Robotics
Inspection, Maintenance & Repair
Keeping Watch
No longer just FIFO workers, subsea vehicles are settling in for long-term IMR assignments.
By Wendy Laursen
Saab UK’s Seaeye SR20 can be quickly adapted to a variety of tasks whether it’s conducting detailed inspections, performing complex maintenance work or handling heavy-duty repairs and equipment.
Image courtesy Saab SeaeyeSaipem’s legion of subsea drones can operate continuously for up to 12 months, working 12-hour shifts and then recharging for 12 on a docking station located on the seabed.
The Hydrones are designed for inspection, maintenance and repair (IMR) activities at depths of up to 3,000 meters. The AI-enabled vehicles can be the size of a Fiat 500 and can perform complex tasks in challenging conditions.
Beyond subsea dormitories, Saipem plans to pair the drones with advanced stationary monitoring solutions, creating a subsea Internet of Things to efficiently assess the integrity of subsea infrastructure and drive operational decisions with greater automation and autonomy. Mauro Piasere – Chief Robotics and Industrialized Solutions, says: “Thanks to these drones and other advanced monitoring solutions, Saipem can enable a deep digital transformation of the subsea world where collected data are used to monitor and manage infrastructures more effectively.”
Image courtesy SaipemThanks to these drones and other advanced monitoring solutions, Saipem can enable a deep digital transformation of the subsea world where collected data are used to monitor and manage infrastructures more effectively. - Mauro Piasere – Chief Robotics and Industrialized Solutions, Saipem
Sensor technology is keeping pace with the needs of autonomous operation, with Teledyne finding increased demand for synthetic aperture sonar, high specification cameras and subsea LiDAR. Arnar Steingrimsson, Vice President of Sales - Marine Vehicles at Teledyne Marine, is also seeing demand for deeper operations, and along with longer stay times, this means bigger batteries and bigger vehicles.
Using AI, Teledyne has developed an autonomous system for identifying and tracking pipelines. “Grid surveys over an area don’t guarantee the best data over the object of interest,” says Steingrimsson. But while offshore energy companies are looking for operational gains, Steingrimsson is also seeing a greater interest in surveillance monitoring, sparked by recent sabotage events.
AUV residents are ideal. It’s not feasible to have ships monitoring subsea infrastructure long-term, and the market is already responding. In response to Europe’s growing security challenges, for example, German company FLANQ has just launched a suite of commercial-off-the-shelf USVs, drones and sensor payloads, powered by AI.
Image courtesy Saab SeaeyeAs the market shifts toward greater automation, we're seeing more emphasis on automating both data acquisition and data processing to deliver actionable insights quickly. - Jon Robertson, Managing Director, Saab Seaeye
Crewed offshore support vessels are likely to see their workload reduce with the increasing use of USVs. Lloyd’s Register recently granted Approval in Principle to Brazilian company TideWise for its 24-meter DP2 USV which has an endurance of 35 days and the ability to deploy a work-class ROV at depths of up to 2,500 meters. Like AUVs, the endurance of USVs in increasing.
Saab UK's recently released Seaeye SR20 ROV is designed with USVs or minimally crewed vessels in mind, says Jon Robertson, Managing Director at Saab Seaeye. It is also compatible with the latest camera and perception technologies, which means it can deliver high-quality, high-resolution inspection data. “As the market shifts toward greater automation, we're seeing more emphasis on automating both data acquisition and data processing to deliver actionable insights quickly.
These advancements are helping to shape the future of the IMR market by enabling more efficient, remote and continuous operations.”
Robertson says the SR20 has a high payload capacity and can be quickly adapted to a variety of tasks whether it’s conducting detailed inspections, performing complex maintenance work or handling heavy-duty repairs and equipment. It can remain stable, even in strong currents, to capture accurate data and perform precise interventions. The SR20 also comes equipped with dual Seaeye eM1-7 electric manipulators, and it will be compatible with subsea exchangeable tools in the future.
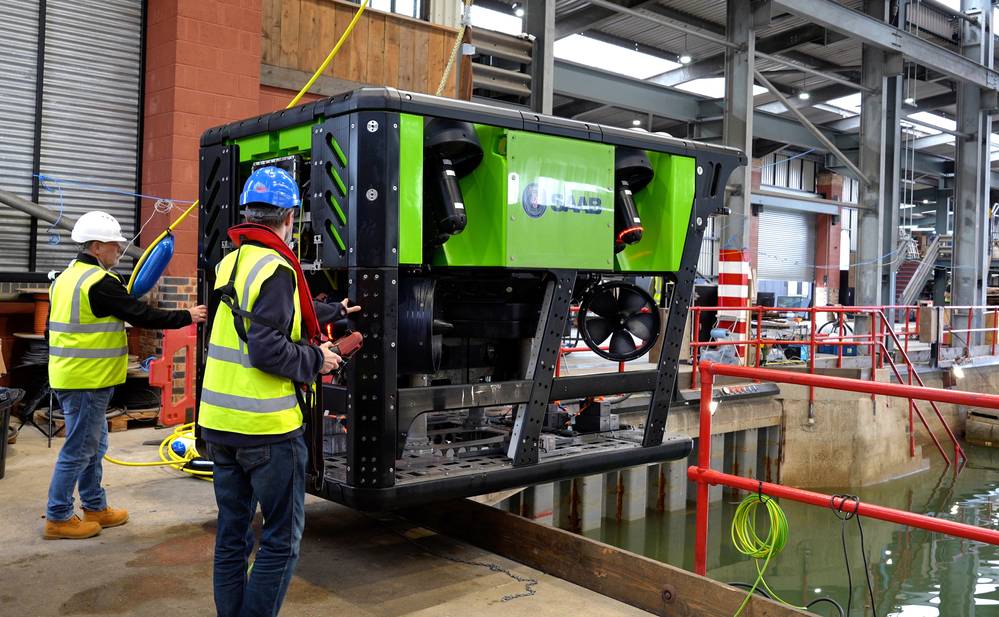
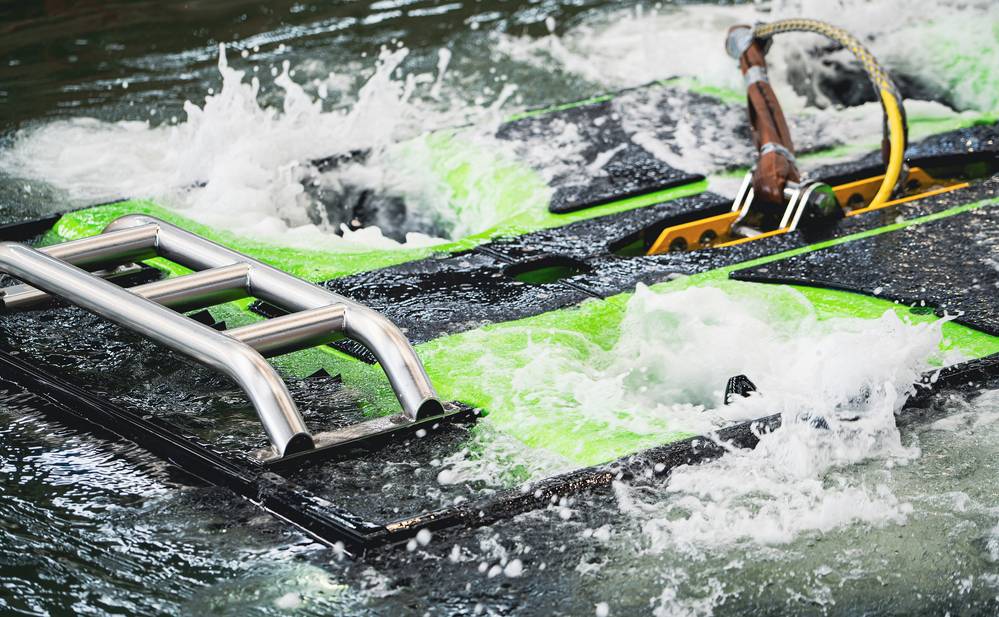
Image courtesy Reach RoboticsRigging, cutting, cleaning, NDT, reduction of biofouling — this can all be achieved by smaller ROVs with manipulators like Reach Robotics'. - Curtis Opsahl, Sales Engineer, The Americas, Reach Robotics
Reach Robotics has released its new X7 subsea manipulators which enable operators to execute dexterous intervention operations that traditionally have been performed by either divers or work class ROVs. “It seems many groups are trying to eliminate the risk and subsequent cost of human divers in the water,” says Curtis Opsahl, Sales Engineer, The Americas. “And it appears that this is achievable for most tasks. Rigging, cutting, cleaning, NDT, reduction of biofouling — this can all be achieved by smaller ROVs with manipulators like Reach Robotics'.
“By using a one-man-portable ROV to efficiently perform light intervention tasks, such as attaching lifting leader lines or threading hydraulic couplers, we eliminate the need for divers in the water or the expense of a work class ROV and its support vessel.”
Even where specific force modulation, situational awareness or tooling requires a diver, these systems can be a force multiplier by preparing the areas or doing some prework, not too dissimilar to a surgeon's assistant, he says. “And we're only on the cusp of what these systems can do. While there may always be a need for divers in certain situations, if we can reduce that reliance by, say, 75%, we're eliminating a material amount of human risk.”
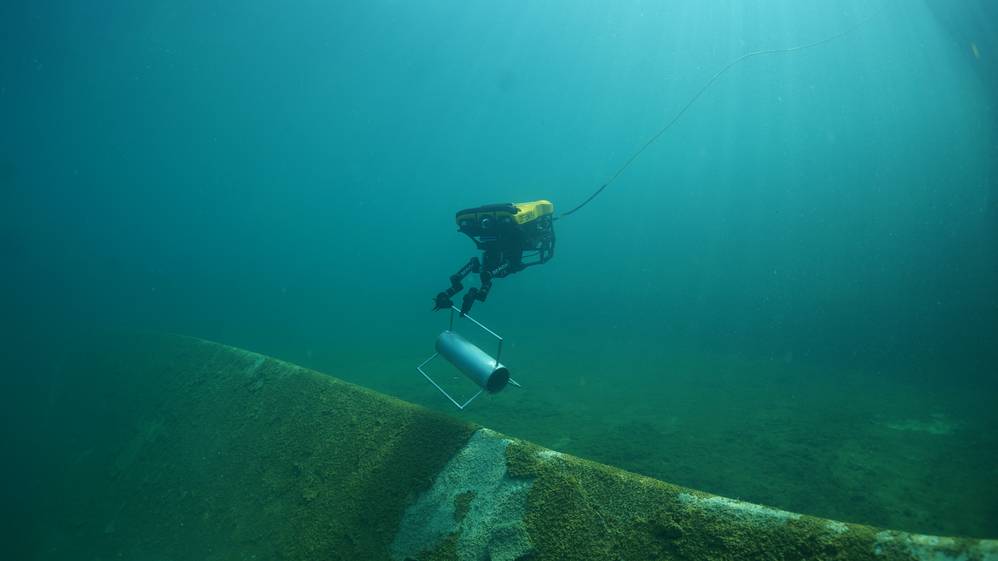
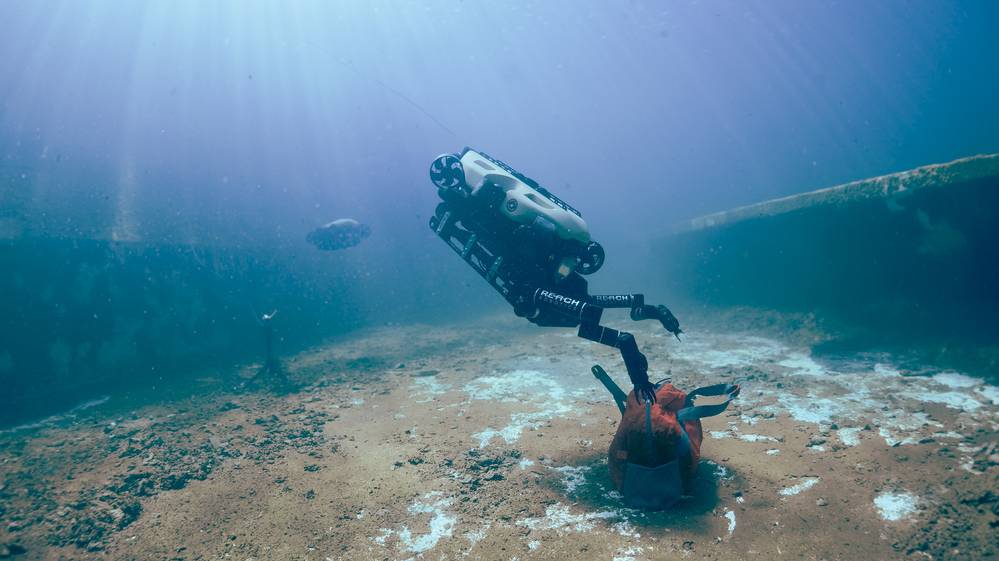
Oceaneering Product Manager Iain Wylie says the company’s Freedom AUV can hover and work in six degrees of freedom so as it approaches subsea structures, like pipeline manifolds, it can get close to the asset and capture a 360-degree image of the structure before continuing with its survey.
Inspection is the backbone of an integrity program, ensuring the damage mechanisms are monitored and fatigue models are accurate, he says, and the Freedom AUV helps reduce the cost of data capture allowing for more cost-effective compliance or more frequent inspections to support data driven risk-based inspection.
The more AUVs achieve, the more is expected of them. “Once we start accessing sites with the AUV we naturally will get pushed to do more than inspect,” says Wylie. “Our engineered solutions group stands ready to handle these requests and see what we'd be able to do with what we have. Recently the team was able to cut a 6" pipe and install a pressure retaining plug deployed by a third party V8 observation class ROV.”
Oceaneering is considering deploying its Freedom™ AUV off assets such as FPSOs and platforms to reach areas within radius without needing additional vessel support. “In my experience, one of the biggest issues facing maintenance and repair is the cost and opportunity of access, usually via vessel,” says Wylie.
Remote and autonomous systems will lead to a reduction in costs and risk, he says. “Vessels can be much smaller with less accommodation required to achieve the same outcome. Maintenance and repair is already done remotely from ships by ROV, this just takes people another step away.”
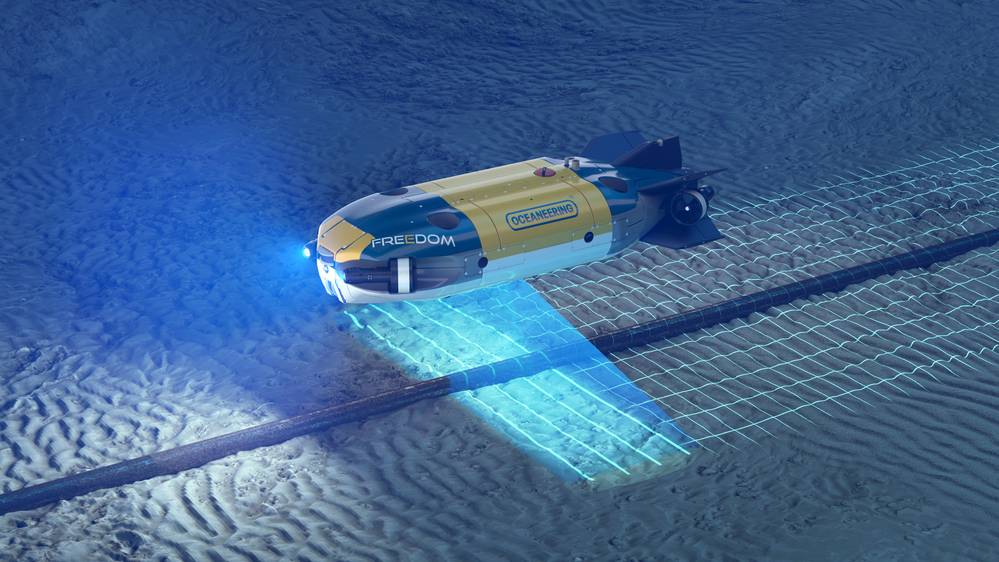
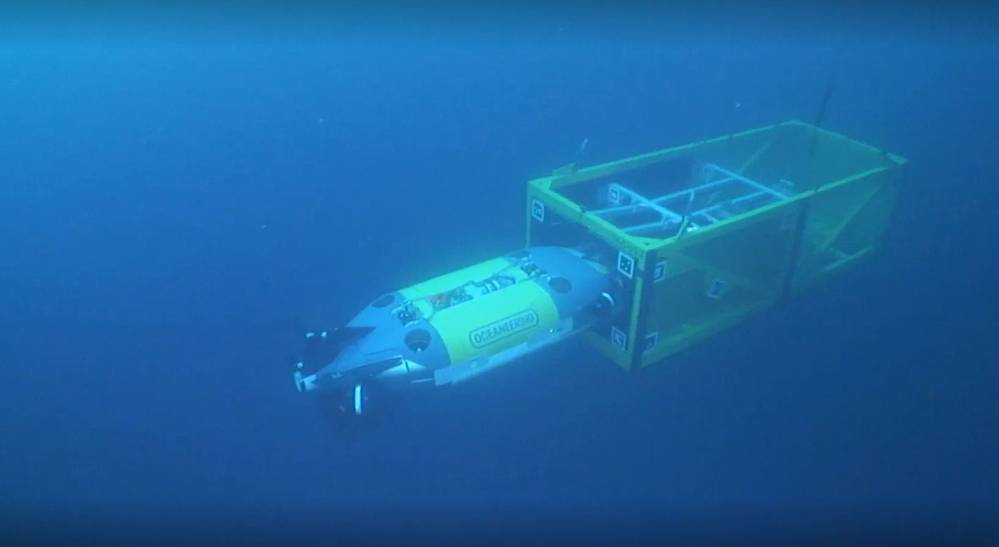