. Plants and any sort of piping installations can be messy places, with close proximity to other piping, constraints such as walls and a general lack of space. That is why the majority of AOGVs are designed as bespoke units. A close inspection of the worksite, and even 3D scans in some instances, are the basis for designing the hardware to be produced for the specific purpose.
The main principle of the AOGV is the same for all pipe dimensions, from 2-inch pipes up to our largest AOGVs to date, the 36-inch pipes described in the second case study. But of course, complexity increases with the larger pipe diameters as the weight and size of the AOGVs involved create their own logistical and HSE challenges. The second-generation AOGV we use today has improved from the first-generation version in that we have added hydraulic compression of the flange to the unit, replacing the bolt compression we first used.
Izomax is in the maintenance and repair business, and for operators facing huge and complex maintenance and repair challenges, what matters most is to find the least costly option. The alternatives for operators are, in many cases, to shut down installations completely and bear the massive cost of revenue loss during downtime. Operators easily see the benefits of AOGV, frequently commenting that the technology has revolutionized their maintenance options.
Offering the alternative to isolate smaller areas for required maintenance, and execute planned, predictive maintenance on crucial components, the AOGV entails a cost-effective option to shutdowns. In cases where there are parallel process segments for redundancy backups, AOGV operations on one segment will not impact the overall operation of the installation.
Case Study 2:
Replacing a Stuck Butterfly Valve at a Supermajor LNG Plant
At one of the world’s largest LNG facilities, a butterfly valve on a 36-inch class 150 flare line operating had been stuck in a closed position for an extended period. The stuck valve prevented the backup flare system from being used, thus limiting the options available to undergo planned maintenance without shutting down the entire plant. The working temperature of the line could range from ambient to cryogenic in the event of a sudden slugs of liquids, and the faulty valve needed to be replaced. Solutions were required to mitigate HSSE risk associated with the valve replacement, as there were no suitable built-in isolation points close to the stuck valve. The plant operator had evaluated alternatives, concluding that few, if any, robust or cost-effective solutions were available.
The Izomax AOGV mechanical isolation tool which can set and retract a blind spade in a pair of flanges on a pressurised process system, e.g. a flare system, without hot work. The blind spade or a combination of several spades in different locations can facilitate the replacement of valves and pumps. The AOGV can also be used to take a vessel out of a closed loop temporarily for safe entry and bringing it back on-line, while the main process is kept in continuous operation.
A 36-inch ASME class 150 AOGV system, the largest developed to date, was designed, engineered, and manufactured for the valve replacement operation on the live flare system. The design incorporated geometrical constraints from the site, adhered to the Pressure Equipment Directive and EN 13445 standards and was verified through third-party FEM/FEA analysis. DNV assessed the tool's conformity, including design review, material evaluation, and production oversight. Pipe flexibility was also analysed to ensure the system met piping design codes.
Detailed planning was conducted in collaboration with the facility owner, including site preparations and operations. A HAZID was performed, and the customer attended a Factory Acceptance Test at Izomax’s facility in Stavanger. Testing of the AOGV tool at cryogenic temperatures (-196°C) was completed, and the operation was rehearsed on a mock-up rig before shipment to the site.
During the operation, scaffolding and rigging support were provided by the site owner, and coordination among personnel in the confined space was critical. The Izomax AOGV system was installed and suspended to prevent additional load on the pipework. After leak testing, the flanges were separated for approximately 30 mm, and a blind spade was inserted for positive isolation at the upstream flange. The faulty valve was safely removed and replaced, following agreed procedures. and the system returned to normal operation. The AOGV mechanical isolation system was reinitiated, the blind spade removed, and the system brought back to normal operation. The main flare was operational throughout the entire operation.
The entire operation was completed without any HSSE incidents or downtime, to the client’s satisfaction. The AOGV system solved a long-term issue that other technologies could not address due to unacceptable risk levels. Despite logistical challenges due to worksite location, the tool was delivered and operated on schedule.
The plant's system integrity was maintained throughout the process, with the flare returned to its original condition after the AOGV operation. The LNG plant was running full speed through the complete operation, no interference to the delivery of the LNG.
This project highlighted the efficiency, safety, and cost-effectiveness of the AOGV system. The ability to isolate equipment without disrupting operations makes it a valuable tool for similar industrial applications, where traditional methods pose higher risks.
About the Author
Kjetil Aamodt is a mechanical engineer with 40+ years of experience from the energy sector on the Norwegian Continental shelf. He is the inventor of the AOGV and has worked for IK Group and now Izomax since 2007.