Tech Feature
Coatings
Maximize Offshore Energy Assets Lifespan
Learn how specialized coatings can extend assets and maintain operations
By Anurag Raj, PPG Customer Sustainability Business Partner, Protective and Marine Coatings
Advanced protective coatings remain essential for longevity and sustainability in the offshore energy sector, where assets endure harsh environments. This comes as the International Energy Agency (IEA) projects global wind energy capacity to triple by 2026, reaching 120 gigawatts—with offshore installations representing 20% of this growth.
Offshore oil and gas operators understand the stakes of operating in a harsh environment, with industry reports indicating a spend of more than $1.3 billion annually on corrosion and maintenance. This includes $589 million for surface facilities and $463 million for downhole equipment. As offshore wind expands into these same challenging marine environments, operators face similar durability challenges from saltwater exposure, temperature fluctuations, and high winds.
Advanced protective coatings emerge as a critical solution. These specialized solutions can help extend asset lifespans up to 50 years while reducing maintenance requirements—creating more sustainable infrastructure that aligns with circular economy goals. Beyond mere protection, these innovations help maximize resource efficiency and minimize environmental impact across the offshore energy sector.
Facing Harsh Environmental Challenges
Offshore wind farms and oil and gas platforms face some of the most demanding environmental conditions. Constant exposure to saltwater, fluctuating temperatures, high winds, and, in the case of oil and gas, the added stress of hydrocarbon exposure can lead to corrosion and material degradation. This can ultimately result in costly repairs or replacements. Asset owners increasingly focus on maximizing the lifespan of these installations to protect their investments and help ensure they meet operational and sustainability goals. Protective coatings can help safeguard these assets from environmental elements and operational demands.
Implement Innovative Protection Strategies
Asset owners and operators turn to innovative coatings specifically designed to address the challenges of offshore energy infrastructure. These specialized coatings offer superior resistance to corrosion, UV radiation, chemical exposure and mechanical wear, providing a robust defense against the harsh conditions in severe marine environments. The needs of offshore oil and gas platforms extend beyond corrosion resistance. Coatings must also withstand exposure to aggressive chemicals and hydrocarbons, maintain their protective qualities in extreme temperatures, and endure the physical stresses associated with deep-sea operations.
Companies can unlock significant sustainability and economic benefits by extending the useful life of critical infrastructure like wind turbines, oil platforms and subsea pipelines. For instance, in recent internal abrasion resistance tests, PPG's reinforced novolac epoxy coatings outperformed styrene-free unsaturated polyester coatings by 30%–40% in reducing wear and damage caused by the harsh offshore environment, thereby enhancing the durability of critical infrastructure.
Guide Better Choices
The longevity and sustainability of offshore energy infrastructure—whether in wind, solar, or oil and gas—is evaluated through life cycle assessment (LCA) and digital modeling. These tools guide maintenance and reliability experts to make sustainable and efficient coating choices. In the LCA process, specialists evaluate the environmental impact of coating solutions throughout their entire life cycle. This provides critical insights that help asset owners select solutions that protect their infrastructure and minimize their environmental footprints. This holistic approach includes assessing the impact from raw material extraction through application and use to eventual disposal.
Complementing this, digital modeling employs advanced computational tools to simulate the performance of coatings in various environments. This predictive capability allows for optimized coating systems specifically tailored for different applications—whether protecting a wind turbine from salt spray or ensuring that an oil rig's understructure remains impervious to chemicals and seawater. By forecasting the long-term behavior of coatings, digital modeling supports proactive maintenance strategies, reducing the likelihood of unexpected failures and ensuring steady, reliable operations.
Case study: Extending the Life of Offshore Wind Assets
A recent evaluation assessed the performance of styrene-free unsaturated polyester (UPE) glass flake coatings against reinforced novolac epoxy coatings for protecting offshore wind tower foundations. These coatings underwent comprehensive internal and third-party testing, including abrasion resistance, cathodic disbonding and impact damage, adhering to industry standards such as ASTM and NORSOK. Results showed that reinforced novolac epoxy coatings offer superior resistance to abrasion, stress cracking and corrosion compared to UPE coatings. Choosing coatings that meet rigorous performance criteria enables stakeholders to extend the service life of wind towers, reduce maintenance costs and support the long-term success of offshore wind projects.
Looking Ahead
A specialized protective coatings partner helps operators maximize asset lifespan while meeting sustainability goals. The right coating system protects and extends equipment life, reducing the need for replacements and supporting circular economy principles. By keeping critical components in service longer, operators achieve both economic and environmental objectives.
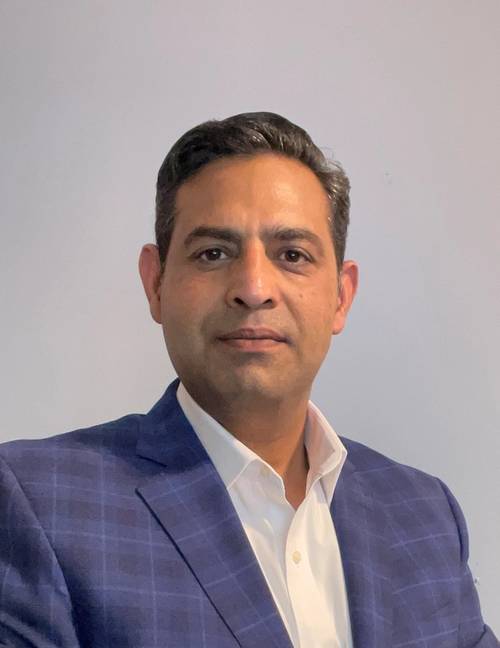
About the Author
Anurag Raj is PPG’s Customer Sustainability Business Partner for Protective and Marine Coatings. He leads and supports PPG’s and its customers’ sustainability targets. To learn more about how PPG helps clients make choices that align with their sustainability goals, visit here. Learn more about Protective and Marine Coatings here.