Tech Notes
New Products, Technologies and Systems
Floating Wind Turbine to Help Cut Platform Emissions
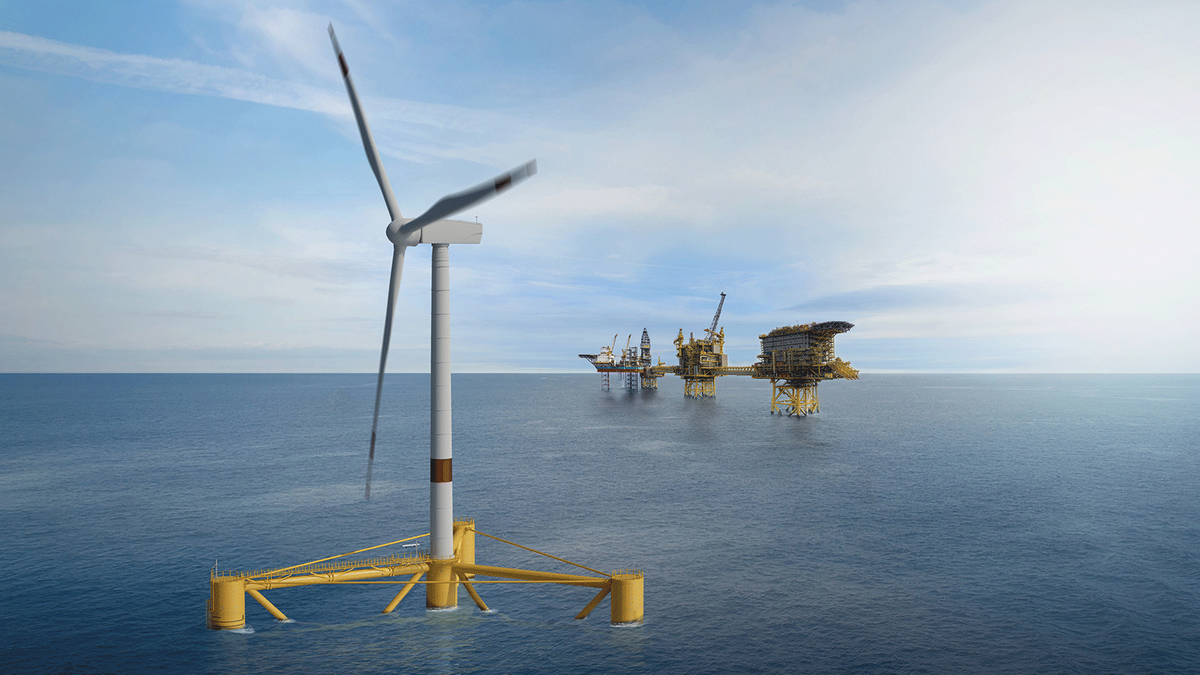
TotalEnergies unveiled plans to install a 3 MW floating wind turbine to provide renewable power to Culzean offshore platform in the UK North Sea. The 3 MW floating wind turbine will be located 2 km west of the Culzean platform, 220 km off the eastern coast of Scotland. The turbine, expected to be fully operational by end 2025, will supply around 20% of Culzean’s power requirement.
It will be installed on a modular, light semi-submersible floater hull designed by Ocergy, allowing for fast assembly and optimized costs, as part of the pilot project selected by Crown Estate Scotland’s Innovation and Targeted Oil & Gas (INTOG) leasing round.
XolarSurf Offshore Solar Prototype
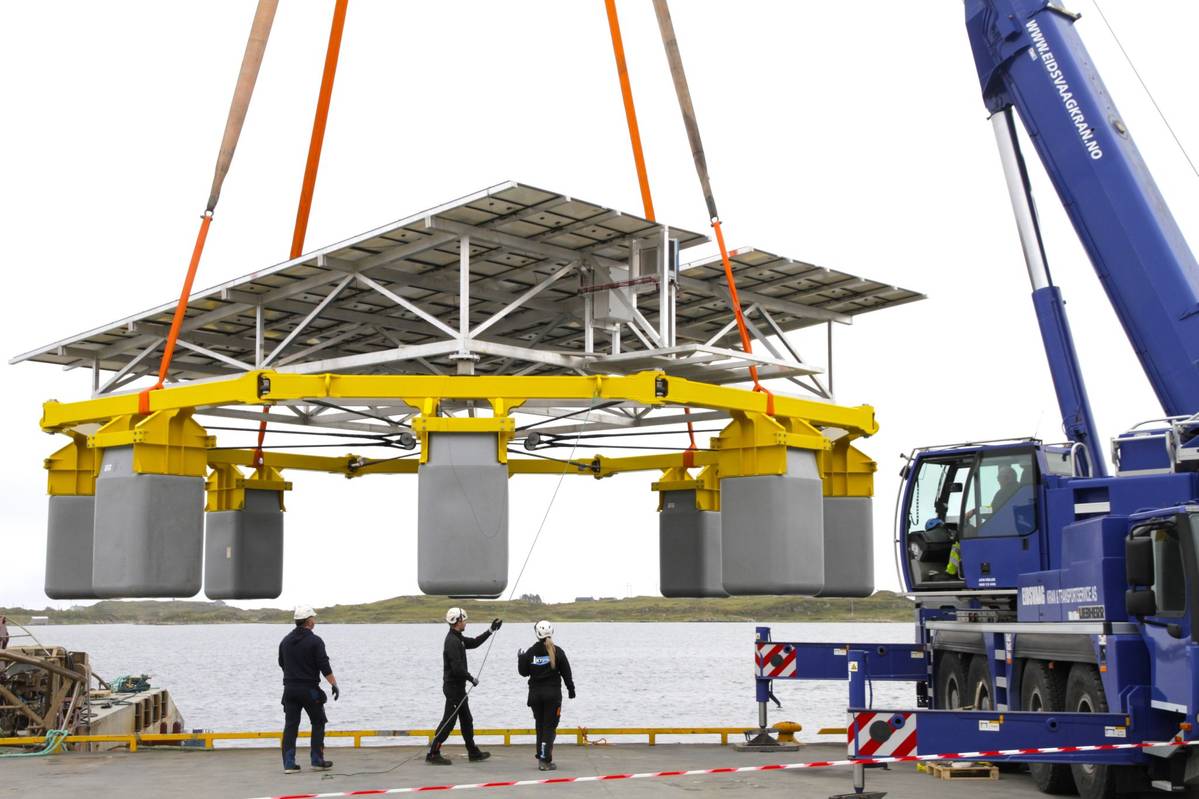
Developed as part of a joint effort by Saipem, Moss Maritime, and Equinor, the XolarSurf offshore floating solar prototype unit has been deployed offshore Norway where it will remain under sea trials for one year for performance and production assessment.
XolarSurf is a modularized floating solar technology developed by Moss Maritime, Saipem's Norwegian subsidiary specialized in design and engineering services for the offshore energy as well as other ocean-based sectors.
The solution can produce electricity from solar panels mounted on floaters specifically designed for marine environments.
Its design grants significant flexibility as it is formed by ‘islands’, each one consisting of several smaller floaters providing a safe space for the photovoltaic panels. Each floater may generate up to 35-45 kWp of installed power.
Designed to withstand waves up to 8 meters, the deployment represents the first full-scale test and a key milestone in the readiness of the product.
Offshore Nuclear for O&G Decarbonization?
Saipem and newcleo have signed a collaboration agreement to identify solutions for the offshore application of newcleo’s technology to produce nuclear energy, which could provide zero-emission electricity for oil and gas installations.
The companies will study the application of newcleo’s Small Modular Lead-cooled Fast Reactor (SM-LFR) technology to provide zero-emission electricity and process heat to oil and gas offshore installations, thereby improving their sustainability performance.
The agreement also allows for the possibility of extending the use of newcleo’s technology to produce zero-emission electricity through floating nuclear units, connected to the electricity grid on land or to other users.
newcleo's solution leverages passive security systems (exploiting natural forces or phenomena without requiring active mechanisms), unique in the marine environment, enabling efficiency in the use of extracted uranium.
“The production of zero-emission energy through floating offshore plants equipped with new generation compact reactors could represent a new frontier in the energy transition. With this collaboration agreement, we leverage Saipem's distinct skills in the offshore sector as well as our ability to bring innovation to the world of energy infrastructure, to explore new solutions that can accelerate the path towards decarbonization,” said Alessandro Puliti, CEO of Saipem.
OPT’s PowerBuoy
Ocean Power Technologies (OPT) recently completed the demonstration of its next-generation PowerBuoy, designed as an uninterruptable offshore power supply unit which exploits the energy of waves, sun and wind.
OPT completed more than four months of offshore testing of its next generation PowerBuoy in the Atlantic Ocean off New Jersey. The solar and wind power equipped PowerBuoy also featured OPT’s AI-capable Merrows suite of solutions. The system maintained 100% data uptime and the state of charge of the batteries remained over 90% throughout the deployment, according to the U.S.-based company.
During the deployment, several intelligence, surveillance, and reconnaissance demonstrations for potential customers were completed.
OPT’s PowerBuoy has been designed to act as an Uninterruptable Power Supply (UPS) which constantly recharges itself by harvesting energy from the waves, as well as wind and sun.
ZEUS Bridges the Power Generation Gap
Aker Solutions, in collaboration with Petronas and Clean Energy System, launched a pilot project featuring the Zero Emission Power Station (ZEUS), a pioneering energy solution that uses oxyfuel combustion with immediate CO2 capture and storage. The ZEUS technology employs advanced oxyfuel combustion to convert high CO2 natural gas into dispatchable power while capturing 100% of the CO2 emissions.
The CO2 is immediately injected into a reservoir for permanent storage or can be used to increase production of both oil and gas before being permanently stored.
The advantage of ZEUS technology innovation is the ability to handle the combustion at elevated pressures, enabling more compact and simplified process equipment. This could lead to significant cost savings while enhancing CO2 management capabilities. In short, ZEUS aims to deliver zero-emission, affordable and reliable power and it is positioned to be a significant bridge technology in the transition to a more sustainable energy landscape.
Jack-Up Platform Enables All-Weather Nacelle Maintenance
Knud E Hansen designed a “Jack-up on Jack-up” vessel concept for offshore wind farm maintenance.
The four-legged jack-up vessel features a 15m wide working platform that can be jacked-up to the height of a nacelle to provide a safe platform for maintenance work on the blades eliminating the need for hazardous rope access.
With a telescopic weather cover fitted on the platform, work on the blades can be done in practically all weather conditions, day or night, resulting in more working hours annually than with conventional maintenance vessels.
A large, air-conditioned workshop is located at the aft end of the work platform, and when the weather cover is deployed, a virtual factory hall is created around the blade, allowing all types of work to be performed on the blade, minimizing the need to remove the blades and transport them to shore for repair.
Additionally, there is the possibility of inserting an X-Y motion compensating system between the work platform and the platform carriers so the “factory hall” can remain geostationary.
A “cherry picker” mounted on a hammer head at the platform’s opposite end provides the access to the nacelle. The main crane is fitted on the elevating structure, allowing for the use of a conventional pedestal-mounted crane with a boom that is approximately 30% shorter than that of a conventional wind turbine maintenance vessel, which should be able to reach the same height, providing a much better view of the blades and the nacelle from the crane driver’s cabin.
Measuring 154m in length and 64.4 m in breadth, the vessel is designed for all kinds of maintenance work on wind turbines up to 20MW, including replacement and handling of nacelles weighing as much as 1,000t at a hub height of 175m, and managing blades up to 130m long. This can be done while it is jacked up in 80m water depth.
ABS Type Approval for In-Situ Carbon Fiber Composites Repair Technique
Toray Industries became the first in the world to obtain type approval from the American Bureau of Shipping (ABS) for its vacuum-assisted resin transfer molding (VaRTM) process for in-situ ship repairs. The technique entails applying carbon fiber reinforced plastic (CFRP) to corroded areas with reduced thicknesses of floating production, storage and offloading (FPSO) and floating storage and offloading (FSO) systems. ABS accounts for around half of FPSO and FSO certifications. This approval enables these certified vessels to employ the proprietary VaRTM process, reducing the time needed for engineering reviews and verifications for ship repairs.
FPSO and FSO maintenance is normally offshore using steel materials. The welding, or hot work, halts oil and gas production. Toray and MODEC, Inc., jointly developed the VaRTM repair process in 2020. It entails applying Toray’s TORAYCA carbon fiber woven fabric, which offers excellent strength and elasticity, to the surfaces of existing steel structures. The next step is to cover the fabric with a film, vacuum-seal, and inject epoxy resin that then cures to complete repairs by bonding the CFRP to the steel structures.
Another advantage of this in-situ VaRTM process is that it is easier than with regular steel-based techniques to transport materials and equipment to locations and perform repairs faster and with fewer people and time. The procedure does not involve hot work, minimizing impacts on oil and gas production.
“Swift by Name, Swift by Nature”
Zelim’s founder and CEO Sam Mayall has a simple mission: make man overboard recovery at sea easier, more efficient, more predictable. In fact, he wants to make MOB recover ‘boring’. To accomplish the job, Zelim debuted a comprehensive system, including the Guardian vessel and Swift in-water recovery system at SMM.
INS to Boost Wind Turbine Installation Precision
Inertial navigation systems (INS) manufacturer Exail has secured a contract to supply three Hydrins INS to Pliant Offshore, an offshore measurement specialist. The units will be integrated into Pliant Offshore’s installation measurement system to improve the accuracy and efficiency of wind turbine installations. Pliant’s technology is designed to provide real-time measurements of the inclination and position of structures, such as monopiles, during installation. The system uses 3D point cloud technology combined with laser sensors to measure and virtually reconstruct objects with high accuracy.
The integration of Exail Hydrins INS enhances the system performance by providing precise positioning and motion compensation, even on moving vessels. This enables the installation measurement system to take continuous measurements during the pile-driving process, guaranteeing the correct positioning and stability of wind turbines in challenging offshore conditions.
SLB Launches Carbon Storage Well Integrity Assessment Tool
SLB launched a well integrity assessment solution that helps carbon storage developers quantify the risks associated with wells at prospective storage sites with previous drilling activity.
Establishing secure storage sites is essential to enabling growth of CCUS and creating a low carbon energy ecosystem, said SLB. Many prospective carbon storage sites are located in either mature or retired oil and gas fields, and having a large number of wells at a site can increase the risk of potential leakage pathways for the stored carbon.
The company’s new methodology for quantifying the probability and potential impact of carbon leakage helps customers understand the risks associated with each well, informing remediation strategies and ultimately estimating the project's long-term viability.
SLB's well integrity assessment solution incorporates advanced failure mode effect and criticality analysis (FMECA) to assess potential leakage pathways, well barrier, failure mechanisms and resulting consequences. Using advanced multi-physics 3D modeling, SLB can assess the volume and flow rates of brine and carbon leakage over time to better estimate risk.