Subsea
Digitalization
Remote Control
The more production infrastructure we push to the seabed, the more data we need to pull back up. With it comes opportunity.
By Wendy Laursen
The Baker Hughes subsea digital ecosystem.
Credit: Baker HughesChevron’s landmark 6,500 tons of subsea gas compression infrastructure for Jansz-Io demonstrates the scale of what is being put on the seabed, but there’s a diversity of other infrastructure under development that will operate alongside traditional production systems.
This includes subsea fluid storage technology from NOV Subsea Production Systems, and TechnipFMC and Sulzer Flow Equipment’s subsea CO2 pumps for new high pressure separation technology from Petrobras.
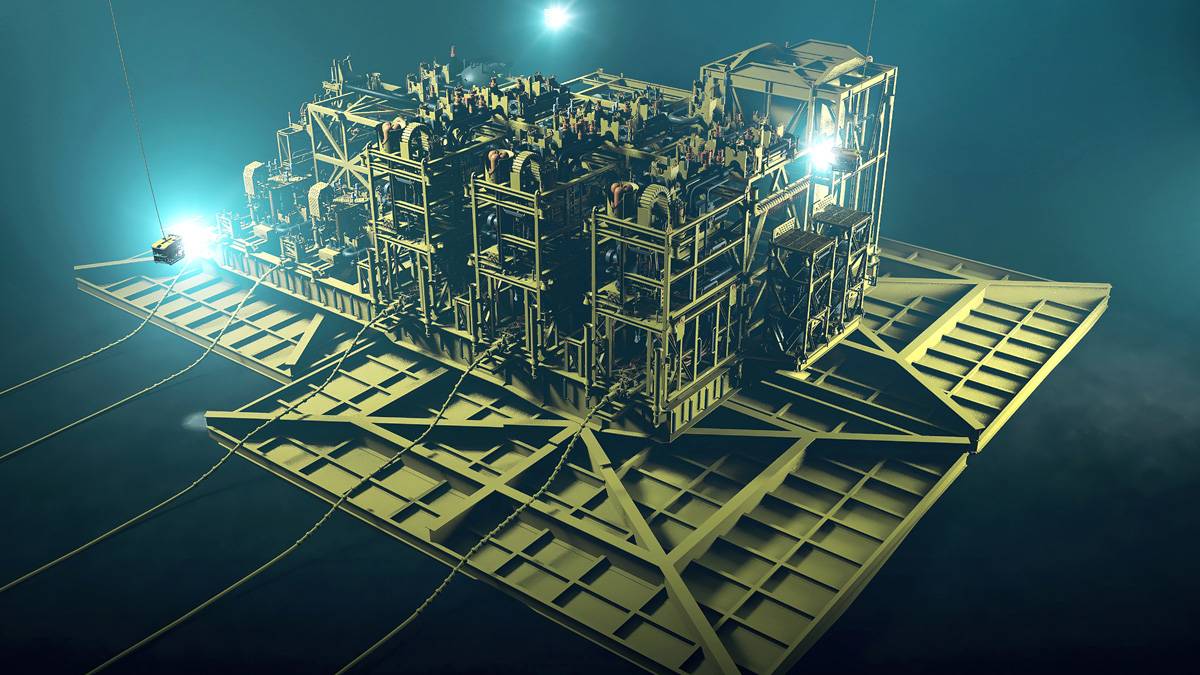
The growing number of new technologies are expected to play a pivotal role in the future of oil and gas production, advancing efficiency and environmental performance. Their digitalization will further these goals by providing remote control, optimized operations and enhanced decision-making capabilities.
Enabling technology for that digitalization, such as subsea power and communications, continue to evolve, says Miguel Hernandez, Senior Vice President of Global Offshore at ABS, even though the subsea environment poses significant challenges. “Maintaining reliable communication links between subsea assets and onshore or offshore control systems is crucial, but connectivity issues such as bandwidth limitations and signal interference can pose challenges,” says Hernandez. “Transmitting data through water, especially at great depths, is challenging due to the attenuation of signals.”
The introduction of 5G technology aims to overcome these challenges and is already being developed for production systems. In July, ADNOC and e& announced a project to build a 5G network that will relay information from sensors embedded in more than 12,000 wells and pipelines to autonomous control rooms. It is due to be completed in 2025 and expected to generate $1.5 billion in value during its first five years of operation.
Also in July, ADNOC announced the deployment of RoboWell, AIQ’s autonomous well-control solution into its NASR field operations. RoboWell uses cloud-based AI algorithms to autonomously operate wells that self-adjust according to changing conditions to enhance safety and efficiency and reduce the need for travel and physical interventions.
A 12-month trial project wrapped up in March that aims to support the electrification of subsea power and communications by combining wave power with subsea energy storage. The Renewables for Subsea Power project connected Mocean Energy’s Blue X wave energy converter with a Halo underwater battery storage system developed by Verlume. The trial off the Scottish coast demonstrated how green technologies can be combined to provide reliable and continuous low-carbon power and communications to subsea equipment as a future alternative to umbilicals. TotalEnergies and Shell Technology recently joined the initiative to now deploy the system on live assets.
Siemens Energy is working on new concepts to make subsea digital systems smarter using its Subsea DigiGRIDTM control, safety and digital twin systems. Endre Brekke, Product Lifecycle Manager for Subsea Automation and Control, explains: “We are designing systems to be able to perform well under significant uncertainties in the system and environment for extended periods of time and without external intervention, that is, operator monitoring and control. We are also working on edge analytics and storage, building in abilities to perform analytics close to the source of the data and to store both raw data and results for an extended period of time.”
Credit: Siemens EnergyWe are designing systems to be able to perform well under significant uncertainties in the system and environment for extended periods of time and without external intervention, that is, operator monitoring and control. - Endre Brekke, Product Lifecycle Manager for Subsea Automation and Control, Siemens Energy
Brekke says industry-standard based integration with topside systems is very important. This enables interoperability between systems from different vendors and enables use of automation standards on the seabed. “This saves CAPEX and OPEX,” he says.
“This approach also enhances liberation of data for optimization of production and maintenance. This is growing even more important, and our Subsea DigiGRID system is designed to do this very efficiently. The Subsea DigiGRID can interface a topside controller on a hard real-time standard automation protocol and, at the same time, from the same hardware, stream data to a topside cloud-based digital twin using a digital twin protocol like MQTT.”
OneSubseaTM, an SLB joint venture, is pushing ahead with subsea electrification, a move that has the potential to increase the amount and quality of data returned topside. The company has been awarded the FEED of a 12-well, all-electric subsea production system with an IoT for the subsea trees at Equinor’s Fram Sør field, offshore Norway. As part of the agreement, future engineering, procurement and construction will be directly awarded to SLB OneSubsea conditional on a final investment decision. The IoT includes three key digitalization efforts: intelligent sensors and actuators on the equipment (rather than spring-operated on/off systems), connectivity through a secure digital platform and the ability to turn data into decisions via analytics and diagnostics.
Credit: OneSubseaThe industry needs more data to develop a deeper contextual understanding of equipment performance to safely extend the productive life of offshore assets and to enable circularity. - John Macleod, Vice President of Technology and Strategy, SLB OneSubsea
“With all these pieces now in place, we have enabled intelligent asset lifecycle performance management for our subsea production systems, including for the trees,” says John Macleod, vice president of technology and strategy, SLB OneSubsea. “Looking forward, the industry needs more data to develop a deeper contextual understanding of equipment performance to safely extend the productive life of offshore assets and to enable circularity.”
For Fouzi Bouillouta, Global Program Manager – EngageSubsea at Baker Hughes, maintaining equipment up-time is critical. With the growing digitalization of a growing number of subsea assets, his aim, using tools such as the company’s modular engageSubsea platform, is to break down data silos, consolidate multiple data streams and bring end-to-end operational visibility and analytics. The system provides a real-time, 360-degree view of installed equipment, preventative maintenance forecasts and critical alarms.
Credit: Baker HughesWhen we speak about digital technology, it sometimes sounds very complex, and expensive, but really it’s all about providing a competitive view of the subsea ecosystem. - Fouzi Bouillouta, Global Program Manager – EngageSubsea at Baker Hughes
Bouillouta doesn’t see digital technology as a black-box approach to problem solving. Rather, the engageSubsea platform is a visualization tool that helps optimize how people communicate and collaborate on the processes that will maximize up-time. One standout feature is engageSubsea Remote, a module enabling remote operations for both Baker Hughes users and customer operations. With it, Baker Hughes has the capability to provide remote technical support via the use of augmented reality tools located on a platform. “This creates a lot of value, instead of sending someone offshore or having to keep someone offshore to look at problems if something happens,” says Bouillouta.
“Today's business complexity necessitates a shift from a reporting culture to true transparency and collaboration in the energy industry. With asset integrity management still representing a significant portion of OPEX, the market needs a solution that leverages data and expertise to proactively manage assets and reduce costs.
“When we speak about digital technology, it sometimes sounds very complex, and expensive, but really it’s all about providing a competitive view of the subsea ecosystem.”
Fram Sør Will be the Tipping Point for Subsea Electrification
OneSubseaTM, an SLB joint venture, recently announced a contract award for its all-electric subsea production system, and John Macleod, vice president of technology and strategy at SLB OneSubsea, sees it as the onset of a tipping point.
“Large investments have been made across the industry to make this capability a reality, and we now see several projects on the horizon that use all-electric as their base case.”
The first project is the recent contract award from Equinor for the front-end engineering design (FEED) of a 12-well, all-electric subsea production systems project in the Fram Sør field, offshore Norway. The solution will use SLB OneSubsea’s standard subsea tree design, upgraded with a fully electrified power, control and actuation system.
“You can only go so far by optimizing component-level performance,” says Macleod. “As we add to our electric capabilities toward a complete pore-to-grid solution, this will trigger further step changes in performance, enabling greater and greater system-level optimization capabilities and cost efficiencies.
“Additionally, an all-electric approach can help to overcome some of the limitations associated with legacy offshore power and control systems. Some of the cases we have looked at for tiebacks into mature infrastructure show an all-electric approach can help to enable the viability of these tiebacks.
“It will also enable the remote control of such assets during the operational phase. The resulting reduction in project cycle time and costs and the ability to produce previously inaccessible reserves can redefine an asset’s net present value for the better.”
All-electric systems are well suited to local energy generation and storage which can be an additional enabler to project viability. Also, electrification leads to reduction of surface infrastructure at the host facility, coupled with the reduction of hydraulics eliminating hydraulic power units and large topside reservoir.
In the future the integration with autonomous underwater vehicles, subsea wireless and subsea power solutions will support even more reduction of infrastructure topside.
“Electrification at a system level will drive simplification of integration with existing infrastructure, moving more to a plug-and-play model for infrastructure led (ILX) resources, for example,” says Macleod.
This is especially important for tiebacks into busy facilities, where plug-and-play power and communications result in much simpler topside modifications, much lower cost and much smaller environmental footprint rebuilding topsides.
The elimination of high-pressure hydraulic systems is expected to enable operators to go further and deeper, improving production and making even marginal fields more viable.
“Electrification is in some cases the only solution to achieve technical, commercial and operationally viable solutions for long distance developments. Using traditional systems, it will be much harder and costly to achieve both acceptable safety and operational performance compared with hydraulic systems during, for instance, shutdown and pressurization of the system. Digitalization of subsea assets facilitates more opportunities for conditioning monitoring, which allows for predictive maintenance and planned interventions or the potential to avoid equipment failure altogether.”
One of the key changes SLB has made is to go from a spring-operated on/off system to a battery-operated and motor controlled one, facilitating much better positional control.
“Ultimately, more control and more data enables realization of optimization that in time may lead toward more closed loop automation, as well as more cognitive workflows. This is becoming an extremely interesting area.”
Macleod points out that the benefits of increased electrification and instrumentation have been recognized across many industries, and history shows that once the benefits are demonstrated at scale, adoption accelerates. “That’s why we believe that the Fram Sør project could pave the way for accelerated industry-wide adoption of all-electric subsea technology, as it offers that industrial, scalable solution. It is built on a solid, proven technology platform, while offering lower cost, smaller footprint and simplified architecture. It is also a necessary piece in the overall digitalization effort of our industry.”